■中方科技 / 邱培其 經理
前言
本案例為TxMC供應商──台塑XX被要求要數位化管控其製程參數變化,並有系統化的方法可以控管該原料之品質,而非等產品生產完再靠檢驗篩選,因此本案重點為符合客戶要求,將現場機台製程參數變化進入中方AIQ & SPC分析即時品質、控管各站機台關鍵參數變化(P)與中方SPC系統(Q)結合。
台塑XX之前即與中方合作,本次目標為將新廠關鍵製程參數連線至中方AIQ系統,並由中方SPC系統將檢驗站自動檢驗數據分析後,將Q異常與P製程參數透過工單+批號+站別資訊結合讓現場工程人員可找出異常時關鍵參數變化的模式與數據,提供主管提升製程能力的科學化數據。要做到上述目標作法為:
- 結合台塑XX資料庫,啟動資料收集將製程參數變化數值導入AIQ資料庫。
- 針對各生產機台與生產料號及工單,提供參數上下限,並即時控管超出上下限發ALARM MAIL。
- 透過SPC資料庫結合AIQ系統資料庫,使用者可即時檢視各站品質是否正常,並在異常發生時提供控管人員即時訊息(如異常數量、數據、該異常工單與批號、料號異常時段、可疑製程機台與人員……)。
- AIQ可提供後段分析功能,利用數學模型對各類型機台製程特性曲線設計控管模型,有效控管不同製程類型機台特性變化。
- 提供製程品質生產履歷,可依料號、批號、機台種類、機台號碼、時間……看到每一批產品在各製程站的參數變化。
- 提供QIR自動報表功能,彙整後的製程與檢驗結果結合自動化分析報表自動定時傳送給相關主管與客戶。
具體目標
- 讓輸入人員不必人工輸入,直接轉AIQ與SPC進入本系統。
- 各料號生產時,如機台發生異常導致產品不良時,可即時警示。
- 可控管全廠產品製程變化,讓生產有異常時可即時發現與矯正。
- 讓管理者可掌握製程狀態變化,從第一線機台變化找出改善模型,提升高階產品品質。
- 符合客戶需求,掌握每批產品在各製程生產履歷與數據,可共同討論先進製程中該如何改善問題。
- 將每日每周每月的品質報表自動整理後發送給相關主管,可第一手掌握品質變化並因應之。
實施方法及過程
本案重點為將台塑XX新廠各項製程參數P與品質Q的數據資料,透過中方開發之AIQ & SPCPLUS分析各層別組合與異常規則,自動就各層別角度,如工單、料號、批號、站別、機台……分析各製程參數與品質管制項目的關聯,並自動發送異常通知與相關報表給現場工程師與管理者,達到即時改善異常,事後科學化分析異常,找出系統的相應對策與持續改善的數據管理機制。其中,本案的做法與重點可分為「現場製程參數彙總」、「現場資料看板」、「台塑XX P & Q串接機制」、「台塑XX自動報表」等四大項。
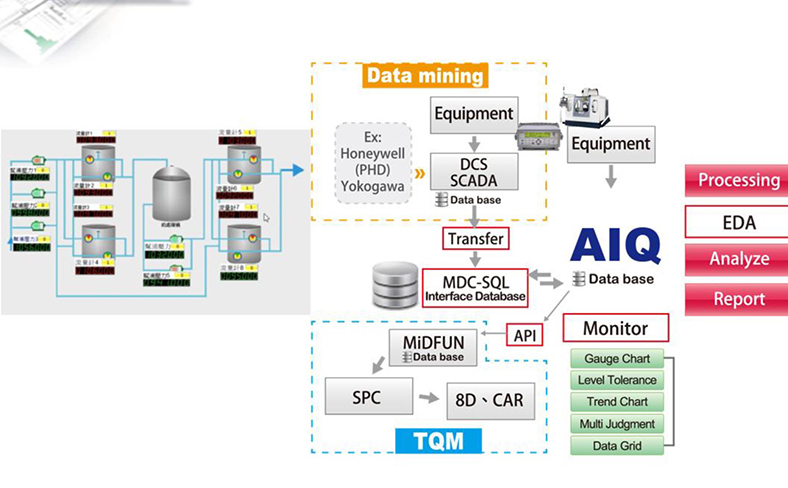
第一項:現場製程參數彙總
連線自動抓取製程系統的參數數據與資料,並存進AIQ資料庫。(流程說明如圖2)
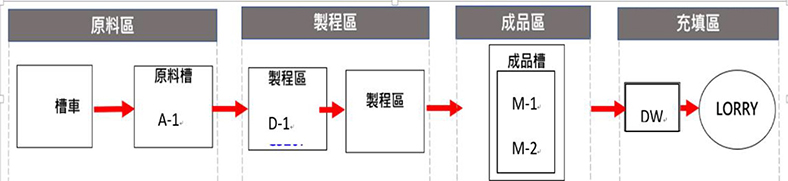
- 參數收集
– 充填區:壓差,4項。
– 成品區:液位,5項;Filter壓差,5項。
– 製程區:溫度,10項;回水溫度,5項;流量,9項;出料量,1項;塔壓力,3項。
– 原料區:溫度,3項;壓力,2項;液位,1項。
– 降溫區:溫度,1項;流量,1項;液位,1項。
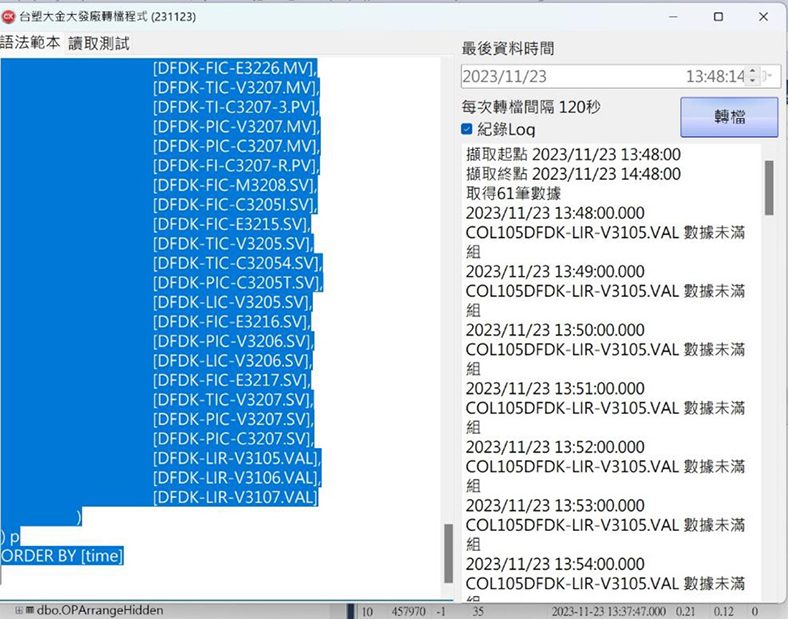
- 效益說明
– 取代人工定時抄寫。(原先費人工與資料量過少,導致無法判斷製程問題。)
– 自動化儀器連線後,數據參數自動匯入,可以進行製程大數據分析與品質參數結合追溯使用。
第二項:現場資料看板
利用AIQ每秒更新抓取的製程參數並與品質公式結合,將結果以最簡單方式呈現在螢幕看板上。
- BEFORE:無法看到現場機台即時看板的變化。
- AFTER:可直觀看到現場機台製程看板與是否異常。(如圖4)
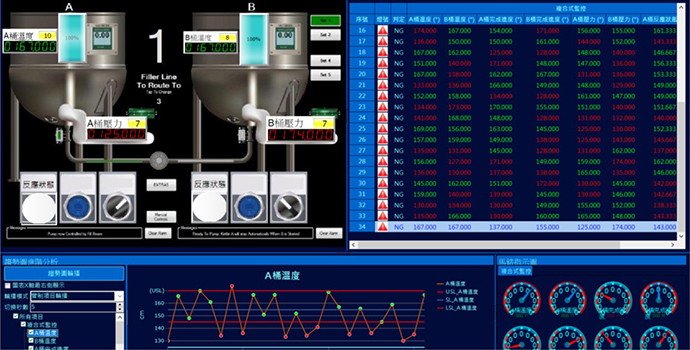
第三項:台塑XX P & Q串接機制
將抓取的數據集中至伺服器,並依照品管需求轉換成可於辦公室管制之管制圖。
- BEFORE:原來只能到機台端看PLC的數據變化無法中央控管且無法Q與P串接。
- AFTER:可直接在現場電腦直觀看到機台數據變化並直觀圖形控管。(如圖5)
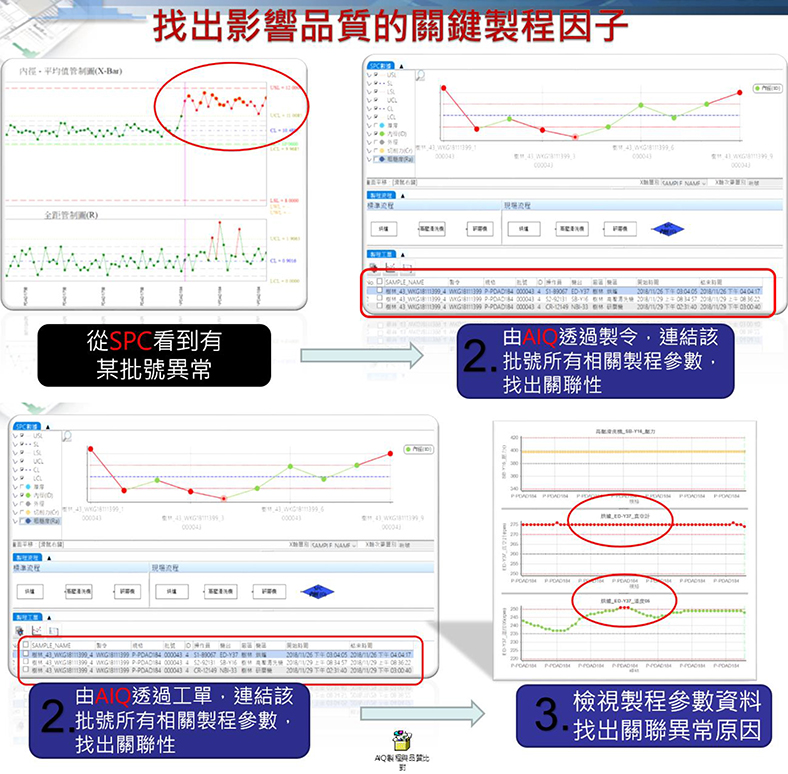
第四項:台塑XX自動報表
利用自動化整合報表將品質結果定時拋轉至主管Email並在每天定時上拋客戶端,讓台塑XX主管可直觀品質結果快速判斷。
- BEFORE:無。
- AFTER:可設定定時將生產履歷與品質項目拋轉至主管報表與客戶系統。(如圖6)
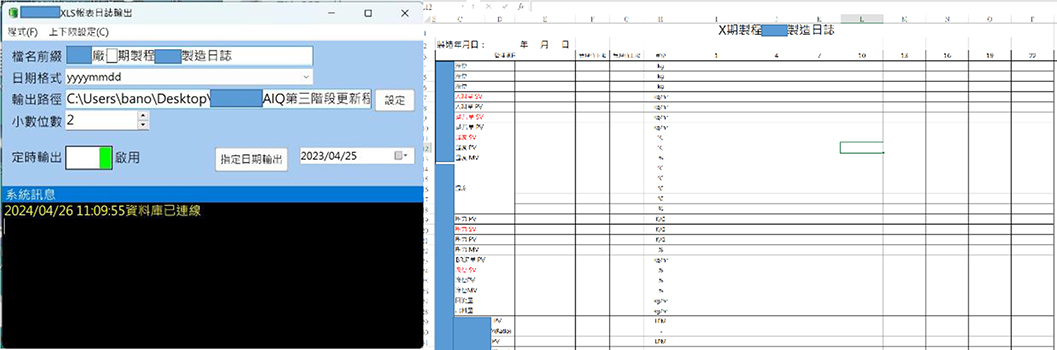
成果及效益
綜合表1與上述內容,台塑XX導入自動化系統後,一年至少可節省薪資900萬以上,降低不良成本至少600萬以上。此外,以上系統也是TxMC對化學製造供應鏈的基本要求,如上資料每日必須定時上傳才能持續得到客戶訂單,這不但可以科學化用數據提升供應商的品質能力與製程精進,更可以拿到高利潤且持久的訂單,打造更精緻與強悍有韌性的供應鏈群山,提升台灣廠商的系統競爭力。
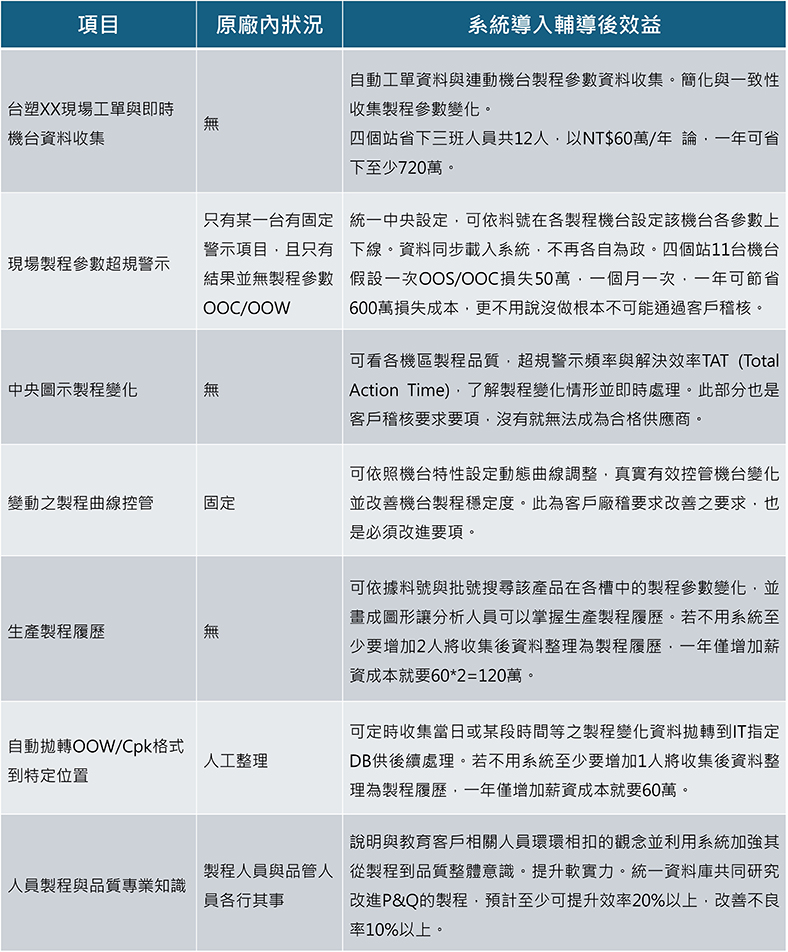