■補充與整理:耀德講堂 / 邱耀弘 博士
※紅字為Dr. Q補充之說明,大陸端原作者不可考。
技術補充說明
- 半固態在大陸被稱之為觸變(Thixo),意指材料金屬材料在接近熔點附近產生碰觸會變成液體,但不碰觸則為固體的特殊現象,此現象被翻譯為觸變(碰觸改變相態),如圖1所示。
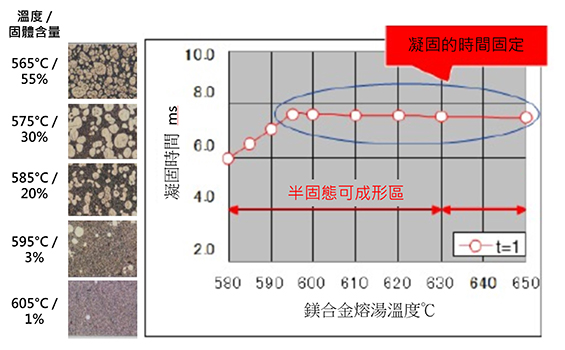
- 此技術主流是在日本,主要流行期間在2000~2010十年間,當時的筆記本電腦與翻蓋按鍵手機,但鎂合金的表面處理一直沒有辦法很理想地展現鎂金屬的光澤(輕但易氧化),逐漸地淡出市場。
- 鎂合金大約比重可以分布在3~1.7g(最輕的是鎂鋰合金),在未來的新能源電動車或許又會重新被提出討論。
摘要
本文對半固態射出成型鎂合金AZ91D的組織與性能進行了分析,如表1所表示為AZ91D的化學成分表與機械性能的要求標準。結果表明,該成型法所生產的鎂合金產品的組織及力學性能均優於壓鑄產品,從而為應用半固態射出成型法進行鎂合金汽車零部件的生產奠定基礎。
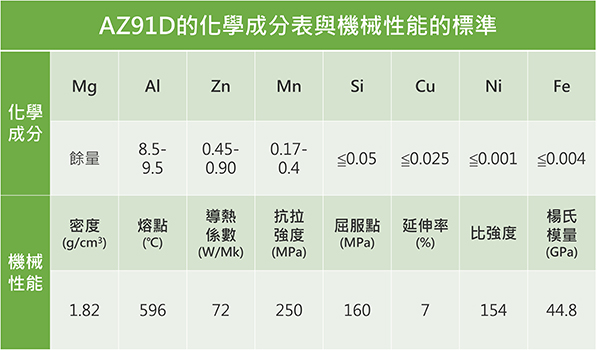
引言
近年來,隨著對綠色、環保等方面的要求逐漸提高,鎂合金以其重量輕、比強度高、比剛度高、減震性好、耐電磁遮罩、易回收等特點從眾多金屬材料中脫穎而出,廣泛的應用於航空、航太、電子和汽車等行業。目前,鎂合金應用的兩大熱點產業是電子業和汽車業。一方面,用於“3C”(Computer, Communication, Consumption Electronics Products) 產品的殼體,有逐漸取代可回收性較差的塑膠殼體之趨勢;另一方面,作為實際應用中最輕的結構金屬,鎂合金能夠滿足交通運輸業日益嚴格的節能和尾氣排放要求,從而生產出重量輕、耗油少、環保的新一代交通工具。
各國廣泛採用的鎂合金成型方法為壓鑄法。壓鑄鎂合金產品具有尺寸穩定性好、生產率高等優點,但也具有夾雜多、氣孔多、成型後難熱處理、尺寸近淨成型差等不足。採用壓鑄法製造的零件很難滿足諸如用於“3C”產品中所廣泛使用的薄壁殼體類零件以及用於汽車工業中的高性能鎂合金零部件的要求。
同壓鑄法相比,半固態方法製造的產品具有鑄造缺陷少、產品的力學性能、尺寸精度、表面和內在品質高等優點。此外,還有節約能源、安全性好、近淨成型性好等優點。目前世界上已經成功工業化的鎂合金半固態成型技術是半固態射出成型技術[1]。臺灣公司的漢達電腦(佛山)、富士鎂合金(昆山)、大陸的華禹鎂業有限公司(長春)是大陸境內最早引進此項技術的廠家,採用均勢以本文利用華禹鎂業的半固態射出成型機製備試樣,對半固態射出成型鎂合金的組織及力學性能進行了分析,從而為公司下一步進行汽車用高性能鎂合金的研究開發作適當的技術儲備。
- 不過半固態射出鎂合金仍舊有技術上必須注意的地方,由於耐高溫要求必須使用DC55(SKD11改性),模具熱損耗高且射出機為專用機,所有耐高溫緊固件都是比原來塑膠射出成型用(~350℃)的高出一倍以上之耐溫要求。另外由於射出後毛邊、螺絲孔、減肉厚處都必須倚賴CNC加工,還有鎂合金是雙相金屬,酸和鹼都能與其反應,射出的鎂合金坯如果不即時處理導致受潮,會容易有白點銹蝕。
另外有關材料的回收部份,由於鎂合金的活性高,半固態射出法必須使用切成片條狀(四方形斷面長條2X2X5~8mm),射出後流道(水口)料無法如壓鑄法直接熔融回收,鎂合金無法像鋁合金可以在無保護狀態下熔融,這是使用此門工藝必須要事先理解的。 - 此外,二次加工鋁合金和鎂合金的風險在於金屬塵暴、活性金屬廢棄品堆積造成起火的風險,在大陸昆山有多次的案例,鎂合金半固態射出與鋁合金壓鑄有相同的風險,一定要注意在射出、壓鑄、鑄件打磨與後處理過程必須格外謹慎。
半固態射出成型技術的原理及工藝過程
半固態射出成型技術的原理
在普通鑄造過程中,初晶以枝晶方式長大,當固相率達到0.2左右時,枝晶就形成連續網路骨架,失去宏觀流動性。半固態成型是在液態金屬從液相到固相冷卻過程中進行強烈攪拌,使普通鑄造成型時易於形成的樹枝晶網路骨架被打碎而保留分散的顆粒狀組織形態,懸浮於剩餘液相中。這種顆粒狀非枝晶的顯微組織,在固相率達0.5~0.6時仍具有一定的流變性,從而可利用常規的成型工藝如壓鑄、擠壓、模鍛等實現金屬的成型。
半固態射出成型法是近些年來開發的一種新工藝,源於美國DOW化學公司,美國THIXOMAT公司將其商業化。該工藝是將塑膠的射出成型原理與半固態金屬成型工藝相結合,集半固態金屬漿料的製備、輸送、成型等過程於一體,該法較好地解決了半固態金屬漿料的保存輸送、成型控制困難等問題。
半固態射出成型技術的工藝過程
射出成型法主要工藝過程如下:被製成顆粒的鎂合金原料(由枝狀晶鎂合金鑄錠製成,其組織仍為枝狀晶組織)從料斗中加入;在套筒中的鎂合金原料通過電加熱轉變成半固體狀態,在螺杆的剪切作用下,在套筒中半固體金屬漿料形成了近乎於球形狀的固體顆粒,在射出缸的作用下,以相當於塑膠射出機的十倍速率壓射到模具內成型。半固態(大陸稱之為觸變)射出成型機的基本結構如圖2所示。
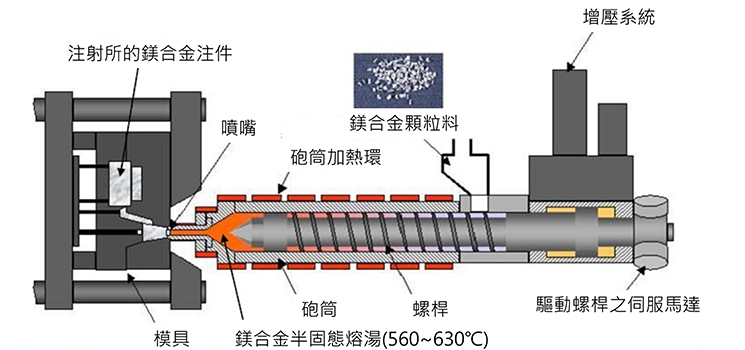
試驗設備及方法
半固態射出成型試樣的製備
本文採用日本製鋼所(Japan Steel Work, JSW)的半固態射出成型機製備了標準力學性能試樣,在不同製備條件下,考察了目前最廣泛使用的鎂合金AZ91D (9%Al+1%Zn的鎂合金)組織與性能的變化以及耐腐蝕性能。該成型機的外觀如圖3所示,試樣模具由日本製鋼所提供,所製備的測試試樣如圖4所示,成型過程中模具溫度為180℃。射出完畢時不需要噴冷卻劑來降低模具的表面溫度,與傳統的壓鑄機不同,因此設備周圍非常潔淨。
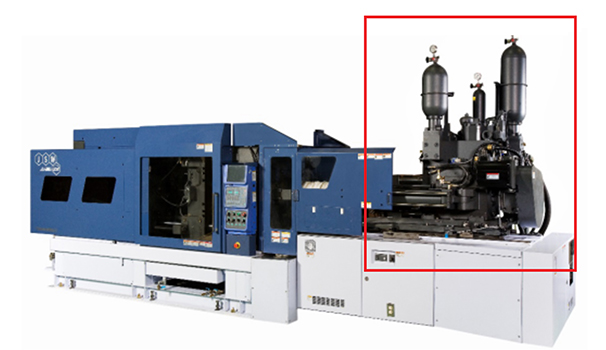
- 由於溫度很高的鎂合金射出料沒有辦法設計熱流道,因此JSW開發長噴嘴(Long Nozzle)技術,加長的射出噴嘴深入模穴附近,因此模具的強度受到考驗。
圖4中由左至右依次為標準衝擊試樣、標準蠕變試樣、標準拉伸試樣與硬度試樣,在論文只採用標準拉伸試樣進行試驗,分別考察不同工藝條件下,半固態鎂合金組織與性能的變化。

快速腐蝕條件如下:腐蝕介質為0.5% NaCl或0.1mol NaCl溶液;試驗溫度:室溫(靜態)或35±1℃;腐蝕測試時間:120小時(因為鎂合金活性高,要求測試的時間很長)。
- AZ91D屬於鑄造鎂合金類,主要依靠壓力模具鑄造輔以後加工的方式加工,可以用電泳等表面方式改變外觀。特點是比強度高且耐腐蝕較純鎂大幅提高,主要用於電器產品的殼體、小尺寸薄型或異型支架等。A代表金屬鋁Al,Z代表金屬鋅Zn,9代表鋁的含量為9%,1代表鋅的含量為1%,最後的D為辨識代碼。
結果與討論
半固態射出成型鎂合金的組織分析
圖5中組織是取自不同工藝參數製備標準拉伸試棒的中部,其工藝參數的區別主要表現在料筒溫度的差別,在圖5中由工藝(a)至工藝(d)料筒溫度逐步升高。
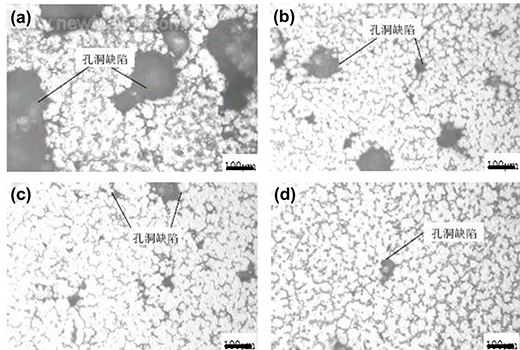
由圖5可見,在不同工藝參數條件下,半固態鎂合金組織的變化不大,主要差別表現在缺陷的數量和大小方面(金屬熔融狀態的蒸發造成氣孔缺陷,尤其在高速高壓射出下的氣旋通常會捲入肉厚變化較大的區域)。可見,料筒溫度對半固態鎂合金成型性具有決定性的影響,在料筒溫度較低的條件下,半固態漿料的流變性不足,成型性能不足,提高料筒溫度可以明顯的提高半固態漿料的流變性能,但會明顯降低固相率,在工藝d的條件下,除晶粒細小外,其組織已經接近普通壓鑄合金組織。因此,在實際產品製備中必須控制好料筒溫度和組織這兩方面的因素,才有可能獲得高品質的產品。
圖6為半固態鎂合金組織的掃描電鏡照片。由圖6a可見,半固態鎂合金試棒的組織細小、均勻,圖6b為放大的晶界相,對晶界相的定點能譜分析表明,其晶界相的主要組成為Mg和Al,並含有少量的Zn。
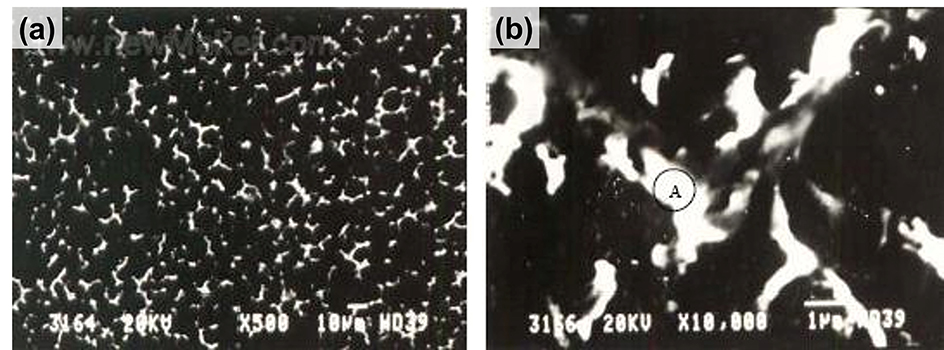
根據圖6表示地定點能譜分析結果如圖7所示。對半固態鎂合金進行線掃描的結果表明Al和Zn主要分佈在晶界上,在晶內分佈較少,Mg則主要分佈在晶內,在晶界處Mg含量明顯減少,如圖8所示。以上結果表明半固態射出成型鎂合金的組織形態及分佈基本與壓鑄組織相同。
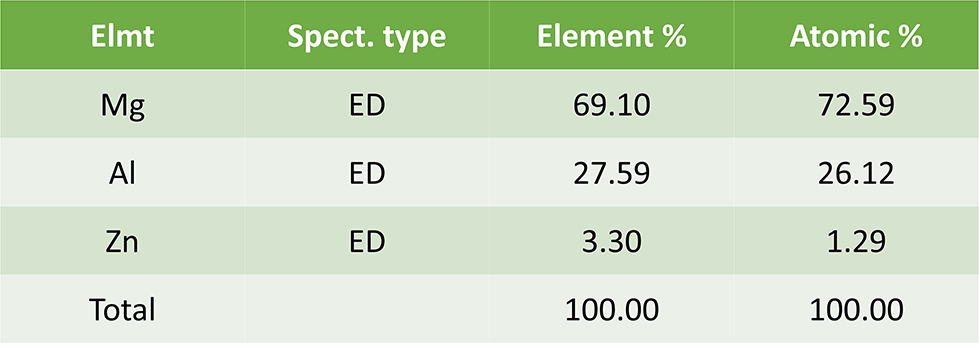
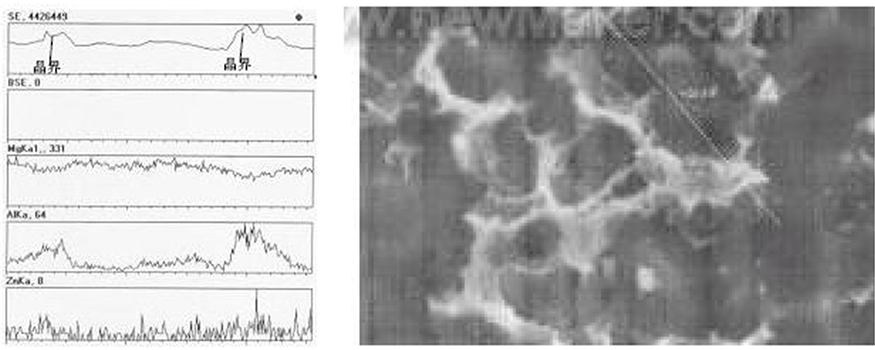
半固態射出成型AZ91D的力學性能分析
- 半固態射出成型AZ91D的力學性能
圖9中示出了50根試棒(圖4工藝d條件下)中隨機抽取5根試棒的力-位移曲線、力-變形曲線以及力學性能的測量資料。由此可見,半固態射出成型試棒已達到了很高的強度,其平均斷裂強度可達到270MPa以上,平均屈服強度可達150MPa左右,由於鎂合金試棒在拉伸過程中沒有明顯的屈服點,故而以σp0.2(0.2的應力變形)估算其屈服強度。 - 鹽水快速腐蝕對於半固態射出成型AZ91D性能的影響
鎂合金的抗腐蝕性能是衡量鎂合金性能的一個重要指標,本文採用快速腐蝕試驗考察了經快速腐蝕後半固態成型鎂合金試棒組織與性能的變化。所採用試棒與前述力學性能試棒相同。圖10展示出了經120小時快速腐蝕後AZ91D鎂合金試棒的力學性能。可見,腐蝕後鎂合金試棒力學性能明顯下降,平均斷裂強度下降到220MP左右,屈服強度下降至120MPa左右。腐蝕試驗結果表明,儘管半固態組織細小、緻密,但其抗腐蝕性能仍相當差,做為重要結構部件和裝飾性殼體類零部件時,仍須採用適當的表面處理工藝,否則將無法滿足使用要求。
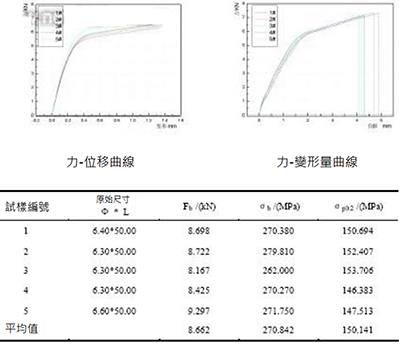
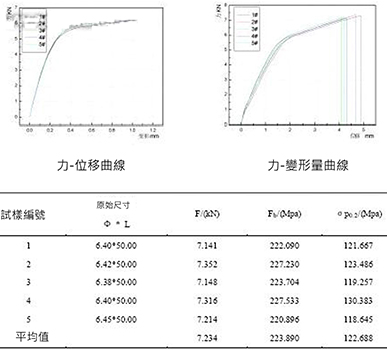
結論
近年來,世界各國高度重視鎂合金的研究與開發,將鎂資源作為21世紀的重要戰略物資,加強了鎂合金在汽車、電腦、通訊及航空航太領域的應用開發研究。美、日、歐等發達國家目前已經投入大量人力和物力,實施多項大型聯合研究發展計畫,研究汽車用鎂合金零部件,這些研究開發計畫加快了國外應用鎂合金零部件的步伐。中國是一個摩托車生產、消費大國和出口大國,也是一個潛在的汽車生產和消費大國。然而,目前中國的鎂合金成型技術還相對落後,鎂合金零部件的力學性能及耐腐蝕性能較低是制約汽車用鎂合金零部件在中國應用的一個重要因素。
本文通過對半固態射出成型AZ91D鎂合金試棒的顯微組織、力學性能分析和快速腐蝕試驗,得出如下結論:
- 應用半固態射出成型技術可得到組織細小、緻密,力學性能相對較高的鎂合金部件。
- 其綜合力學性能優於目前被廣泛採用的壓鑄鎂合金部件。
- 半固態射出成型設備的費用高昂,以及必須支付專利許可的費用,加之成型用原材料-鎂粒的成本較高,整體投資比較大。因而該技術尤其適用於那些具有較高要求和高附加值的產品。
- AZ91D是否能夠使用NMT技術(Nano Molding Technology, 奈米成型技術)與一種材料的工程塑膠進行結合?沒有資料顯示可行性,目前仍有待三井化學的資料(當時極度保密)。不過已經得知普通鎂合金AZ31是可以採用NMT技術的。