■臺灣科技大學 高速3D列印中心
前言
積層製造產業在疫情時代的催化下加速導向工業化量產需求,其自由的造型可塑性,從醫療器材的呼吸器、面罩架、鼻咽拭子或醫用轉接器等,皆可見3D列印的相關應用,其中更以鼻咽拭子最具代表性,透過符合FDA安規之列印用材料可於2小時內列印400支拭子,提供龐大的市場需求。在此次台灣積層製造設備大展本中心與T3D台科三維公司合作,首次展示因應工業需求而開發的三種高速生產技術:「液晶式大面積光固化列印技術」、「極低分離力薄膜」與「高速成型光敏樹脂」。以提供積層製造的量產解決方案,大幅提升生產效率。
液晶式大面積光固化列印技術
光固化3D列印技術發展初期,列印面積均不大,多以珠寶鑄造模具或者齒科模具等較小型的列印物為列印對象。隨著積層製造技術的發展,各式3D列印機廠商逐漸開始以更大的列印面積為機臺發展方向。可列印面積的放大在積層製造技術中有兩項主要優點:
- 可列印尺寸更大的單一零件:使得3D列印的零件比起以往的牙模、戒指等小型物品,可以轉為列印大型設計家具或是機械大型部件等零件。
- 提高單位時間,小零件的列印生產量:更大的成型面積,可以使得單位時間內列印出更多的相同零件,達到量產的目的。
但增加列印面積,不論是SLA,DLP或者是LCD形式的光固化3D列印機都具有一定的技術挑戰存在。目前市售較常見的大型光固化3D列印機,依照成型方式大概分為以下三種:
- SLA光固化:335X200X300mm,Formlabs (Form3L) 大尺寸光固化3D列印機;
- DLP光固化:255X235X190mm,揚明光學 (MIICRAFT) Advance 255;
- LCD光固化:200X125X200mm,Phrozen Sonic XL 4k 2022。
但不論是哪種3D列印機,最大的成型長度也很難超過400mm。目前高速列印中心成功開發31.5吋的超大型LCD光固化3D列印機,擁有689.4X392.85X500mm的成型空間,約為Form3L的6倍成型體積,4倍的成型底面積。以鞋模為例,可以列印最大39隻42碼的鞋底模具。以此看來大面積的3D列印可以大幅加快單次列印的生產量,是光固化3D列印的發展重點之一。
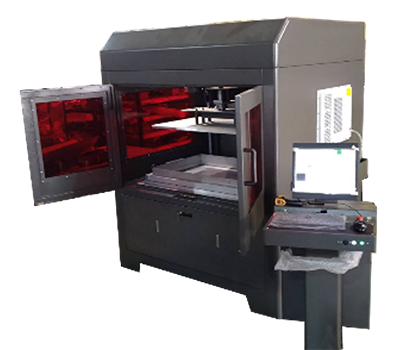
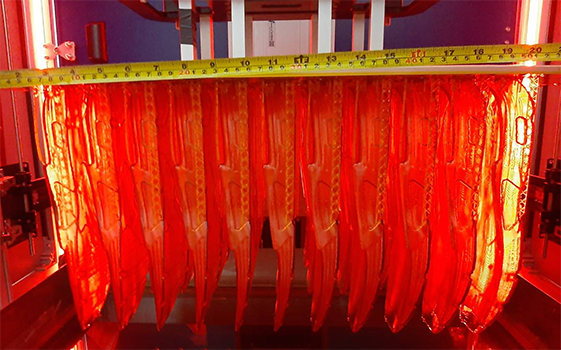
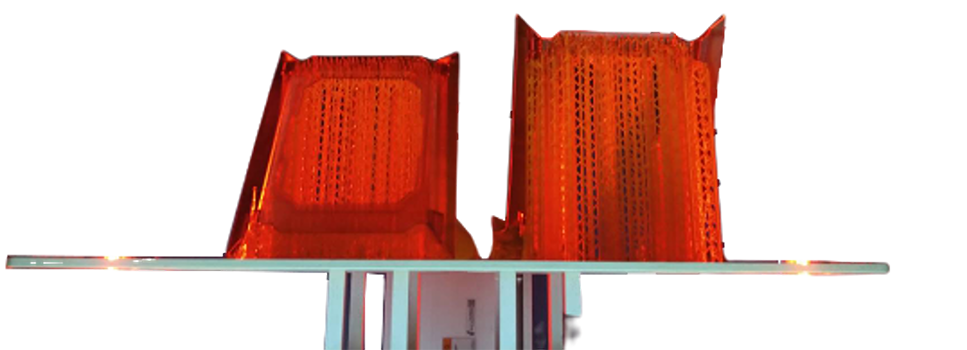
極低分離力薄膜
臺灣有許多廠商投入下照式光固化技術,其中也有廠商對於超高速這項技術投入研發,而臺灣的研發單位對於高速下照式光固化列印技術亦給予正向的肯定,認為這項技術將有望成為全球推動「工業4.0」及「智慧機械」的重要技術之一。
下照式光固化技術在積層製造中有著最佳的列印精細度,然而現行設備在提高生產率上仍面臨挑戰,提高生產率最顯著的方法就是提升列印速度,但速度的提升總受限於列印層脫離樹脂槽底的拉應力問題,因此現今還是大多應用於小面積尺寸的客製化列印。
發展高速下照式光固化技術,不僅能達到大量客製化,讓使用者能快速拿到成品,也能隨時因應市場變化達到降低庫存,不論是用在產品原型的製造或者是在模具的生產,都能大幅縮減時間,也等於成本的降低,達成生產中各方面的效率提升。
為解決下照式光固化列印之拉應力問題,達成高速下照式光固化技術,本中心研發製作了超疏滑薄膜改善拉應力的產生,藉著低表面能薄膜降低硬化光敏材料的黏附,並由穩定劑維持低表面能的結構,完成低表面能薄膜達到超疏水與疏油界面,並可達成網狀物件的連續穩定列印,能達到每分鐘1.5公分的列印速度。
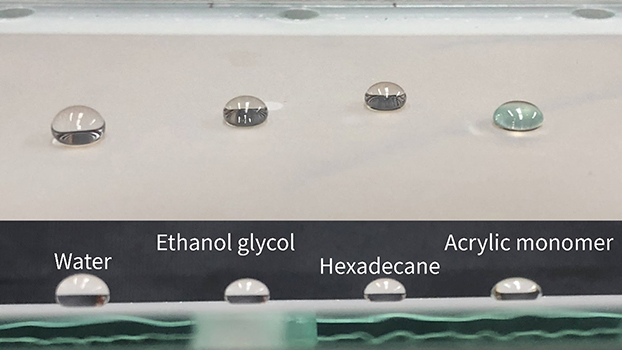
高速成型光敏樹脂
為降低LCD面板在光固化列印時的損耗,我們開發了可見光3D列印機及適配的可見光樹脂。該樹脂具有低黏度、低氣味、固化快速等特點,與我們的可見光3D列印機同時使用時,精度可媲美紫外線光源的3D列印機,解決了一般可見光3D列印機普遍精細度不佳的缺點。同時因流動性佳,可進行大面積3D列印而不會因回流問題而需要過長的列印時間。此外,該樹脂於室內自然光下仍有一定程度的穩定性,因此無需於完全無光的環境下操作,僅需稍暗的環境即可。
另外,我們也開發了紫外光源3D列印機的高速樹脂,該樹脂同樣具有低黏度、低氣味、固化快速等特點,於1mW/cm2的紫外線光源下便可達到每小時7-10公分的列印高度。該樹脂固化後可與離型膜快速分離,同時因流動性極佳,可有效縮短成型平臺移動以及等待樹脂回流的時間,每100微米的固化時間也僅需2秒左右,使得整體列印時間大幅縮短,增加每單位時間的產量。此樹脂可用於常見的LCD 3D列印機臺,無需使用特殊機臺。
結語
本文僅介紹部份的技術內容,歡迎有興趣的讀者於展會期間前來做進一步的了解,未來我們將繼續整合以上三種高速列印技術,以期能於產業中實際的應用,讓生產過程能確實的達成客製化數位製造與適量製造,降低供應鏈的囤貨壓力,也間接降低生產成本。