■慶良電子 CAE課 / 曾琛涵 & 李宜蓁
前言
一個完整的連接器是由許多零件組合而成,金屬件利用沖壓、車削、壓鑄等方式製作,而塑膠件大多以射出成型製成。其中,塑膠零件有支撐連接器結構的功能,故在產品開發前期,準確預估塑膠件的結構強度,有助於後續試模生產。
塑膠強度與塑膠分子鏈的排列行為有關,縫合線區域的機械強度會有明顯減弱的情形(圖1),特別是含玻纖的塑膠材料此弱化效應會更加明顯[1, 2]。此外,射出成型工藝導致的玻纖配向也會大幅影響塑件的力學性能(圖2)[3],近年來也有越來越多人投入玻纖增強複合材料應用的相關研究[4, 5]。綜上所述,本研究使用聯合仿真技術,重現塑膠產品於扭力測試的開裂現象,進行連接器前蓋結構強度的優化設計。
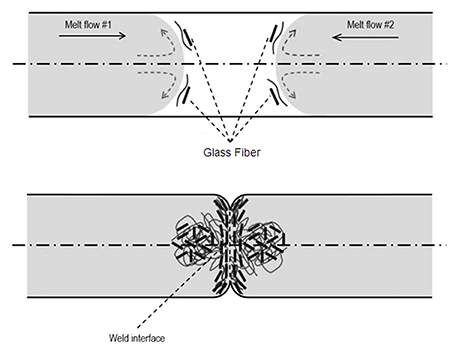
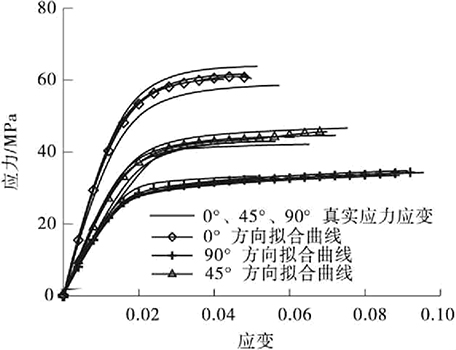
產品描述
連接器的基本結構包括端子、鐵殼及膠芯,根據不同的應用可能還會有其他零件;如本研究所探討的連接器,其膠芯外部有一個前蓋結構,可以在互配時提供準確定位與對接穩定性。連接器成品組裝完成後,為了使前蓋與膠芯本體之間不產生相對運動,並加強整個連接器在電路板上的固持性,設計上採用公制M2螺絲對前蓋進行鎖附(圖3)。該案例於螺絲鎖附後,前蓋的遠膠外側發生開裂問題,開裂位置與模流流動末端的縫合線相符(圖4),即塑膠強度較脆弱處,此為明顯品質異常,需要對產品設計加以優化才行。
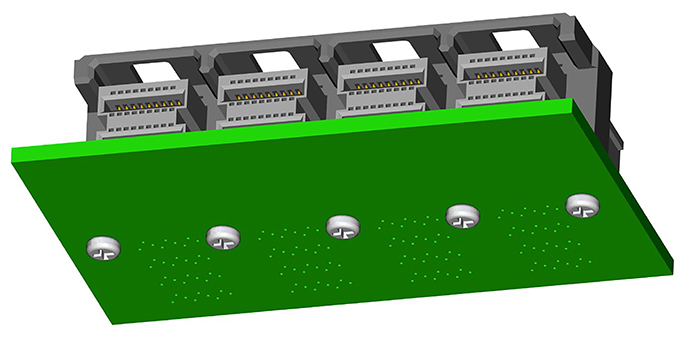
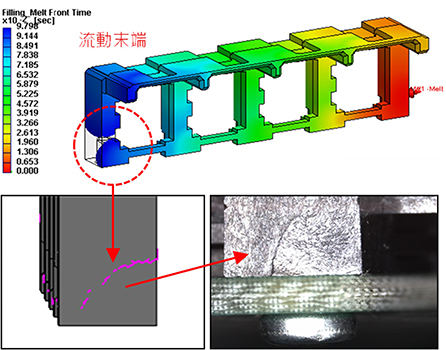
模擬方法及流程
前蓋模型材料為LCP E130i,先使用Moldex3D進行模流分析,透過Moldex3D FEA介面模組將模流分析後的材料性質輸出,如由纖維配向產生的非等向性數據及縫合線強度,再將這些數據對應至簡化後的前蓋網格模型,作為ABAQUS結構分析的前蓋材料參數。螺絲使用材料為SUS301,仿照螺絲鎖附行為(圖5),對該螺絲施加一旋轉負載後,將LE結果作為前蓋是否開裂的評估依據,同時擷取螺絲鎖附過程中產生的扭力值,以便與實測數值進行對照。
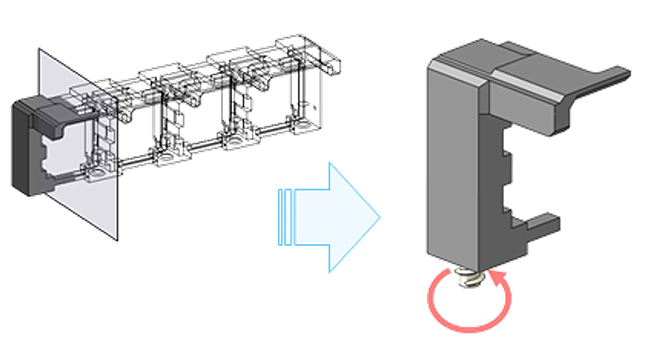
結果與討論
原始設計下,對螺絲施加旋轉負載後,不同分析模式的結果存有顯著差異(圖6A)。「聯合仿真」的LE結果呈現集中且連續的分布,其位置與前蓋實際開裂位置相符;單執行結構分析時,其LE分布則無法反映此現象。此外,兩種分析模式求得的扭力值也相差甚大(表1及圖7),「聯合仿真」求得的扭力最大值為2.23 kgf‧cm,落於實測扭力範圍內,但若僅執行結構分析,扭力分析數值則有高估的疑慮,可能因此錯判產品的結構強度;為此,「聯合仿真」的存在確有其必要性。
為了改善前蓋遠膠外側的開裂問題,採取新增溢料井的方式使流動末端的縫合線產生位移(圖8),以提升原開裂位置的結構強度。設計變更在施加旋轉負載後,其LE結果無連續分布,而實際產品外觀亦無開裂問題產生(圖6B)。在扭力數值方面,設計變更可承受之扭力明顯提升(表1及圖7),顯示原開裂位置的結構強度的確有增強的趨勢。
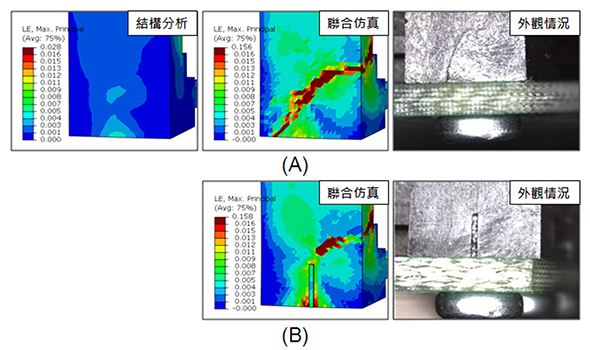
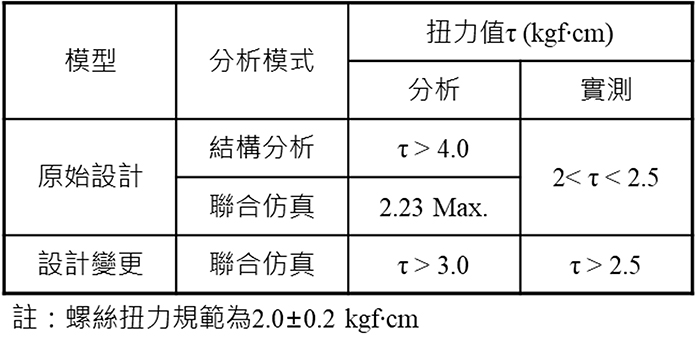


結論
本研究應用Moldex3D FEA介面模組,將模流分析結果轉譯到結構分析軟體ABAQUS,進一步為產品開發執行全面性的結構分析。此分析以LE結果作為塑膠開裂的判斷指標,在扭力分析數值上也具有一定的參考性,可協助評估產品的結構強度。因此,本案例的分析經驗及操作流程應有其參考價值,有助於提升CAE在產品開發流程中的應用深度及廣度,讓CAE的效率最大化。
參考文獻
[1] On the Weld Line of Injection Molding Part https://www.linkedin.com/pulse/weld-line-injection-molding-part-hank-tsai
[2] 如何避免縫合線 https://wenku.baidu.com/view/7619ff1efad6195f312ba6f7
[3] 短玻纖增強複合材料的性能及其在車身上的應用 https://auto.vogel.com.cn/c/2021-09-08/1132115.shtml
[4] 多尺度聯合仿真在汽車注塑零件減量化設計中的應用研究 https://read01.com/zh-tw/m0Moyzy.html#.Ys4oIb1Bzcs
[5] 李西順, 楊明華, 孫正峰.車用塑料件的模流與結構聯合仿真分析, 2017. https://www.fx361.cc/page/2017/1121/2477225.shtml