■羅德斯台灣
德國ShapeFab的成功經驗
高精度的CNC機器,對於特定幾何形狀,例如凹角或自由曲面,提供了獨特的加工優勢。從單件加工到小批量生產都可以對企業產生很大的效益。「在玻璃光學行業的玻璃加工方面,我和Ms. Jahn擁有超過26年以上的實務經驗,」ShapeFab GmbH & Co. KG的經理Oliver Seidel機械工程師表示。這位受過訓練的切削機械操作技術人員非常熟悉玻璃和陶瓷材料的特性和加工方法。在Ms. Jahn的建議下,她長期琢磨相關技術問題,兩人逐漸在多年的時間裡發展出了關於如何使用現代先進設備,如金屬加工行業常用的高速加工機,並開發比傳統加工工藝,更加合理和高效地進行易脆性材料加工的方式。
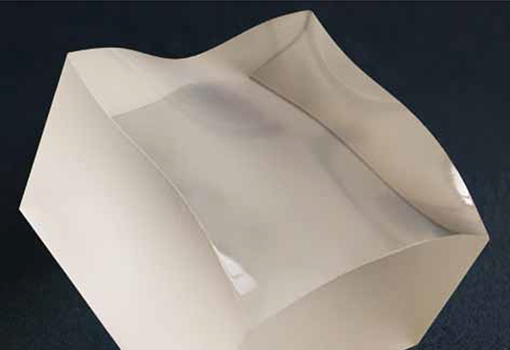
高速銑床提供三合一的優勢
當處理應用於實驗室、醫療相關、測量設備或雷射技術等的玻璃或陶瓷鏡片或其他結構時,傳統的三步工藝流程,包括磨削(Grinding)、研磨(Lapping)和抛光(Polishing),必須使用三種不同的加工系統。在Jena的一家初創公司現在僅僅使用單一設備即可完成所有的加工程序。傳統的加工流程每個工序必須在不同的設備上進行,有時甚至必須在不同的場域進行,這不僅耗時,也存在工序轉換過程中導致精度損失的風險。因此,他們長期以來一直在考慮在同一臺機器上的同一夾具中完成這三個操作的想法。
「與傳統的玻璃加工方法相比,我們在所有三個工藝階段都使用具有定義幾何形狀的工具,」ShapeFab公司的董事總經理 機械工程博士 Anett Jahn補充道。在傳統的玻璃加工中,僅在第一步使用具有鑽石磨料鍍膜的磨棒進行磨削,這些磨棒具有指定的幾何形狀。另一方面,隨後的兩個製程,研磨(Lapping)和抛光(Polishing),則使用鬆散的顆粒進行,這意味著必須考慮眾多的影響因素。
研磨(Lapping)是使用均勻大小的未黏結磨粒懸浮液在工件和配對工具之間的狹縫中進行的。兩個物體的恆定滑動相對運動確保了微小的材料被去除。結果是表面非常霧面,尺寸精度可達0.5µm,表面粗糙度Rz可達小於0.05µm。
另一方面,在隨後的抛光(Polishing)過程中,含有非常細的抛光劑顆粒的懸浮液在表面上在輕微壓力下使用柔軟的紡織品或氈布引導。目標是在盡量少的材料移除量的情況下使表面平滑。然後,表面非常光滑、透明且有光澤。然而,在複雜的幾何結構甚至自由曲面的情況下,如果使用這兩種加工方式,就會使製程更加複雜。相反地,在ShapeFab進行的所有加工都是使用具有定義幾何形狀且塗有牢固結合磨料的工具進行的。這具有一個優勢,即最終的幾何形狀完全符合CAD規範,就像在CNC加工金屬時可以實現的那樣。通過特別選擇的磨削工具,可以實現高達Ra 8 nm(奈米)的表面質量。
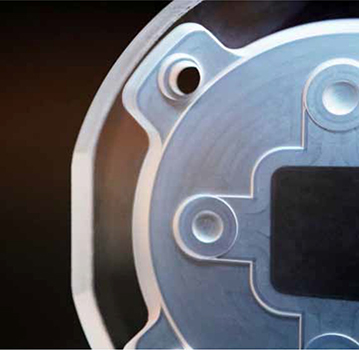
德國羅德斯五軸高速銑床協助我們有效率製作高精度零件
「我們這種製程的特別優勢在於,我們可以創造出相較於傳統製程可達到在幾何要求上,要求更高的結構,」ShapeFab的Adrian Helming說明:原則上,現在已經可以使用玻璃創造出一些原本只能用金屬製作的結構。舉例來說:擁有3D自由曲面的零件、透鏡陣列、具有緊固點或是鑽孔但是無框架的零件、實驗室需要的微流體零件、傳感器光學零件或甚至在難以觸及的位置上具有選擇性拋光表面的零件。由於生產過程高度自動化,零件在CNC控制下製造,並且主要使用標準刀具,因此具有特殊設計的單一零件都可以有效率地生產。由於使用了Röders提供的現代高精度五軸銑床,配備了研磨模組,公司在設計複雜的三維幾何結構方面擁有充足的自由度。這使得客戶能夠製造出以前被認為以這種形式生產是不經濟的零件。可實現高達5:1的長寬比,節距偏差小於5 µm,尺寸誤差小於3µm,可以實現最小結構尺寸為300 µm和表面粗糙度可以小於Ra 8 nm。而在孔加工的部份,即使在很深的位置也能實現僅有2 µm的真圓度偏差。
「ShapeFab面對對於大多數設計師而言仍然是新領域的製造技術。因此,我們憑藉著特殊專業知識支援我們的客戶,」O. Seidel說。儘管團隊規模不大,但歸功於整個製程自動化的有效運作,讓我們可以面對客戶提出的挑戰。從CAD設計到CAM規劃、從加工到品管的製程均已完全數位化。工件固定在Erowa的零點夾持系統的托盤上,該系統確保了高重複性夾持精度,因此可以在加工中心和坐標測量系統之間自由轉移,而不會損失精度。Werth測量系統不僅具有常規的探頭,還有一個白光感測器和一個拋光表面的光纖探針。由於在公司成立之前多年來對使用5軸加工中心處理玻璃和易脆性材料的深入研究,創始人在系統、軟體以及相關應用積累了豐富的專業知識。其中一個例子是可以直接整合到光學零件或自由曲面中的固定介面。這使得組件當中即使沒有調整元件也能夠以微米級的精度與終端應用整合。此外,使用高速精密五軸銑床整合研磨,不僅可以在玻璃鑽孔,甚至還可以製作螺紋。
對客戶的另一個優勢是可以使用符合他們自己設計的磨削工具。例如,具有較複雜幾何形狀的底部切削(undercuts)或孔並不成問題。同樣,通常容易出現在尖銳處的過度加工,也能夠在不出現邊緣破裂的情況下完成。
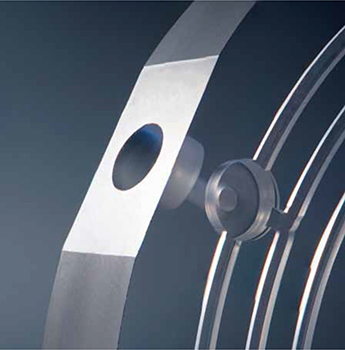
德國羅德斯RMS控制系統易學易用
「多年來,我們一直與機床方面的合作夥伴Röders有著良好的經驗,」A. Jahn強調道。這種合作開始於她多年前在Röders完成實習的時候。在這裡,她接受了對Röders系統的基礎訓練,並讓她找到處理硬脆材料的可行方案。使用由Röders以Windows介面開發的RMS6控制系統,直覺式的操作方式,學習起來很容易且提供了豐富的功能,可以編寫強大的加工編程。可以有效協助工程師提升加工效率。
關於Röders RXP 501DS
Röders HSC 5軸高速加工機RXP 501 DS設計旨在滿足高精度要求,並在加工硬材料時提供卓越的加工性能。它配備了無摩擦的線性直接驅動,與所有軸上的32 kHz時脈控制器相結合,實現了同樣動態和高精密度的加工。由於高校正頻率,可以實現顯著的加工時間縮短以及最佳表面質量。
實現這一點的一個基本前提是在所有軸上使用高精度的光學尺度——在精度方面,Röders絕不妥協。由於其高精確度和動態性,這台機器還可用於治具研磨。此外,Z軸配備了一個具有專利無摩擦的真空平衡器。
為了確保最大的熱穩定性,該設備擁有先進的溫度管理系統。流經所有重要系統組件的介質溫度控制精度為± 0.1 K。另一個特點是一個專用的基於個人電腦(PC)技術的控制系統,其功能精確地適應於HSC高精度銑削或治具研磨(Jig Grinding)的特定任務。由於Röders自行基於工業電腦和Windows操作系統開發了控制系統,硬體和軟體的更新可以根據需求隨時進行,因此機器的控制系統幾乎不會過時。
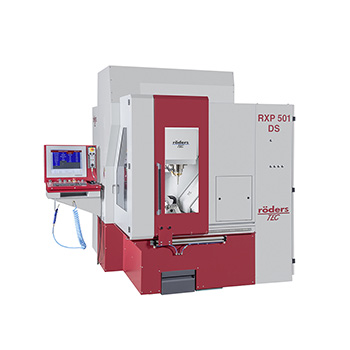