■淡江大學 化學工程與材料工程學系 / 黃招財 教授
摘要
近年來為了減少化石燃料汽車排放問題,採用纖維強化塑膠(Fiber reinforced thermoplastics, FRP)製備汽車零組件,藉由汽車輕量化後提升燃油效能,改善排放問題。然而,纖維強化塑膠在經歷複雜的射出成型製程中,纖維到底如何產生強化機制,此等機制如何由內而外,或者由外而內可以被適當地量化,甚至調控,目前並未完善。再者,此等強化機制又會如何影響射出成品的幾何變化,至今仍不完全掌握。
為此,本文利用一個具有三種不同進澆型態的複合幾何模型,運用虛擬之無損檢測技術模擬分析來研究不同流場區域(從靠近澆口到充填結束區域)纖維排向如何變化,接著透過實際之射出成型製程,加上微電腦斷層掃描與影像處理(實際無損檢測技術)進行射出成品內在之纖維排向實務解析與驗證。之後,再深入觀察射出成品在不同流場區域所展示之幾何變形結果,進一步建立纖維排向變化與射出成品幾何收縮變形之關聯性。結果顯示,透過數值模擬分析與微電腦斷層兩種無損檢測技術所獲得之纖維排向特性相當吻合,特別是在充填結束區域(end of filling region, FR)時,原先在平行流動方向之纖維排向張量(A11)會迅速減小,同時在垂直流動方向(A22)及厚度方向之纖維排向張量(A33)會增強;此等之纖維排向張量變化驅使A11與A22產生交錯現象,進而導致垂直流動方向主導,明顯改變纖維排向特性。此等微結構特性變化,可經微電腦斷層掃描與影像處理技術獲得證實。
另外,透過射出成品之幾何收縮變化探討發現,在靠近澆口區域(near gate region, GR),成品之幾何外觀收縮呈現左右對稱收縮,而且在流動方向收縮變化最小,甚至膨脹,此部份主要因為平行流動方向纖維排向張量A11主導該區域所致。然而,在充填結束區域(FR)時,流動方向抵抗收縮貢獻度明顯減小,在此同時垂直流動方向與厚度方向之抵抗收縮貢獻度相對增強,導致成品呈現收縮左右不對稱之外觀,此現象主要是由內在之纖維排向張量由平行流動方向轉至垂直流動方向及厚度方向所致,此等結果能透過無損檢測技術明確證明纖維排向變化與射出成品幾何收縮變化有相當一致之關聯性。
前言
由於地球暖化問題越來越嚴重,溫室氣體的排放被認定是造成地球暖化問題最主要的原因之一,其中根據美國環保署近年來的調查發現,最主要的溫室氣體排放來源之一為燃燒化石燃料之交通運輸工具所造成[1],為減緩此等問題,過去幾年許多國家都努力投入汽車輕量化技術,思考讓汽車總重量減輕,提升車駕效能並減少排放,此等做法也同樣有利於現代及外來電動車的運行。
再者,想要達成汽車輕量化技術主要是利用塑膠複合材料來製作部份之汽車零組件,透過以塑代鋼讓整體重量減輕。此等塑膠複合材料的常見相關技術,包括:
- 將非連續式纖維與熱塑型塑料,利用射出製程製作成品;
- 將非連續式纖維與塑料,利用擠壓製程製作成品;
- 將連續式纖維先編織排列,再利用熱固型塑料灌製固化製作成品[2-4]。
不論哪一種製程,理念上都希望纖維在熔膠內能夠均勻分散,進而提供複合材料構成之產品有一定強度與韌性[5-6]。然而,纖維在此等成品中到底如何扮演好增強材料特性之角色,常常受制於纖維在熔膠中如何排列,但此等排列非常不容易觀察與確認。
一般而言,經歷三十年的努力,目前要了解纖維在熔膠中的排列方式,一方面可透過理論分析虛擬實境方式來進行推估與預測,此等學理較有系統Folgar and Tucker[7]提出了短纖維排向預測理論,之後Advani等人[8-9]持續強化理論模型用來推測短纖維之排向與其效應。透過此等理論模型的幫助,讓近代產學界對於纖維強化塑膠射出成品的設計開發有了良好之指引[10-11]。
然而,如同Thomason[5]建議,足夠長度之纖維是確保衝擊強度需求之基本要求,因此在實務上如何將長纖維導入高分子材料內,並且在經歷高溫高壓的射出製程後仍能保有一定長度,以及長纖維微結構如何影響,不論從學理預測或是實驗觀察,都非常挑戰。為了進一步探究長纖維強化塑膠之微結構性質,有許多學者陸續提出Anisotropic Rotary Diffusion(ARD) model[12],Reduced Strain Closure(RSC) model[13-14]。但是此等數值理論模型需要許多額外參數,使用上非常複雜。為此,Tseng等人[15]進一步提出iARD-RPR數值理論模型,簡化模型參數,並導入於商用軟體Moldex3D軟體中,也成功展示於長纖維射出成型產業應用中[16]。
另一方面,纖維在熔膠中的排列方式也可透過實際之實驗觀察,包括:可透過破壞性之光學法,利用將樣品切割/拋光/SEM或TEM顯微鏡方式進行檢測[17-18];或是透過電腦斷層掃描(CT scan)/影像處理之無損檢測技術來達成[19-20]。其中採用光學法需利用減法方式將樣品逐一拋除,再利用光學顯微鏡進行樣品表面特性表徵,再擷取影像進行處理判斷,此法影響準確度之參數很多。另外,利用電腦斷層掃描(CT scan)及影像處理之無損檢測技術著要是讓樣品透過三維之電腦斷層掃描廣泛地蒐集內在的微結構特徵,再利用影像處理技術進行微結構特徵之評估與分析,此方法是否足夠精確與斷層掃描的條件給定,以及後續影像處理技術優異與否很有關係。然而,不論利用理論分析或是實驗觀察所得之纖維排向,除了要面臨如何評估其準確性與否外,此等排向到底如何與加工製程引發之產品幾何變化有一定關聯性,至今並沒有完整的解決方案。特別是複合材料內在纖維排向變化如何進一步影響射出成品之幾何收縮變形之關聯性,也就是如何具體體驗纖維排向變化,就作者所知,目前仍非常稀少[21-22]。
為此,本篇文章將先詳細說明如何透過無損檢測技術(包括:虛擬實境之CAE模擬分析技術,以及透過電腦斷層掃描(CT scan)/影像處理之實務技術)掌握非常複雜且不易觀察檢測到之纖維排向微結構特性變化。接著,再從射出成品之幾何尺寸之量測與分析,掌握成品巨觀變形的趨勢與量值。之後,進一步整合纖維排向微結構特性變化與巨觀變形的關係。透過此等作動展現無損檢測技術如何協助產業朋友能夠看透複雜之纖維排向微結構特性,與其具體之影響。
理論背景
此研究中,纖維強化熱塑性塑膠材料(Fiber reinforced thermoplastic, FRP)假設為不可壓縮之牛頓流體。此等塑料在射出成型製程中所產生之三維流動系統,將以下列之主控方程式(Governing Equation)及纖維微結構之數學模型進行表示。
高分子熔膠流場模型
其中u是速度向量;T是溫度;σ全應力張量(total stress tensor);τ應力張量(extra stress tensor);g重力加速度;t為時間;P是壓力;ρ是密度;k為熱傳導係數;Cp為比熱;D應變速率張量。
另外,針對高分子熔膠在不考慮流動與纖維耦合作用下,其應力張量可表示如下:
其中η為高分子熔膠之剪切黏度。
再者,高分子熔膠之剪切黏度將隨溫度變化情況,可表示如下:
以及
其中n為power law指數;h0是指零剪切黏度(zero shear viscosity);t*是指零剪切至power law剪切之過渡區域應力張量。
纖維排向模型
在FRP熔膠中,每一根纖維可被視為具有剛性的軸對稱硬棒,而其單位向量為p,沿軸向可描述纖維排向,
其中,ψ(p)為定向空間上的概率密度分布函數。A4為四階方向向量,其定義為:
此張量恰巧為一對稱張量,為了處理這個複雜的張量系統,Tseng等人[15]提出了一種新的纖維排向模型,結合Jeffery的流體力學(HD)模型,即為iARD-RPR模型:
詳細RPR模型及iARD模型可見於[4]
其中,W是渦度張量,D為應變速率張量,ξ是單一纖維的形狀因子。
射出成型系統之模型與資訊
模擬分析之模型與資訊
圖1a為本研究之產品幾何模型,此產品外觀尺寸為400 mm × 165 mm × 3 mm,內含有三個不同進澆方式的ASTM D638標準拉伸試片(試片尺寸為172 mm × 20 mm × 3 mm),分別是(I)側邊入料之模型,(II)直接入料之模型,以及(III)雙邊入料之模型。圖1b則為模座及冷卻水路。為了探索流纖維排向微結構變化,特別是將每一個標準拉伸試片再分成三個區域,分別是為靠近澆口區域(Gate Region, GR),中間區域(Center Region, CR)以及流動末端區域(end of Filling Region, FR),並在每個區域再安置多個量測節點,以確定能詳細搜集各項可能影響產品之因子,如圖2所示。再者,射出成型製程主要之操作參數為充填時間為1.49秒,保壓時間為5秒,冷卻時間為15秒,其他相關參數如表1所示。至於所使用之材料,主要為含3mm之短纖維複合之聚丙烯材料(由李長榮化工公司供應)。
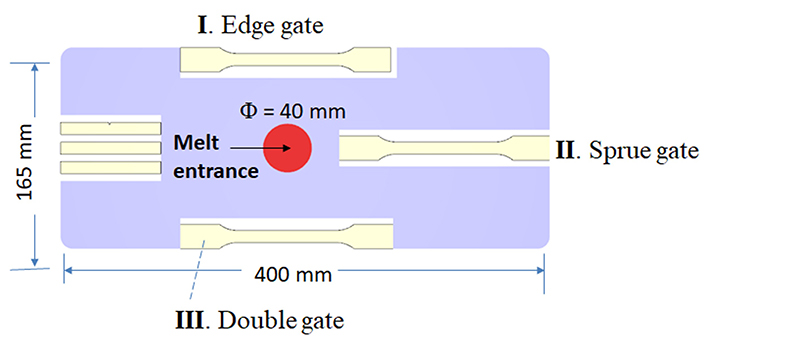
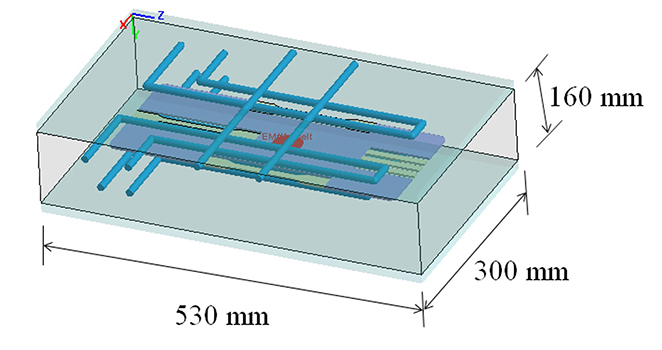
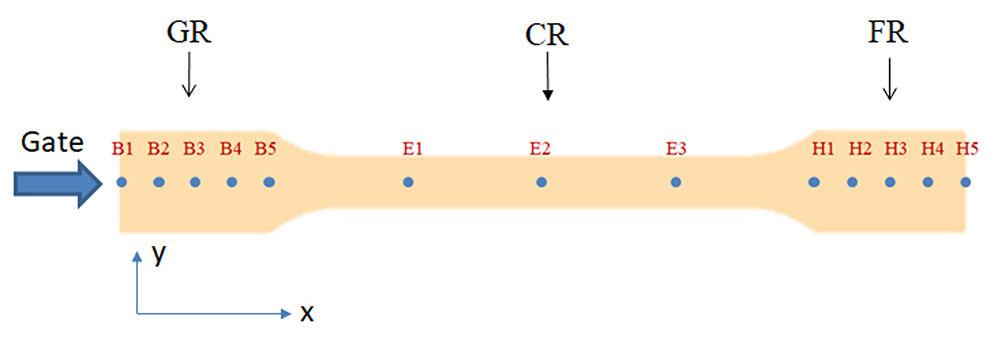
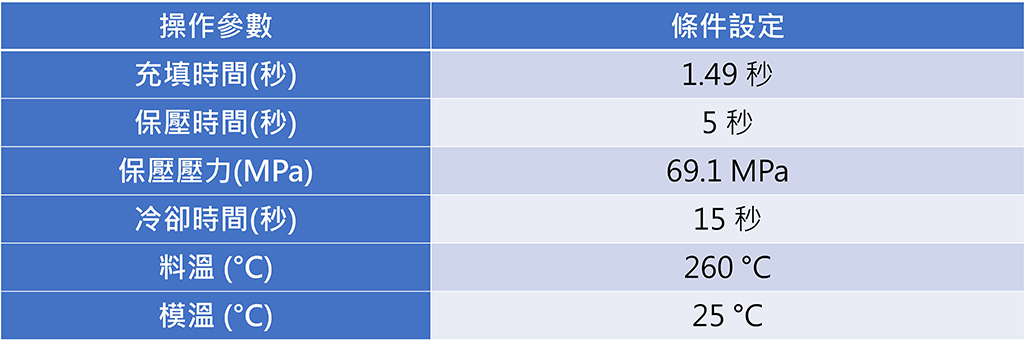
實驗設備與資訊
圖3a為實際所使用的射出機台型號CLF-180TXL,此機台為全立發機械廠股份有限公司所開發之特殊長纖機台。圖3b為模座及冷卻水路佈局。再者,射出成型主要之操作條件與材料,皆與數值模擬系統相同。另外,後續為瞭解纖維排向如何變化與影響,將利用微電腦斷層掃描(micro-CT)技術進行掃描,此部分主要由工研院材化所Multiscale X-ray CT實驗室,利用Bruker Skyscan 2211系統所提供之技術。
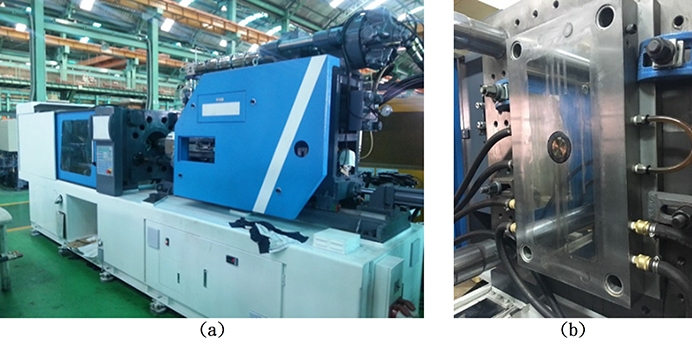
再者,對於虛擬損檢測技術纖維排向的模擬分析方法,主要是透過Moldex3D軟體進行,其中為能精確掌握量測點空間位置,特別利用混成網格方式進行空間離散,如圖4所示。應用此等網格檔,在搭配Moldex3D軟體專案建立與分析執行即可順利完成虛擬式的無損檢測技術剖析纖維排向效應。

另外,對於實際無損檢測技術執行纖維排向的觀察與量化流程,如圖5所示。該作法為先將樣品(以模型I為例子)分為三個掃描區域,並標記為黑色。每次只掃描一個區域,之後將待測區域置入Bruker Skyscan 2211進行樣品之微電腦斷層掃描(稱為CT scan)以獲取內部圖像,再將獲取數以千計之圖像利用Avizo軟體技術進行3D重建為具有纖維分布之模型,如圖5a所示。之後,再應用Avizo軟體內部之XFiber功能進行內部有纖維微結構的估算,完成纖維排向特徵之量測與分析,如圖5b所示。之後,每一根纖維都可被個別截取並且確認其空間座標,如圖5c所示。
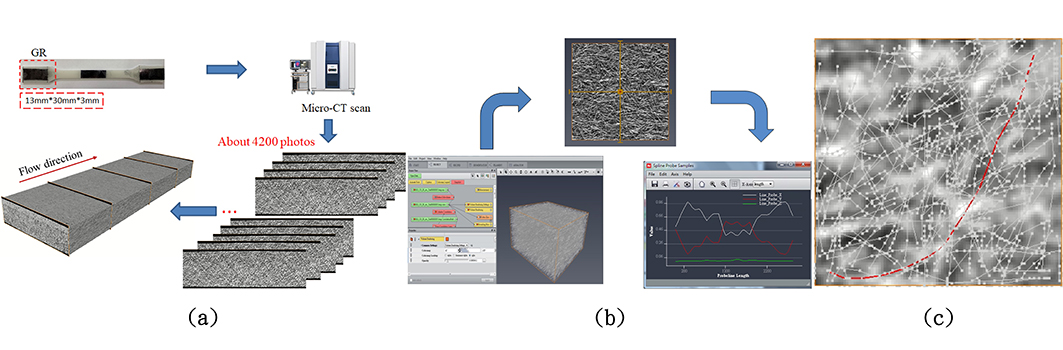
結果與討論
應用無損檢測技術進行纖維排向之預測與驗證
為了解射出產品熔膠內之纖維排向變化,此處利用兩種無損檢測技術作為探討之依據,一方面利用Moldex3D®軟體執行模擬分析預測,另一方面,將實際射出成品透過微電腦斷層掃描進行內部影像拍攝,再利用Avizo®軟體進行影像處理與分析,結果如圖6至圖8所示。其中,圖6a為模型I在B3量測點時之纖維排向張量模擬分析預測之結果。此結果顯示在接近澆口區域(GR),纖維排向張量主要由平行流動方向之分量A11所主導。圖6b為利用微電腦斷層掃描及影像處理分析後之實驗結果,此結果顯示雖然纖維排向張量絕對量值與模擬分析預測結果並非完全相同,但是纖維排向張量與模擬分析主要由平行流動方向之分量A11所主導之趨勢相當一致。
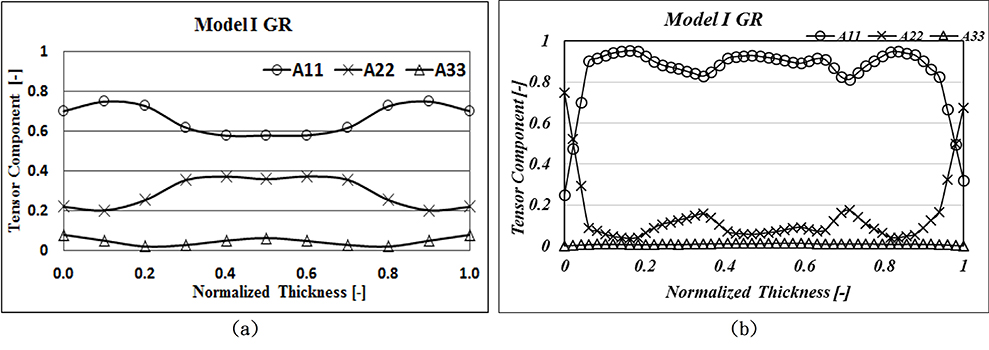
接著探討模型I之E2量測點(CR區域)時,比較模擬分析與實驗結果,發現模擬分析結果與實驗結果趨勢與量值相當一致。此時,因變化不明顯,此處沒有展示圖片。另外,當我們移至模型I之H3量測點(FR)時,圖7a顯示模擬預測纖維排向張量結果,其中在平行流動方向纖維排向張量A11在皮層區域會從0.65增加到0.8,但是到了芯層中間區域時卻降至0.3,而A22分量由低點0.15增加到0.6,此處產生A11與A22分量交錯現象,顯示纖維排向張量在芯層區域改由垂直流動方向之纖維排向分量A22所主導。再從實驗之結果觀察,如圖7b所示,可以發現模擬分析結果與實驗結果之變化趨勢相當吻合。此處可以進一步推論:當熔膠進入產品充填末端區域(ER)時,此時剪切作用力已經變得很小,而熔膠流動與纖維間的耦合效應變得相對明顯,此等作用會進一步推動纖維朝垂直流動方向運動。在此區域可明顯感受到熔膠流動與纖維間的耦合之效應。
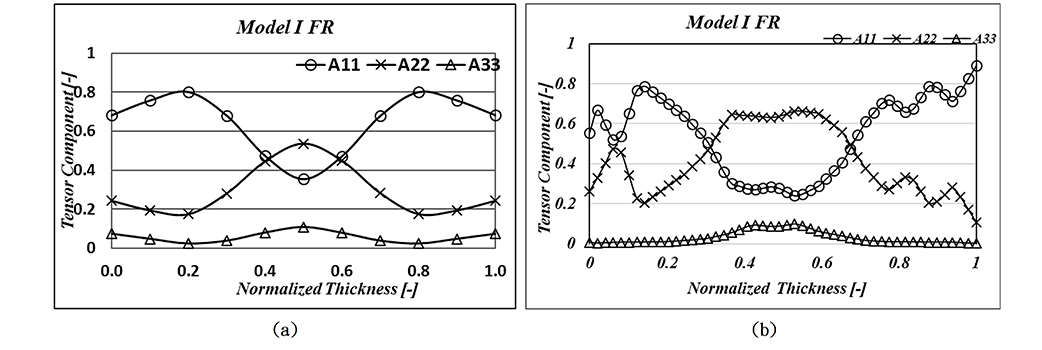
另外,我們也很好奇,同一條件下射出之模型II成品,其內在之纖維排向是如何變化呢?當我們觀察模型II之B3位置(GR區域)及E2量測點(CR區域)時,可以發現如同模型I所觀察到之現象,模擬分析結果與實驗結果趨勢一致(此處沒有展示)。再者,當我們移到模型II之H3量測點(FR區域)時,如同在模型I所見,圖8a顯示平行流動方向纖維排向張量A11會在芯層中間區域急降,而且會產生A11與A22分量交錯現象,顯示在芯層區域纖維排向張量主要改由垂直流動方向之纖維排向分量A22所主導。再從實驗結果觀察圖8b,可以發現實驗結果模擬分析結果趨勢相當接近。
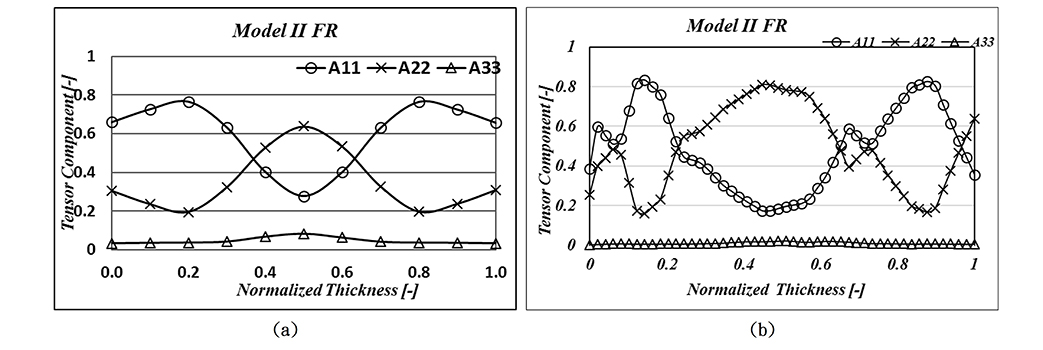
纖維排向變化與產品幾何變化關聯性探討
此處進一步探索纖維排向變化與產品幾何變化關聯性,針對產品巨觀特性變化,我們進行許多面向的思考,最後決定採用射出成品之各個邊長收縮變化作為評估與比對之標準。為此,我們在每一個區域之量測點利用無損檢測技術逐一完成纖維排向張量之模擬分析與實驗觀察。圖9是靠近澆口區域並從B1至B5纖維排向張量變化情形,此處先從模擬分析結果觀察平行流動方向纖維排向張量A11,它會先從單波峰型態,演化最後形成雙波峰型態,而且在此區域由平行流動方向纖維排向張量A11主導全局;再者,垂直流動方向纖維排向張量A22,先從單波谷型態展示,演化成具有微量之雙波峰型態。接著再從實驗結果觀察,從平行流動方向纖維排向張量A11及垂直流動方向纖維排向張量A22之型態變化,與模擬分析結果還算吻合,而且平行流動方向纖維排向張量A11主導全局,整體變化趨勢模擬分析也一致。
再者,除了詳細解析每一個量測點之纖維排向張量以外,也針對每一個量測點所分析量測之纖維排向張量進行平均,再將該點所得之纖維排向張量A11、A22、A33與流動方向空間位置作圖,結果如圖10所示。從B1至B5模擬分析結果發現,平行流動方向纖維排向張量A11從0.6逐步增加至0.7;垂直流動方向纖維排向張量A22從0.3逐步減少至0.2;而厚度方向之纖維排向張量A33保持在0.05左右。另一方面,圖10b為實驗結果顯示,平行流動方向纖維排向張量A11從幾乎都維持在0.8至0.9間震盪;垂直流動方向纖維排向張量A22則維持在0.15至0.2間震盪;厚度方向之纖維排向張量A33幾乎沒有變化。雖然實驗變化趨勢,沒有與模擬分析完全一致,但在此區域間,平行流動方向纖維排向張量A11主導此區域之纖維排向特性是相當一致。
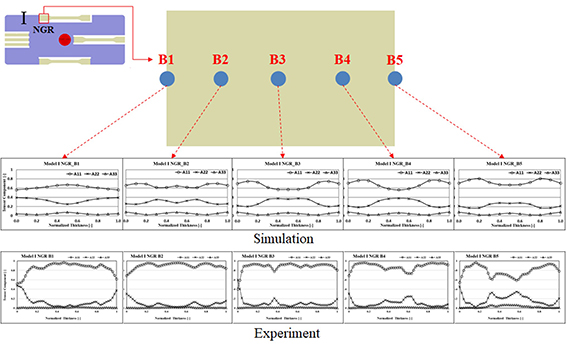
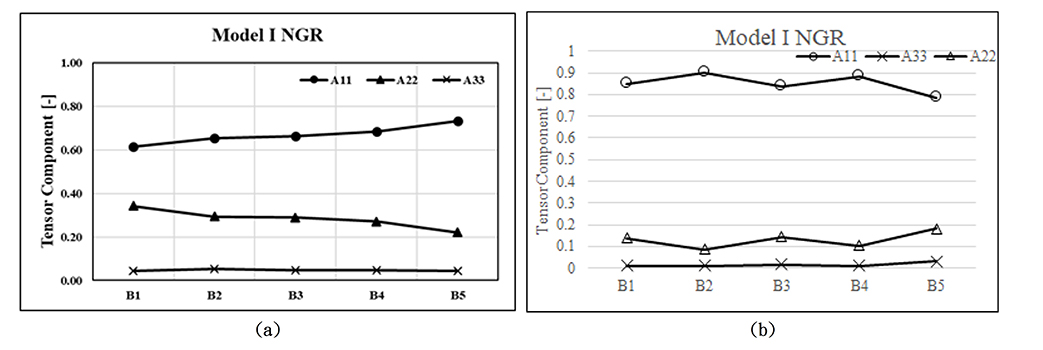
接著,圖11是以靠近澆口區域(GR)為例,用以定義射出成品幾何邊長收縮變化關係,其中圖11a的x為流動方向,y為垂直流動方向。此時四個邊界分別是上側(Lx)U、下側(Lx)D、左側(Ly)L、右側(Ly)R;另外,在圖11b中z為厚度方向,上側(Lx)U、下側(Lx)D、左側(Lz)L、右側(Lz)R。利用此等定義,再針對純料PP(稱為PP)以及含纖PP(稱為30SFPP)材料進行比較,從表2得知,當使用PP材料時,射出成品之6個邊都產生收縮。整體結果在平行流動方向收縮較小,而且每一組對稱邊(比如:上側(Lx)U及下側(Lx)D為一組;左側(Ly)L及右側(Ly)R為一組;厚度方向左側(Lz)L及右側(Lz)R為一組)收縮變化呈現對稱收縮。再者,當改用30SFPP材料時,射出成品之6個邊變形差異明顯,比如:在流動方向上側(Lx)U及下側(Lx)D約呈現膨脹2.75%,若與PP材料系統相比,收縮改善率3.25%。再由垂直流動方向來觀察,30SFPP材料系統之左側(Ly)L及右側(Ly)R約收縮2.0%,對比於PP材料時約改善1.25%之收縮。再從厚度方向探討,30SFPP材料系統之左側(Lz)L及右側(Lz)R約收縮3.0%,對比於PP材料時約改善0.3%。從此等結果並與圖10相比較得知,平行流動方向纖維排向張量A11所遠大於其他兩個方向,因此強化之作動最明顯,故射出成品內之纖維排向與射出成品之收縮變形有相當一致之關聯性。
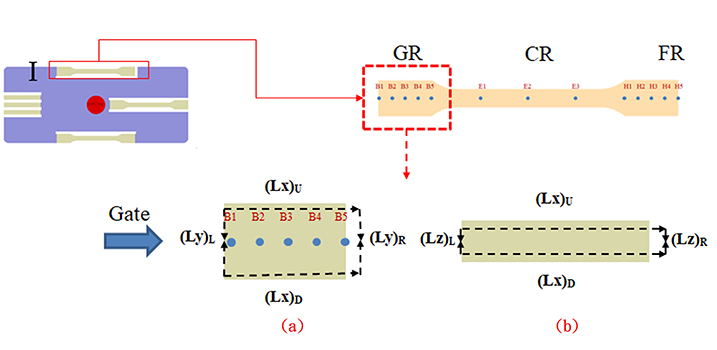
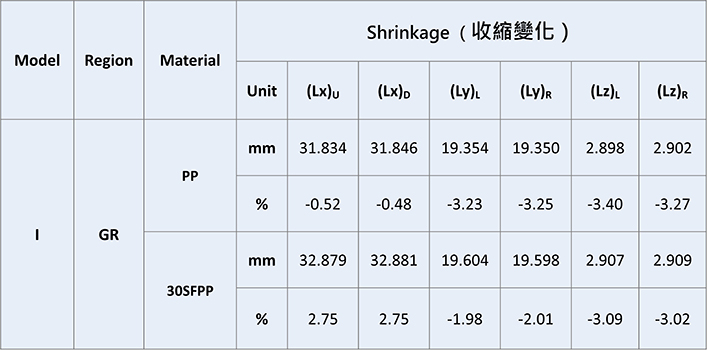
再者,當轉到充填結束區域(FR)時,圖12是靠近澆口區域並從H1至H5纖維排向張量變化情形,先從模擬分析結果(圖12a所示)可以發現平行流動方向纖維排向張量A11,會從H1之最高值逐步下降,最後在H5降為0.43;反之,垂直流動方向纖維排向張量A22,會從H1之最低值最後上升至0.43;而厚度方向纖維排向張量A33,從最低值上升至0.15。再從實驗結果觀察(圖12b所示),其中平行流動方向纖維排向張量A11會從H1之最高值逐步下降至最後H5為0.3;垂直流動方向纖維排向張量A22,會從H1之最低值上升至0.6;而厚度方向纖維排向張量A33,先從最低值上升至0.1。整體而言,模擬分析與實驗觀察變化之趨勢相當一致,特別是在H4至H5最後一小區,平行流動方向纖維排向張量A11將轉化成垂直流動方向纖維排向張量A22及厚度方向纖維排向張量A33。
接著,從射出模型I成品之充填結束區域(FR)收縮變形情況來探討,如表3所示。當使用PP材料時,射出成品之6個邊都產生收縮。整體結果仍是流動方向收縮較小,而且每一組對稱邊幾乎呈現對稱收縮。再者,改用30SFPP材料時,射出成品之6個邊變形差異很大,特別是左側及右側兩邊呈現收縮不對稱,比如:在流動方向上側(Lx)U及下側(Lx)D約呈現收縮0.4%,若與PP材料系統相比,該等邊長收縮改善率2.1%;再由垂直流動方向來觀察,30SFPP材料系統之左側(Ly)L收縮3.24%,對比於PP材料時,約改善0.62%之收縮,但在右側(Ly)R收縮為1.5%,對比於PP材料時,收縮改善提高至2.5%,此處明顯發現左側及右側兩邊呈現收縮不對稱現象,此時再由圖10得知,垂直流動方向纖維排向張量A22在H5遠大於H1,此等左右不對稱垂直流動方向纖維排向張量是引導此等左右側兩邊呈現收縮不對稱現象之主因,特別是左側收縮大,右側收縮小。另外,在厚度方向再次發現左側及右側兩邊呈現收縮不對稱現象,如同前述,此等不對稱收縮現象主要來自厚度方向纖維排向張量A33在左右兩側分布不對稱所引導。所以,透過射出成品之收縮變形結果與纖維排向變化情況,可以證明纖維排向效應確實與射出成品幾何變化有相當一致之關聯性。
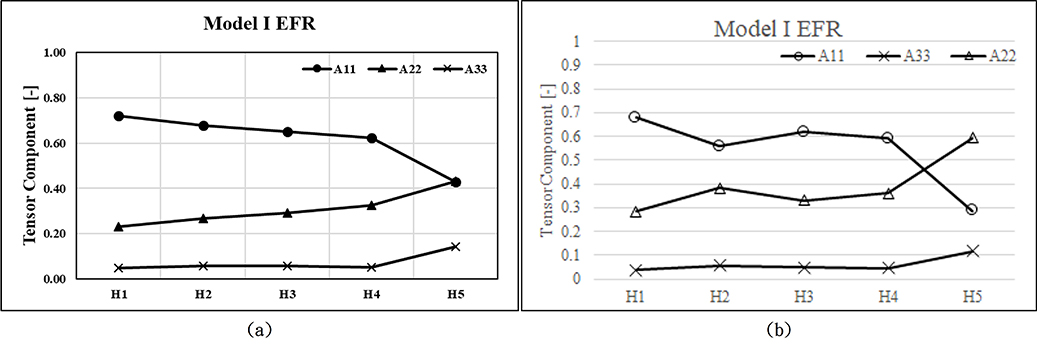
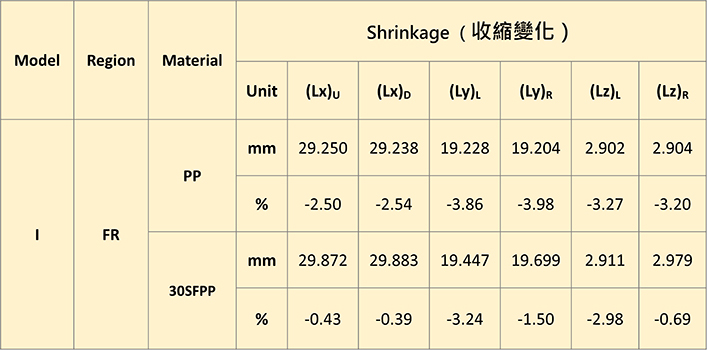
再者,轉移至模型II時,我們發現在GR及FR區域,纖維排向張量變化情況與模型情況非常相似,整體而言,在GR及FR區域時30SFPP材料系統之收縮量都遠小於PP材料系統,如同模型I所得結論,平行流動方向纖維排向張量A11所遠大於其他兩個方向,因此強化之作動最明顯,故射出成品內之纖維排向與射出成品之收縮變形有相當一致之關聯性。另外,在FR區域時,也會明顯發現左側及右側兩邊呈現收縮不對稱現象,此等左右不對稱是因垂直流動方向纖維排向張量引導此等左右側兩邊呈現收縮不對稱現象之主因,特別是左側收縮大,右側收縮小。另外,在厚度方向也在左右側兩邊呈現收縮不對稱現象也是由纖維排向張量在左右兩側分布不對稱所引導。所以,透過射出成品Model II之收縮變形結果與纖維排向變化情況,可以再次證明纖維排向效應確實與射出成品幾何變化有相當一致之關聯性。
結論
此篇文章主要應用無損檢測技術剖析纖維排向效應,先藉由有系統之模擬分析與CT-scan暨影像處理技術,成功進行深入探索纖維複合射出成品之纖維排向微結構特性,並且完成確認。再者,透過採用PP與含纖維30SFPP材料系統進行比較,結果顯示在靠近澆口區域(GR),成品之幾何外觀呈現左右對稱收縮行為,而且在流動方向收縮變化最小(甚至膨脹),此部份主要因為平行流動方向纖維排向張量A11主導該區域所致。然而,當觀察區域轉至充填結束區域(FR)時,特別是仔細探索充填最後區塊(標示為H1到H5)時,抵抗射出成品收縮方向之作動力方向,很明顯地轉至垂直流動方向與厚度方向,導致成品呈現左右不對稱收縮之外觀,此現象主要與纖維排向由平行流動方向轉至垂直流動方向及厚度方向所致。整體結果可以證明纖維排向變化效應與射出成品幾何收縮變化有相當一致之關聯性。
本文由淡江大學 化學工程與材料工程學系 黃招財 教授、王鈞正、蔡孟哲;成功大學 機械工程學系 黃聖杰 教授;逢甲大學 機械與電腦輔助工程學系 彭信舒 副教授、黃柏維;全立發機械廠股份有限公司 杜俊毅、許暐勳共同編撰。
感謝誌
本文作者非常感謝國科會多年之經費支持(計畫編號:MOST 110-2221-E-032 -015 -; MOST 108-2221-E-032-013-MY2; MOST 107-2622-E-006 -024 -CC1) 。
參考文獻
[1].EPA of USA, “Sources of Greenhouse Gas Emissions”, Web-source: https://www.epa.gov/ghgemissions/sources-greenhouse-gas-emissions, Accessed: 2023/07/12.
[2].S. Department of Energy report, “Lightweight materials R & D Program”, 2013 Vehicle Technologies Office.
[3].Othman, N.I. Ismail, M.A.A.H. Pahmi, M.H.M. Basri, H. Sharudin, A.R. Hemdi, “Application of Carbon fiber reinforced plastics in automotive industry: A review”, Journal of Mechanical Manufacturing, 1, pp.144-154 (2018)
[4].CompositesWorld Report, “The markets: Automotive (2020)”, Web-source: https://www.compositesworld.com/articles/the-markets-automotive, Accessed: 2020/08/19.
[5].L. Thomason, M.A. Vlug, “Influence of fiber length and concentration on the properties of glass fiber-reinforced polypropylene: Part 1-Tensile and flexural modulus”, Composites, 27A, pp 477-484 (1996).
[6].L. Thomason, “The influence of fibre length and concentration on the properties of glass fibre reinforced polypropylene: Interface strength and fibre strain in injection moulded long fibre PP at high fibre content,” Compost. Part A Appl. Sci. Manuf., vol. 38, no. 1, pp. 210–216 (2007)
[7].Folgar & C.L. Tucker, “Orientation Behavior of Fibers in Concentrated Suspensions”, Journal of Reinforced Plastics and Composites. 3(2), pp.98-119 (1984).
[8].G. Advani & C.L. Tucker, “The Use of Tensors to Describe and Predict Fiber Orientation in Short Fiber Composites”, Journal of Rheology, 31(8), pp.751-84 (1987)
[9].G. Advani, Flow and Rheology in Polymer Composites Manufacturing , Elsevier, New York (1994)
[10].Vincent, T. Giroud, A. Clarke, C. Eberhardt, “Description and modeling of fiber orientation in injection molding of fiber reinforced thermoplastics”, Polymer, 46(17), pp.6719-6725 (2005)
[11].Ortman, D. Baird, P. Wapperom, and Alex Aning, “Prediction of Fiber Orientation in the Injection Molding of Long Fiber Suspensions”, Polymer composites, 33(8), pp.1360-1367 (2012)
[12].H. Phelps, and C.L. Tucker III, “An anisotropic rotary diffusion model for fiber orientation in short- and long-fiber thermoplastics,” J. Non-Newton. Fluid Mech., 56, pp.165–176 (2009).
[13].Wang, J.F. O’Gara, and C.L. Tucker III, “An objective model for slow orientation kinetics in concentrated fiber suspensions: Theory and rheological evidence,” Journal of Rheology, 52, pp.1179–1200 (2008).
[14].Wang, and X.Jin, Comparison of recent fiber orientation models in autodesk moldflow insight simulations with measured fiber orientation data, International Conference of Polymer Processing Society (PPS), Banff, Canada (2010).
[15].C. Tseng, R.Y. Chang, and C.H. Hsu, “Phenomenological improvements to predictive models of fiber orientation in concentrated suspensions,” Journal of Rheology, 57, pp.1597–1631 (2013).
[16].H. Foss, H.-C. Tseng, J. Snawerdt, Y.-J. Chang, W.-H. Yang, C.-H. Hsu, “Prediction of Fiber Orientation Distribution in Injection Molded Parts Using Moldex3D Simulation”, Polym. Compos., 35, 4, pp. 671-680 (2014).
[17].Goris, U. Gandhi, Y.- Y. Song, and T. A. Osswald, “Analysis of the process-induced microstructure in injection molding of long glass fiber-reinforced thermoplastics”, SPE Annual Tech. Papers, ANTEC2016, pp.348-356 (2016).
[18].Gandhi, D. B. Sebastian, V. Kunc, Y. Song, “Method to measure orientation of discontinuous fiber embedded in the polymer matrix from computerized tomography scan data”, Journal of Thermoplastic Materials. 29(12), pp.1696-1709 (2016).
[19].Rigort, D. Gunther, R. Heger, D. Baum, B. Weber, S. Prohaska, O. Medalia, W. Baumeister, H. Hege, “Automated segmentation of electron tomograms for a quantitative description of actin filament networks”, Journal of Structural Biology, 177, 135-144 (2012).
[20].Weber, G. Greenan, S. Prohaska, D. Baum, H. Hege, T. Muller-Reichert, A. Hyman, J. Verbavatz, “Automated tracing of microtubules in electron tomograms of plastic embedded samples of Caenorhabditis elegans embryos”, Journal of Structural Biology, 178, 129-138 (2012).
[21].T. Huang and C. H. Lai, “Investigation on the Coupling Effects between Flow and Fibers on Fiber-Reinforced Plastic (FRP) Injection Parts”, Polymers, 12(10), 2274 (2020).
[22].T. Huang*, J.Z. Wang, C.H. Lai, S.J. Hwang, P.W. Huang, H.S. Peng (2022, Sep). Correlation Between Fiber Orientation and Geometrical Shrinkage of Injected Parts Under the Influence of Flow-Fiber Coupling Effect. International Journal of Precision Engineering and Manufacturing-Green Technology, Published Online: 2022/09/22; https://doi.org/10.1007/s40684-022-00473-5.