■通業技研
前言
伴隨3D列印設備、材料與技術的演進,3D列印應用從原型設計、功能測試邁向終端生產製造。而眾所皆知3D列印最令人印象深刻的特點之一,就是可以靈活創造出具複雜內部晶格結構的零件,這在傳統製程是不可能做到的。甚至近年製造商為了材料減重或者節省3D列印用料成本等因素,也開始運用輕量化設計,例如工業零件減重(航空航太、汽車等)、醫療植入體及消費產品(矯正鞋墊、工藝品)等。
利用Lattice點陣模組(晶格結構)達輕量化設計
Materialise 3-matic軟體中的晶格結構模組提供3D列印強大的設計工具,減輕重量、吸收衝擊、滲透性、熱交換和熱力學應用的理想選擇,讓您可以在產品內部實體或外部輪廓設計多種不同的陣列結構、隨形結構或隨機結構,或者自由地在零件上創建自己想要的結構,導入STL或者賦予需要的網格參數,進而達到增強緩衝、增加孔隙率,或減輕產品重量等目的。(晶格是3D單元格的重複,由特定幾何形狀的樑和節點組成,以創建結構。)
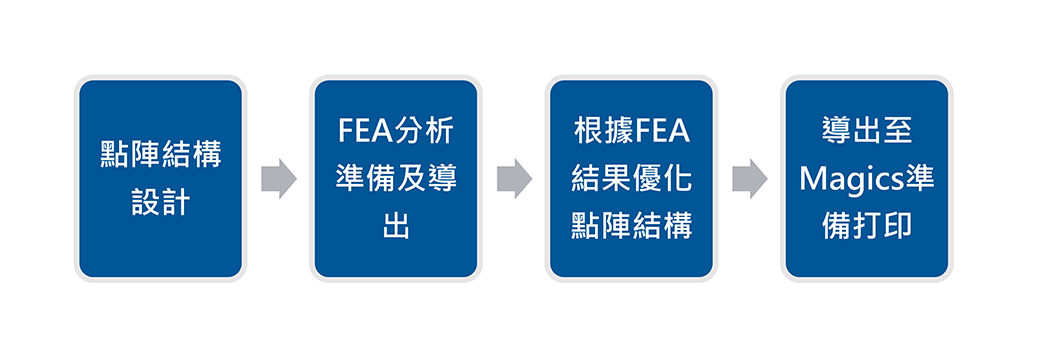
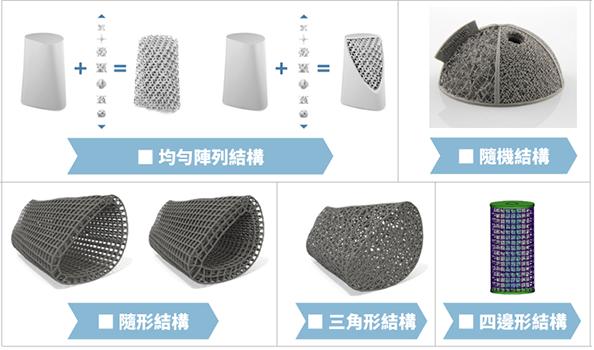
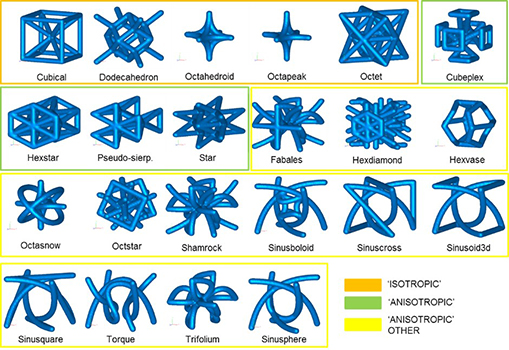
Lattice點陣模組3大應用
傳熱系統應用
借助晶格設計於3D列印之應用,用戶能夠快速創建具有高度複雜和小型化設計的高效電子結構,例如熱交換器、冷卻系統、催化轉換器或者航空設計中使用的絕緣層中添加晶格結構,使熱空氣從發動機引導到機翼以進行除冰,甚至鋰離子電池也能使用晶格進行熱管理。
吸收衝擊應用
晶格設計非常適合用於衝擊吸收應用,例如用於頭盔護墊以提供卓越的保護性能,還能帶來透氣性和出色的貼合度;或者應用於製作3D列印跑鞋鞋底,有助於緩衝跑步者的衝擊力;或者應用於汽車和航空領域所需要的機翼夾層金屬晶格結構,以提供更好的衝擊保護,同時還能兼具輕量化並改善成本高昂的問題。
流體滲透應用
利用多孔結構設計應用於再生醫學領域,打造骨組織支架晶格結構,促進組織生長的同時,也能提供結構性支撐。
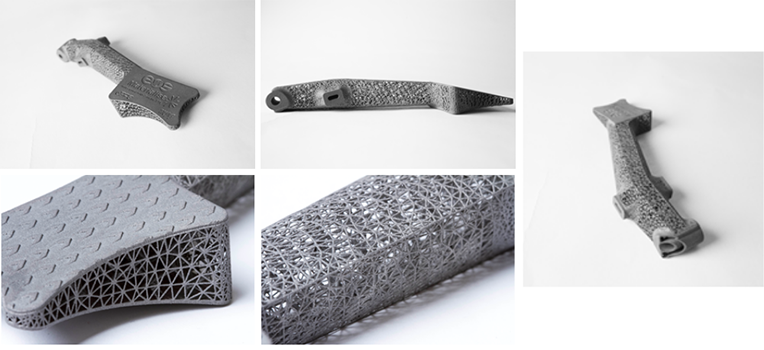
透過3-matic軟體生成晶格結構的3D列印設計案例
案例1:輕量化汽車座椅材料用量減少72%,依然非常結實(日本豐田研發實驗中心)
豐田汽車公司和豐田研發實驗中心與Materialise一起設計並列印了一個輕量化座椅,以最少的材料,達到最優化的設計。這個資料量極大的(250 GB)設計檔在操作、傳輸和加工方面都非常複雜,只能透過Materialise切層技術來實現。讓豐田的這個輕量化汽車座椅材料用量減少72%,座椅重量從25kg降到7kg。
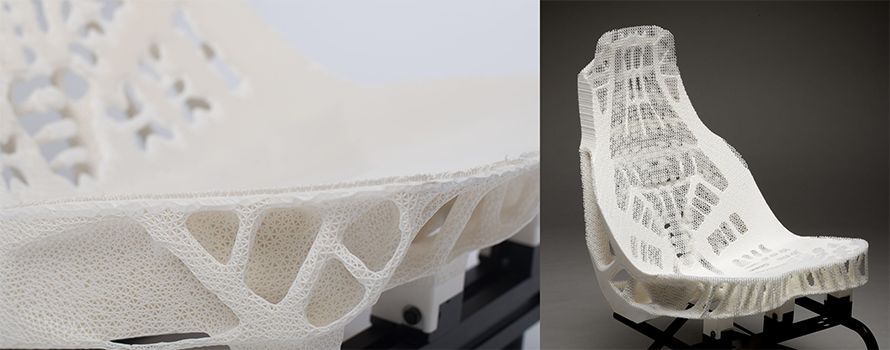
案例2:輕量化結構使鈦合金航空器鑲嵌件減重66%
對於航空航太零件來說,任何重量的優化都是非常重要。而如何減少重量並保持零件本身結構強度,這變得非常重要。該鑲嵌件是用於連接衛星上的零件,需要很大的承重。傳統的設計中是透過使用鋁合金或鈦合金做成整塊實心磚型,經由使用3D拓樸優化和輕量化3D設計使零件重量從1454克減少至500克,同時還可以解決原有設計中的熱塑性應力問題,進而有效減少應力對零件的損耗,以及提高負載平衡。
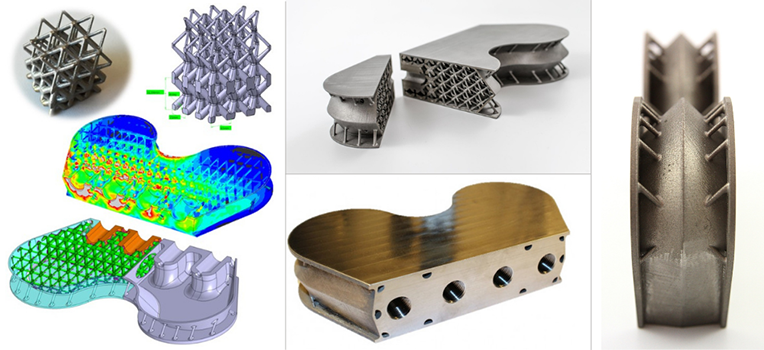
案例3:韓國KLIO Design運用Materialise 3-matic軟體晶格結構,減輕汽車重量的同時,確保小體積的穩定性
韓國設計公司KLIO Design推出一款名為「Open structure Mobility Concept」的小型電動概念車,2016年於首爾智能移動國際會議暨展覽會上展示,其中其輪圈蓋、車輪防護裝置、方向盤、部分車架以及晶格結構座椅設計都是採用3D列印而成,實現輕量化又能確保小體積穩定性。在設計過程中均採用Materialise 3-matic建模軟體以及Magics軟體協作完畢。
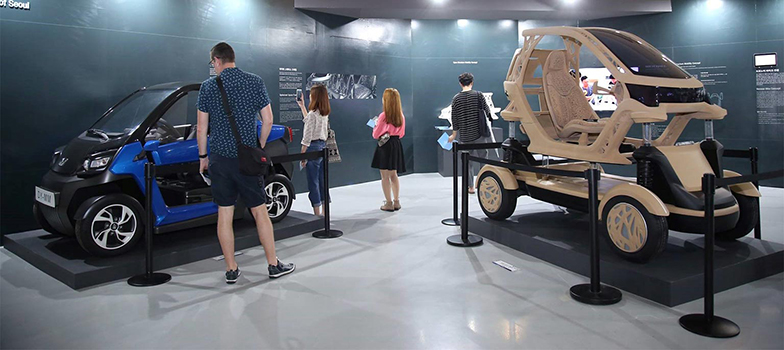
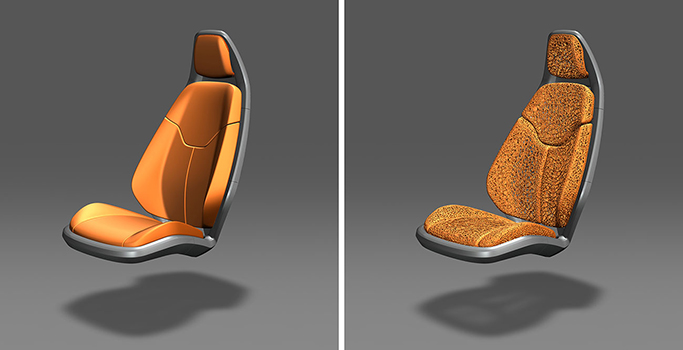