■工研院南分院 / 吳宗明 資深專案經理
前言
積層製造(Additive Manufacturing, AM)或稱3D列印,技術問世迄今已超過30年,由於可以製造列印傳統減法加工工藝無法達成之複雜形貌與內部結構的零件,近10餘年來更受到廣泛矚目並引領產品創新設計與產業應用的風潮。隨著積層製造相關軟硬體技術的持續發展與進步,積層製造技術的產業應用也從早期快速打樣(rapid prototyping)及小量客製化製造,逐漸轉向數位化製造生產及適量客製化生產,特別是在航太產業、醫材與植體、汽車產業及模具等產業領域應用範圍也有著明顯進展與擴散,隨著積層製造技術的發展,成功應用案例的發表也更趨多元。
以美國材料和試驗學會(American Society for Testing and Materials, ASTM)訂定之七大類型積層製造技術類別來看,由於金屬積層製造技術能直接將複雜形貌與特殊結構的金屬元件一次成型,近十年來製造設備與服務市場一直在顯著增長,並且在可預見的未來十年內很可能會扮演多個產業重要加工製造角色,製造生產活動預計在2030年增長到每年超過500億美元。
其中金屬粉床熔融技術(Metal Powder Bed Fusion, Metal PBF)的應用在世界各國產官學研在軟硬體開發的持續投入下,可供使用者選用的金屬粉體材料類別與供應廠商愈來愈多,產品應用範圍也愈來愈廣。儘管金屬粉床熔融製造技術具有很大的潜力與應用領域,然而金屬粉床熔融成型仍存在著諸如產業相關標準訂定尚不完備、製造生產力低、零件品質重現性差、幾何精確度有待提升、零件的缺陷與機械特性不確定性等亟待解決的技術問題和挑戰,這些問題點與挑戰遲緩或阻礙了相關產業導入金屬粉床熔融技術的時機點[1-2]。
因此,實務上進行金屬粉床熔融製造需考慮到此項製造技術能力的獨特性與限制,諸如擺盤方向與位置、支撐面的臨界角度、最小孔洞直徑、最大深寬比、最小壁厚與最小特徵尺寸等,重新思考如何從設計到製造工作流程的思維模式轉換與加工製作的限制已達成有效的管理,包括運用製程預前模擬及製程參數最佳化,以最大限度地減少因試誤方式增加的設計修改,亦即在設計階段以金屬積層製造設計思維(Design for Additive Manufacturing, DfAM)進行產品設計與評估,粉床監視補償控制以確保製作時金屬粉體層層堆疊與熔融的品質,並輔以金屬粉體周邊設備提升粉體吸供篩的自動化程度與工作效率。
透過不同的工作流程階段評量產生的資訊進行最佳化評估,以大幅降低因反覆的設計修改與重工,所造成的人力、材料與列印時間的成本,來提升屬粉床熔融製造的可生產性、品質與效能[3-4],亦即在製造階段以金屬積層製造思維(Manufacture for Additive Manufacturing, MfAM),進行產品製作品質管理。
近幾年工研院南分院即針對金屬材料製程參數最佳化、預前熱應力模擬技術、粉床監視補償控制與金屬粉體自動吸供篩裝置等項技術的進行開發,提供改善與逐步移除上述產業化瓶頸與障礙,以加速金屬粉床熔融技術的產業化,並建立臺灣自主的金屬粉床熔融製造技術完整決方案,如圖1所示。
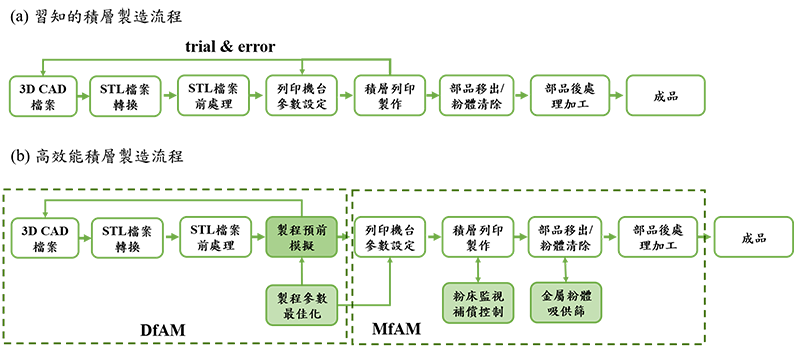
製程參數最佳化技術
習知的積層製造流程(如圖1(a)所示),將3D CAD設計圖檔轉換成STL格式載入後,工程人員即依據經驗進行製程前處理,其中包含製程參數設定、掃描策略與擺放方向決定以及支撐結構設計與補強等。另外,機臺及粉體來料變異等因素也需仰賴有經驗的工程人員調控製程參數,要維持生產效率與品質實在不易。
早期使用國外金屬粉床熔融設備與廠商銷售的專用金屬粉體是綁在一起,使用者視需要購買所需的金屬粉體與製程參數資料庫,以確保所製作零件品質,卻也某種程度限制了金屬粉床熔融製造技術的廣泛採用。隨著越來越多的設備商與材料供應商進入市場,設備與使用材料間的限制逐漸被打破,設備使用者可從其他材料供應商購買粉體,但新材料通常是透過實驗試誤法,需花費數週甚至數個月時間進行製程參數分析,試誤過程耗費成本且效率極低,且所找到的可能是局部範圍的最佳參數,而非全域的最佳參數組合。
工研院整合南分院、材料與資通三個單位開發製程批次參數優化技術,利用Random forest演算法分析眾多製程參數對拉升強度的關聯性,篩選出需優先調控的製程參數,如圖2所示。抗拉強度模型(Gaussian process)與變形模型(Support vector machine)用於製程批次參數優化技術中,利用優化演算法搭配這兩個模型找出合適的推薦參數,目前已完成製程批次參數優化技術模組1套,如圖2所示。經實際驗證,無預熱鋁合金6061拉力棒製作,拉伸強度可突破先前以習知試誤方式找出的最佳製程參數,列印最佳值提升47.3%。製程批次參數優化執行流程如圖3所示。
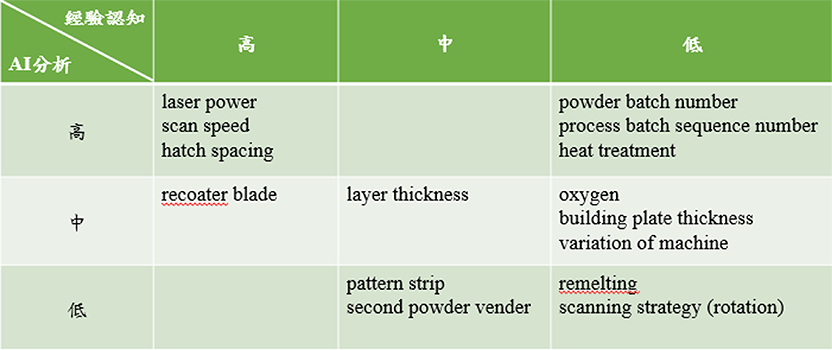
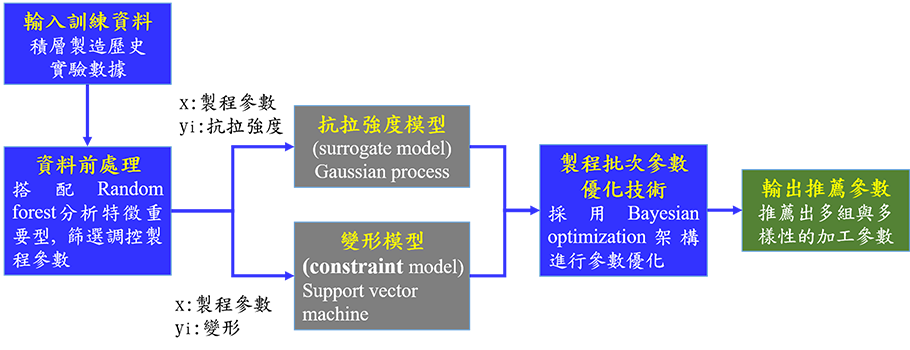
製程預前模擬技術
目前使用者利用雷射粉床熔融技術列印金屬零件時,所產生的熱應力變形,是製作時最主要的不確定性。若想以試誤方式減少零件變形,往往會耗費大量的人力、時間、材料與設備使用成本。製程預前模擬技術有助於研究和預測潛在的金屬列印過程中可能發生的物理現象和熱力學行為,例如:溫度分佈、傳熱、熔池動態、熔池幾何形狀、相變、熔化和凝固、Marangoni對流、微觀結構演變、殘餘應力和變形等[5]。
製程預前模擬技術提供了產品設計者擬採用雷射粉床熔融列印零件時,對於零件設計與列印加工間的關聯性有更好的理解與確認。對於初入金屬雷射粉床熔融列印領域的設計者,也不必參考或仰賴設備廠商所提供通則性的設計指引(design guide)。目前市面上已有可以支援金屬雷射粉床熔融製程預前模擬之套裝軟體,如ANSYS、Flow-3D、COMSOL等,然而購買與使用維護成本仍高。
有鑑於此,工研院南分院於開發金屬雷射粉床熔融設備的同時,近幾年更從現場使用者的需求回饋,戮力發展積層製造熱應力模擬軟體,如圖4所示,其最大功能為可預測零件在積層製造、熱處理及支撐架移除時,整體最大應力與變形。相關功能包含計算最終零件的變形,減少/避免變形、最小殘留應力、優化積層方向、底板和支撐結構的移除製程,目的可協助客戶第一時間決定正確的雷射粉床熔融製造方案[6]。
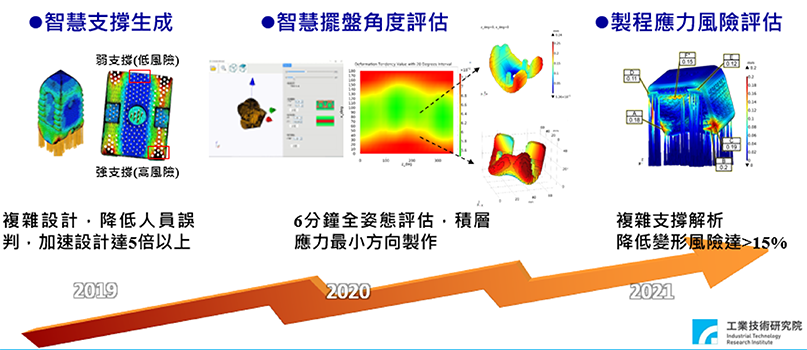
實際應用案例
人體骨盆(pelvis)由髂骨(ilium)、坐骨(ischium)及恥骨(pubis)三大部分組成,在臨床上因大範圍的髂骨骨腫瘤進行手術切除時,切除面積不足會導致腫瘤復發;切除面積過大又會對患者造成很大創傷,甚至會影響原本的功能及術後復原。因此,對於骨科醫生來說,如何填充髂骨腫瘤切除後的骨盆缺損是相當棘手的問題。在沒有積層製造技術以前,一般是植入由醫材廠商批量生產的模組式植體,植體跟骨盆缺損部位尺寸不易精準配合,積層製造技術應用於髂骨腫瘤的手術治療,對傳統骨腫瘤手術提供了新的概念與選擇,彌補了傳統手術方法中使用植體的許多不足,在提高手術品質的同時,能夠實現精準的個人化醫療[7]。
工研院南分院與三軍總醫院醫用3D列印中心針對髂骨骨腫瘤切除手術後的重建嘗試建立完整的作業流程與試做評估,首先由三軍總醫院將患者的骨盆電腦斷層掃描檔案建立成3D圖檔,並與院內醫生針對患者腫瘤切除範圍進行討論後,進行骨盆缺損部位個人化的植體3D CAD設計,如圖5所示。同時與醫師及工研院工程人員反覆就臨床手術、生物力學、熱變形模擬分析及積層製作實務等進行討論後定案,如圖6(a)所示。工研院南分院積層製造技術人員依過去累積之經驗直接進行圖檔前處理後,載入列印機臺製作結果支撐因熱應力產生斷裂,如圖6(b)所示。
因此,回過頭來由工程師進行熱應力預前模擬分析,分析結果顯示在原先支撐處有不小的熱應力集中現象,如圖7(a)所示,於是重新進行支撐生成並適當加粗優化分析其熱應力分布,有效降低支撐斷裂的風險,effective plastic strain從>100%降低至<40%,圖7(b)所示。重新列印後獲得成功之髂骨植體,如圖8(a)所示,與患者3D列印術前模擬骨盆模型可以精準的配合,如圖8(b)所示。
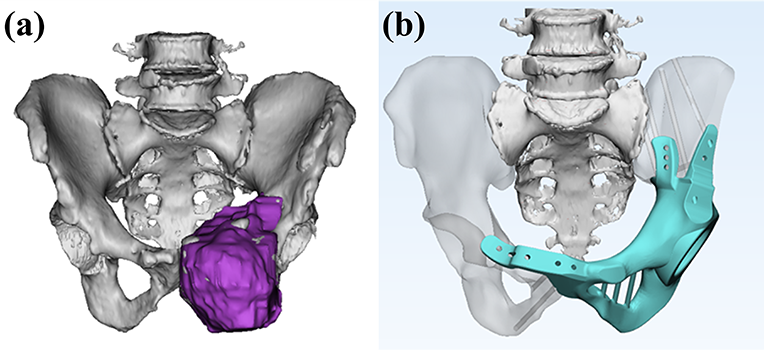
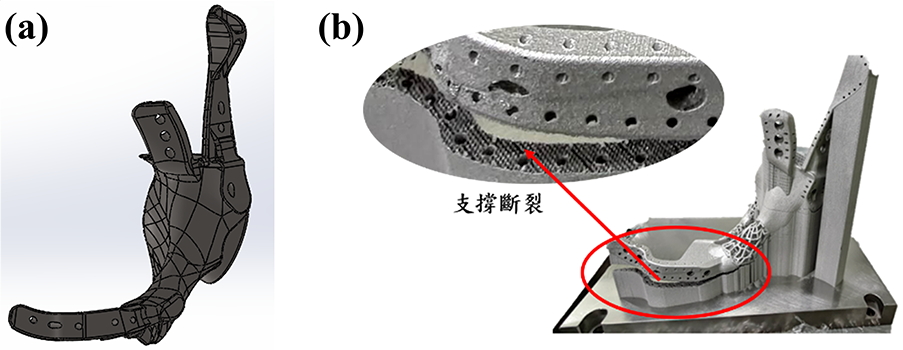
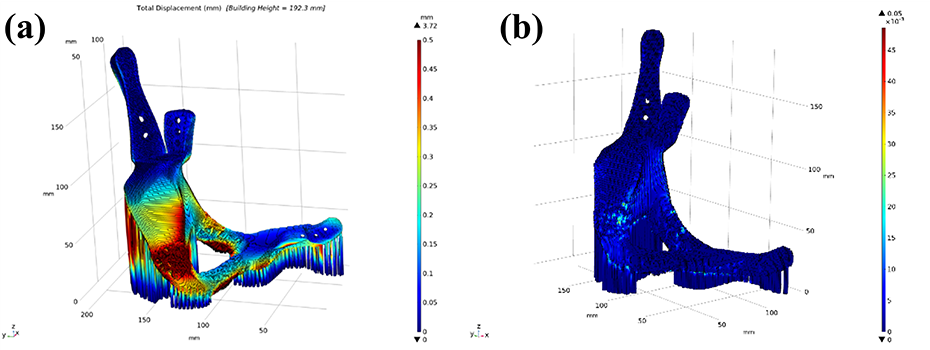
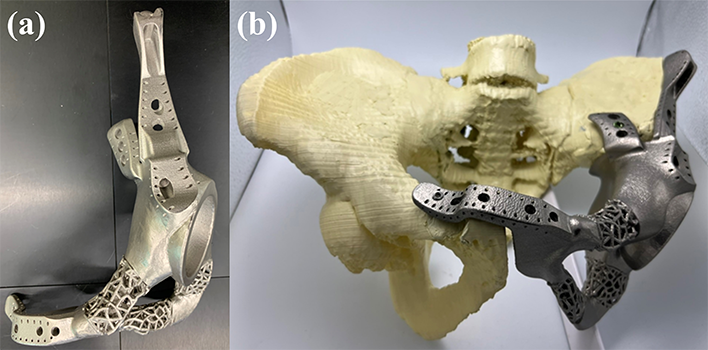
粉床監視補償控制技術
金屬粉床熔融設備列印過程中,由於粉體、氣場與雷射作用下,可能造成腔體透鏡之髒汙,雷射長期使用下可能衰減其出光能力,或腔內粉塵影響雷射光束行進路線,這些都可能造成雷射單位能量之改變,若在逐層製作無即時偵測與預警,內部瑕疵將殘留在內結構裡甚至製程會因此中斷,因此架構閉迴路積層製造系統將需整合熔池監控裝置,進而整合偵測熔池影像、形貌輪廓甚至熔池溫度等,達到工作中確認與逐層確認的完整機臺狀態監控之目的,達到預警及製程回授追蹤再確認。
目前此項技術對製程良率改善已達到≧80%的目標,導入偵測鋪粉完整度達>90%以上監控判斷成功率,若偵測有鋪粉不均勻、缺粉未覆蓋區、刮刀磨耗過大造成鋪粉不均勻痕跡,將自動判別後再進行重覆補粉鋪粉動作,於警戒上限到達前以不中斷製程為優先條件,使未覆蓋區域得到再鋪粉以及實現人員通知調整的機制,實現製程缺陷補償控制。設備狀態監控氧量濃度、循環流速、腔體壓差、底板溫度達全時100%條件追蹤,當因氧氣濃度變異回昇、循環流速因循環熔渣逐漸阻塞而變慢,都會即時調整循環頻率以提高效率,直至目標值達到正常區間,如圖9所示。透過以上兩點的缺陷影像與條件變異所進行的補償控制,目標於導入此系統後可讓產品良率提升>80%[6,8]。
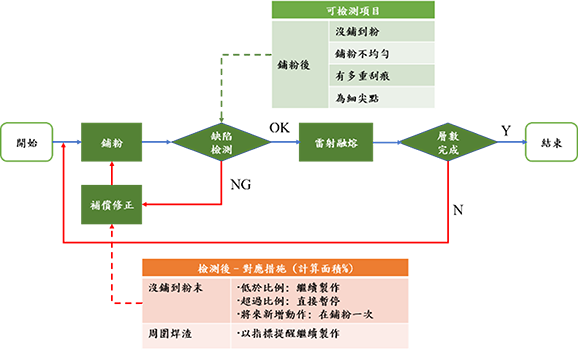
金屬粉體吸供篩設備技術
金屬粉床熔融設備列印過程前後需要花費長時間進行多項繁複之粉體處理,包含粉體清理、蒐集、過篩、運送等,特別是進行連續生產與當機臺愈大時,其所要處理的粉體重量越高,以工研院開發的AM 450設備,粉體依次填充粉體總重量約為100公斤(視金屬粉體總類而定),若依現行做法現場人員的整備工作份量重且耗時。
為此雷射中心開發出具備上述功能之安全整合吸篩供粉末處理系統。此吸篩供粉末處理系統具備自動化吸粉(回收)、篩粉、儲粉及供給粉體之功能,粉體處理能力達3 Kg/min,粉體儲存空間最大容積為400 * 400 * 300(L * W * H)。操作時同時具備氣氛保護(循環氧氣濃度< 1%),確保操作安全。搭配ITRI AM雷射積層製造設備,提供自動化粉末處理程序,減少粉末處理時間及人力,並提升製造後處理效率。
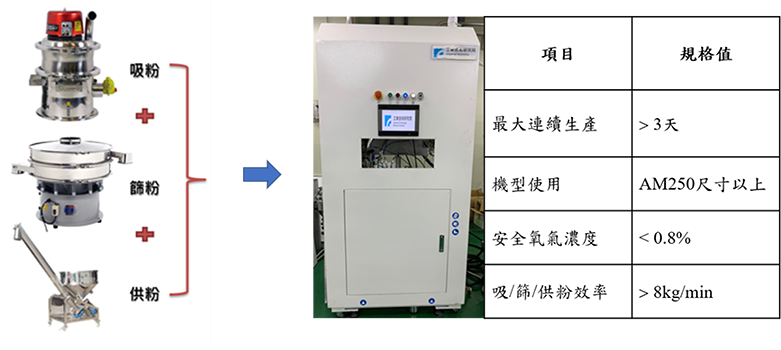
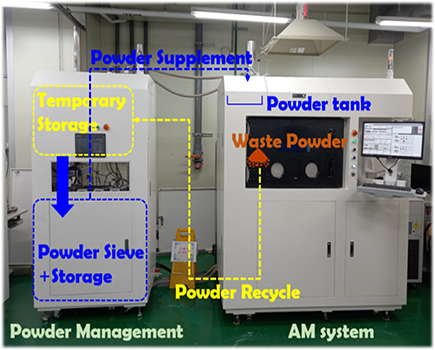
結語
受限於零件製作品質和生產效率低等障礙,目前大部分金屬粉床熔融技術所做的研究都集中在改進零件的製程參數及更大的列印腔體與多雷射頭,希望進一步提高金屬粉床熔融技術在產業實際製造中的可行性,然而,這項技術很多應用都面臨著不確定性和過程的不可預測性。這些歸因於市場上缺乏可用的過程控制與周邊輔助設備解決方案。
工研院南分院近幾年致力於建置積層製造技術之智能化系統。相關技術可於製作前提供較佳製程參數與可行性分析,縮短材料製程參數開發時間,減少製程熱殘留應力影響之失敗可能。此外,開發之監控補償系統即時監視粉床及雷射品質,針對製程缺陷或變化即時分析並提供補償控制參數與對策,並透過自動化整合吸供篩設備,支援連續生產製作,大幅提升金屬積層製造的效能。
本篇文章由工研院南分院 吳宗明 資深專案經理與三軍總醫院醫用3D列印中心 陳加恩 研究員、工研院南分院 林得耀 經理,以及工研院南分院 林敬智 副經理所共同編撰
參考文獻
- SmarTech Analysis Report: Metal Additive Manufacturing Market Back on Track to Produce More Than $50B in Components Annually by 2030. Available on line: https://www.prnewswire.com/news-releases (accessed on 10 Feb 2022)
- Nicolas Alberto Sbrugnera Sotomayor, Fabrizia Caiazzo and Vittorio Alfieri, “Enhancing Design for Additive ManufacturingWorkflow: Optimization, Design and Simulation Tools”, Applied Science 2021, 11(3), 6628
- Ana Vafadar, Ferdinando Guzzomi, Alexander Rassau and Kevin Hayward, “Advances in metal additive manufacturing: a review of common process, industrial application, and current challenges, Applied Science 2021, 11(3), 1213.
- Benjamin Durakovie, “Design for additive manufacturing: benefits, trends and challenges” Periodicals of Engineering and Natural Science 2018, 6(2), 179-191.
- Ninpetch, P. Kowitwarangkul, S. Mahathanabodee, et al., “A review of computer simulations of metal 3D printing”, AIP Conference Proceedings 2279, 050002 (2020)
- 蔡宗汶,鍾偉權,潘潘振銘,林敬智, “智慧化積層不NG製造技術”, 工具機與零組組件雜誌, 2021 (130), p60-67
- Jong Woong Park , Hyun Guy Kang, June Hyuk Kim, and Han-Soo Kim, “ The application of 3D-printing technology in pelvic bone tumor surgery” Journal of Orthopaedic Science 2021, 26(2), 276-283
- Y. Lu and C.H. Wong, “ Additive manufacturing process monitoring and control by non-destructive testing techniques: challenges and in-process monitoring” Virtual and Physical Prototyping 2018, https://doi.org/10.1080/17452759.2017.1351201