■工研院 / 郭宗勝 博士
序言
射出成型製造是高度依賴製造端(OT) 領域知識(Domain Knowledge) 的產業,這也是成型產業邁入智慧製造的一大挑戰,因為若單獨從資訊端(IT) 角度想要打造智慧製造方案往往會事倍功半,無法為射出成型廠創造智慧化的最大效益。
有鑑於此,本文將從製造面與管理面雙贏的角度切入,期望透過IT 與OT 跨領域的技術融合能夠加速成型產業智慧製造的落地。並且將以工研院智慧成型系統實際導入汽機車零組件廠為案例,說明如何藉由IT與OT 融合技術協助射出成型廠進行數位轉型,佈局全球輕量化與高值化市場。
IT 與OT 融合技術需求
在思考IT 與OT 為何需要融合時,我們可以分別從「OT 為何需要IT」與「IT 為何需要OT」等兩個角度切入來看。
OT 為何需要IT首先,先從如何導入IT 技術解決成型加工製造端(OT)痛點的角度說起(OT 為何需要IT)。傳統成型製造產線上過度依賴人力解決生產品質問題,從試模、量產、品質檢測到報工,都過度依賴人力作業造成新產品來回修模影響產品開發時程、依經驗調機造成量產品質不易穩定、巡檢方式導致不良品流出造成客訴。因此,若射出廠願意透過數位轉型來導入IT 技術發展各種智慧功能將可有效改善製造端面臨的問題。以試模為例,透過各種感測器擷取即時成型曲線,可以將模具內的成型過程可視化,以數據協助調機人員進行科學化調機作業加速產品量產。而量產階段產生不穩定問題,則可透過感測特徵擷取與分析,即時針對製程環境發生變異時進行示警,避免不良品的大量生產。而在品檢階段,以收集每模次感測數據進行成型品質推論,即時察覺每模次品質問題,解決巡檢或人力檢測的不足。如此一來,製造端就能明顯感受IT技術導入的效益。
IT 為何需要OT
接著,來看如何以OT 數據創造IT 資訊端價值(IT 為何需要OT)。在成型製造的過程中,如烘料、上模、射出、保壓、冷卻等,都可從中取得各種物理變化的數據,包含電壓、電流、壓力、溫度、位置、甚至聲音與影像。只是在這龐大的資料中,若沒有結合OT端領域知識,是很難從龐大的數據中,找到實際反應痛點的資訊或特徵。因此,在數位轉型過程中,射出成型廠導入各種資訊系統,如ERP、MES、PLM……等,若忽略製造端資訊的重要性,將讓資訊系統導入的價值大打折扣。接下來本文將會以君牧塑膠科技的數位轉型經驗為案例,說明如何運用OT 數據提升資訊端管理效率。
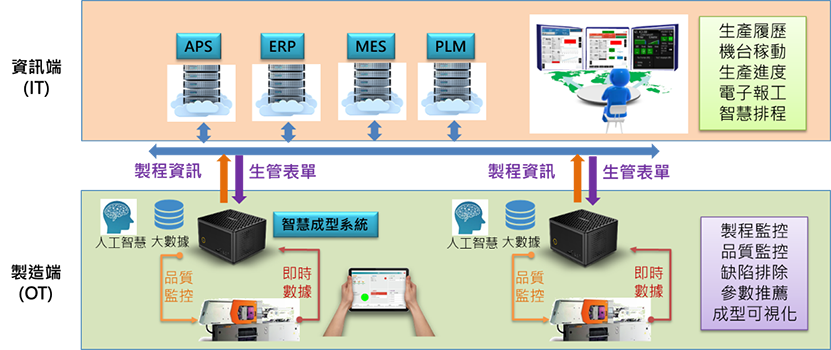
打造智慧化成型產線應用案例
君牧塑膠科技是一家成立超過35 年的專業射出成型廠,憑藉著高強度複合塑料產品的開發實力深獲國際車廠肯定,成為日本YAMAHA 與光陽的一級供應商。君牧塑膠科技在十幾年前即投入數位轉型,陸續導入ERP、PLM、MES 等資訊化系統,不過在IT 與OT 整合上,一直沒有找到合適的解決方案。為追求公司在高度競爭的全球市場上能夠持續成長,君牧塑膠科技 黃董事長經常參加國際重要展覽以瞭解國際技術的發展趨勢,也因而看到國外大廠在智慧製造技術上的進步,更是憂心臺灣產業的未來。可是國外設備大廠的智慧解決方案導入費用根本不是臺灣中小企業所能夠負擔的,而臺灣廠商的方案往往偏重生產管理,無法兼顧製造端之需求。
目前工研院發展的智慧成型優化系統似乎是比較接近黃董事長理想中的IT 與OT 整合方案,因此從108 年開始進行導入,經由雙方共同的努力,慢慢開始看到一些成果。
在製造端方面,如圖2 所示,透過線上品質檢測可以即時發現生產上的問題,甚至可以發現一些人力所無法檢測到的問題;而在資訊端方面,如圖3 中所示,透過製造現場機臺的自動化報工,將可解決人力作業方式的即時性與誤報問題,讓公司即時掌握生產進度與瓶頸。此外,藉由機臺自動回報的製程參數與感測數據,還可以建立每件產品的完整產品履歷,確保未來產品發生問題的可追溯性,這對建立客戶對公司的信任很重要。
藉由工研院智慧系統的導入,我們也開始累積君牧的生產大數據,未來我們的功課就是要從這些數據中去創造公司產品的價值,以產品價值取代價格的競爭才能為臺灣成型產業開創一條通往藍海的道路,這也是君牧塑膠科技的目標。■
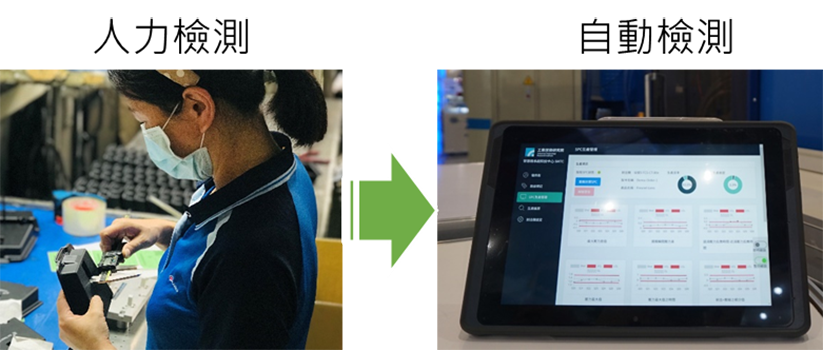
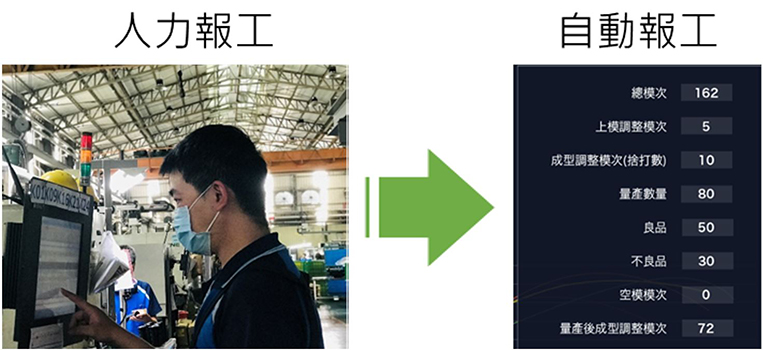
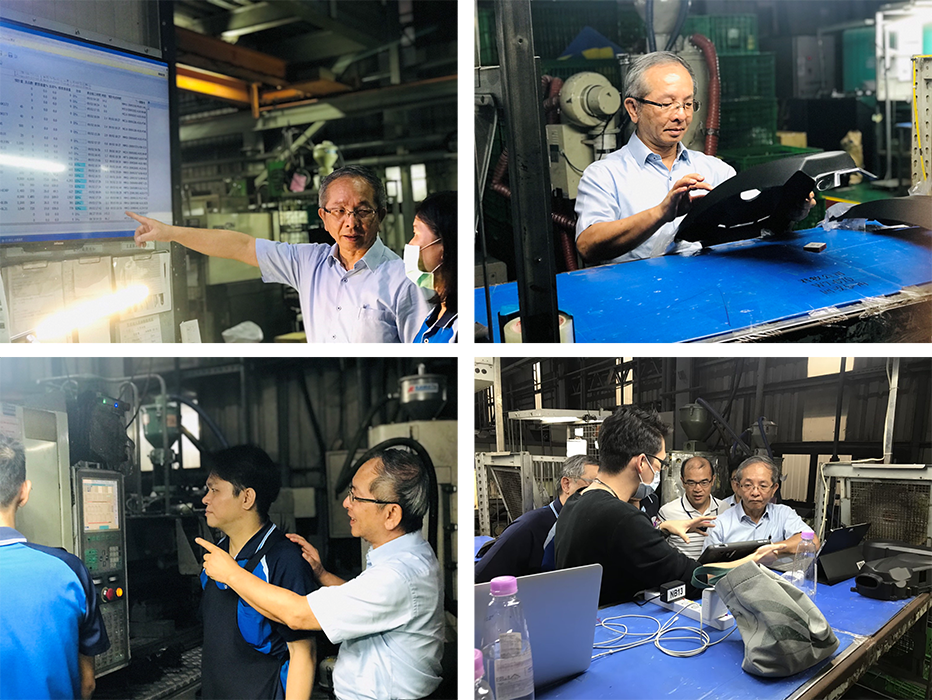