■中原大學智慧製造中心
背景
加工工具機需不斷朝向低成本、高精度、高速化及技術提升方向前進,而目前CNC加工工具機也不斷朝向高速化及高精度化發展,使得工具機在加工過程中溫升速度提升,溫升造成之變形與誤差影響機臺的精度也會相對明顯,溫升熱變形誤差佔工具機總體加工誤差60-70%,如能作有效補償可大幅提升模具加工精度,高速化發展的主軸切削回轉數往往高於2萬轉/分以上,進給也可高達120公尺/分,在這些高轉速、高進給的情況下,工具機的溫升速度將提高,為了有效提高工具機精度的穩定性,將溫升熱變形所造成之誤差進行補償是對精度非常重要的一部分。
溫升熱變形不單只有機臺內部CNC加工機臺運作時所造成溫度變化與溫升熱變形所造成的誤差而已,當有著不同的室溫時,當時所建立的溫升熱變形模組並不能在各種不同室溫下有良好的補償,但在每個不同溫度時都去做溫升熱變形補償迴歸方程式,必然需要花費非常多的時間在建立各個溫度的迴歸方程式,也不能利用以往的資料進行有效的預測。於是便開始研究是否能利用類神經網路訓練的方法將各種溫度套用在一個程式裡。
過去的溫升熱變形較難將環境溫度變化的影響考慮在內,為了提升溫升熱變形補償的準確性,可應用Artificial Intelligence人工智慧的方法將影響性考慮在內,如何將數據進行有效分析並結合AI人工智慧,使資料處理上有更有效的運用將是本研究的重點。
研究方法
溫升熱變形中,數據為線性可分離,故不需要使用太多層數便能夠擁有很好的訓練成果,故將隱藏層設置為2層,同時第一層與第二層設置相同的神經元數量能讓訓練上更容易成功,將同時調整神經元的數量並透過損失函數來比較神經元的數量所帶來的準確性。透過實驗量測建立當下環境溫度、各軸溫度感測器溫度變化與各行程節點變形量。
實驗與驗證結果
本次實驗驗證將分成三種實驗進行驗證。第一種實驗將驗證「模型預測之準確度」,在收集訓練模組時將收集資訊分為訓練數據與預測數據,透過訓練數據訓練類神經網路,並利用類神經網路進行收集數據外之預測,將類神經網路預測與實際收集數據進行比對來了解模型的預測能力。
第二種實驗為驗證「儀器補償功能」,主軸與伺服軸會用不同的方式進行補償,而此次實驗驗證能夠確認各軸之補償模式是否能夠將溫升熱變形所造成變形量進行良好的補償。
第三種實驗為「實際切削驗證」,實際切削驗證將使用大工件來增加加工行程,行程越長變形量越大,藉由觀察所切削之外形精度來檢視補償的有效性,實際切削將分為兩部分:X、Y方向熱變形補償實切、Z方向熱變形補償實切,並在不同的環境因素下進行切削,比較點與點間距離誤差來檢視補償的有效性。
圖1為主軸數據分析,橘色線段為類神經模組訓練所預測之數據,紅色線段為雷射量測數據,主軸觀測溫度溫升0°C至2°C有較好的預測,誤差為0.5µm,2.2°C至3.2°C預測最大誤差為1.1µm。圖2為X軸數據分析,橘色線段為類神經模組訓練所預測之數據,藍色線段為雷射量測數據,最大誤差為1.01µm。圖3為Y軸數據分析,藍色線段為類神經模組訓練所預測之數據,橘色線段為雷射量測數據,最大誤差為1.8µm。圖4為Z軸數據分析,藍色線段為類神經模組訓練所預測之數據,橘色線段為雷射量測數據,最大誤差為1.3µm。
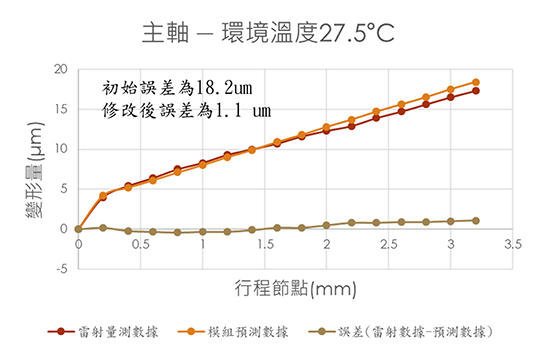
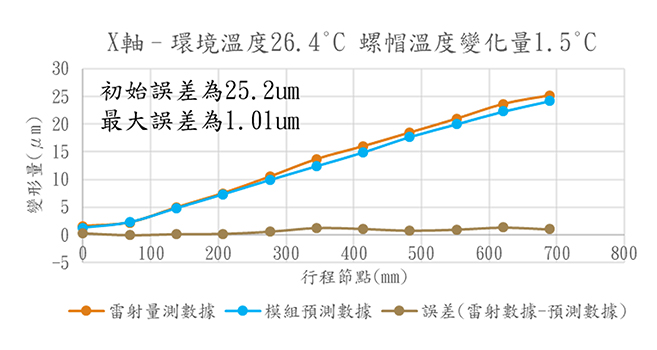
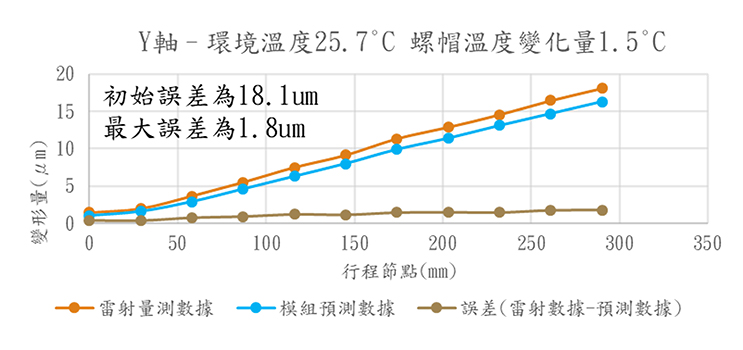
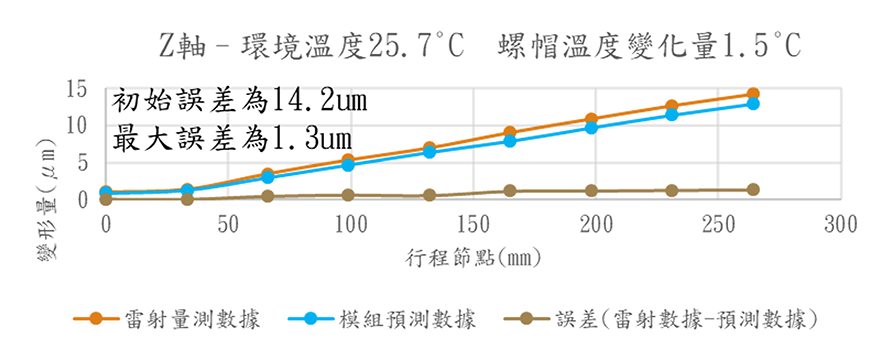
實切驗證
實切驗證規劃使用材料為鋁之矩形工件,切削條件如表1。如表1所示,對X、Y方向的實驗規劃為在初始冷機時,先在工件四個角落分別鑽四個直徑16mm、深度30mm的圓孔。X方向孔心相距350mm,Y方向孔心相距150mm,由圖5三層圓孔圖可看出,圓孔總深度30mm,擴孔時機為初始冷機時進行第一次擴孔。利用在不同切削深度及不同圓孔直徑下進行循圓切削擴孔,由於主軸與伺服軸因溫升產生變形,因此從擴孔後圓心的偏移量可看出溫升變形的影響,及補償前後的差異。
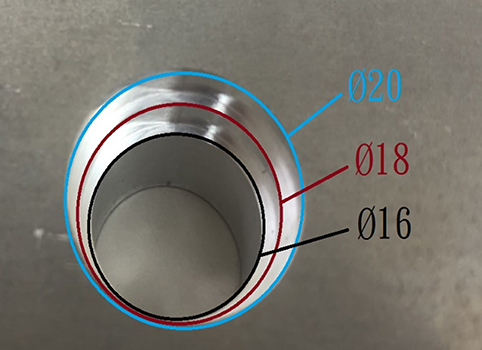
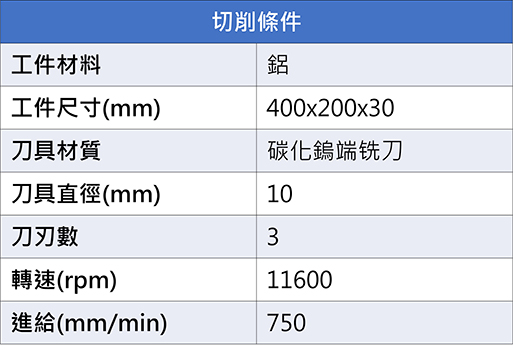
為方便三次元量測圓孔之圓心,實驗設計圓孔為三層不同深度之同心圓孔,使用直徑10mm之端铣刀對初始冷機時所鑽之圓孔進行循圓切削擴孔,依據擴孔順序,左下角為圓1、右下角為圓2、右上角為圓3、左上角為圓4,第一次擴孔完成後機臺進行20分鐘的溫升,四項實驗將分別切削,溫升完畢後進行四項實驗之實際切削進行第二次擴孔,圓孔深8mm、圓孔直徑18mm,依據擴孔順序,左下角為圓5、右下角為圓6、右上角為圓7、左上角為圓8。第二次擴孔完成後將機臺進行20分鐘的溫升,溫升完畢後進行第三次擴孔。圓孔深8mm、圓孔直徑18mm,依據擴孔順序,左下角為圓9、右下角為圓10、右上角為圓11、左上角為圓12,即完成X、Y方向熱變形補償實切。
表2為環境溫度26℃有補償時之距離比較,第一次銑孔孔1~孔2之X距離為349.988mm,第二次銑孔孔5~孔6之X距離為349.993mm,第三次銑孔孔9~孔10之X距離為349.996mm,將冷機時孔1~孔2之X距離設為0相對於補償前孔5~孔6,補償後孔9~孔10。補償前孔5~孔6誤差為0.005mm,補償後孔9~孔10誤差為0.008mm;同樣第一次銑孔孔2~孔3之Y距離為149.978mm,第二次銑孔孔6~孔7之Y距離為149.983mm,第三次銑孔孔10~孔11之Y距離為149.986mm,將第一次銑孔孔2~孔3之Y距離設為0相對於補償前孔6~孔7,補償後孔10~孔11。

表3為環境溫度30℃有補償時之距離比較。從表中可以看出冷機時孔1~孔2之X距離設為0相對於補償前孔5~孔6,補償後孔9~孔10。補償前孔5~孔6誤差為0.011mm,補償後孔9~孔10誤差為0.013mm。
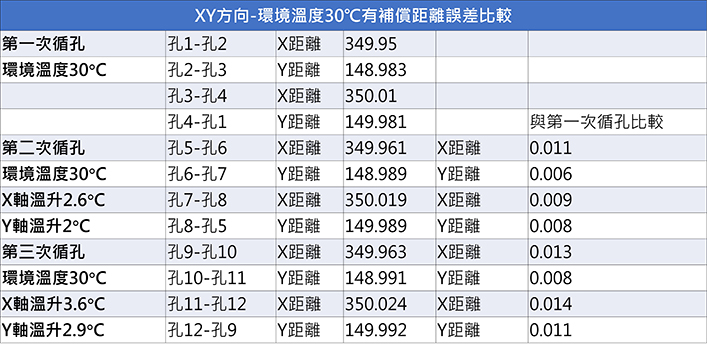
環境溫度26.5℃-Z方向有補償如表4所示,依據切削平面順序,分別有平面1~平面4,平面1為z=0mm之基準面,平面2為預定切削深度z=-150µm,平面2實際切削為-150µm,有0µm的誤差,平面3為溫升20分鐘後之切削平面,實際切削深度為-116µm,與預定深度-150µm有-10µm之誤差,平面4為溫升20分鐘後之切削平面,實際切削深度為-161µm,與預定深度-150µm有-11µm的誤差。
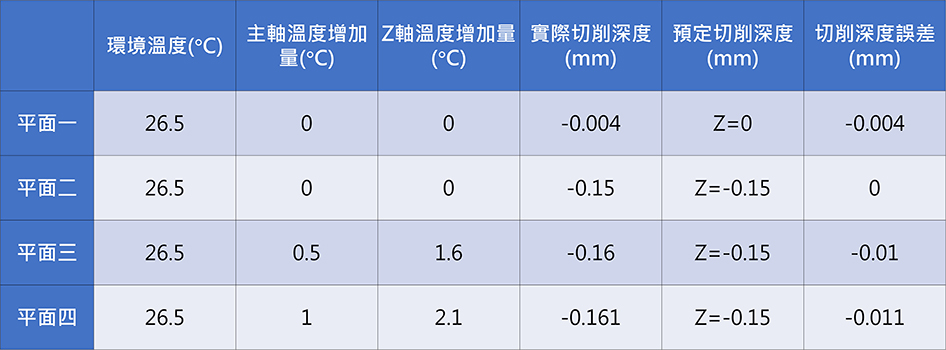