■上博科技
模具產業的轉型壓力
在全球製造業競爭日益激烈的背景下,台灣模具產業正面臨多重挑戰。生產成本攀升、技術人才斷層,以及市場需求多樣化,使傳統生產模式難以為繼。如何在保證品質的同時提升效率並降低成本,已成為當前模具產業最大的挑戰。伴隨熟練技術人員的逐漸退場,模具業也面臨技術與知識傳承的困境,長期以經驗為基礎的製造流程,隨著技術人才的減少,許多珍貴的製造智慧正在流失,亟需透過數位化與系統化方式保存與傳遞。
整合性的智慧製造解決方案:從設計到製造的革新
針對模具產業的痛點,上博科技提出了一套整合性的智慧製造方案。這套方案不僅涵蓋生產自動化,更著重於全面的數位轉型。透過對CAD/CAM系統的二次開發及CAPP作為模具廠進行同步工程的起點,企業得以實現從設計到製造的完整數位化流程。在這樣的模式下,過去依賴個人經驗完成的作業如今得以轉化為標準化流程,讓新進員工能更快速地適應工作,並降低操作的技術門檻。此外,數據整合為製造流程的優化奠定了持續改進的基礎,使企業能夠提升生產一致性並有效降低出錯風險。更重要的是,數位化使企業能精確掌握生產過程中的細節,使整體生產流程更順暢,並顯著縮短生產週期,進一步提高運作效率與競爭力。
成功案例:產能與效率雙提升
上博科技的智慧製造方案已在多家企業中展現卓越成效。其中,一家位於南部的業者成功導入模具自動化產線,順利完成數位轉型。該廠在採用上博智慧製造系統後,實現了72小時全自動化無人生產。該方案整合了多項生產設備,包括CNC、EDM等不同加工段,協助串聯製程各工段,實現彈性製造。導入後,整體製程時間縮短30%,產品品質穩定,模具交期更大幅縮短40%。在人才培育方面,該廠透過將老師傅的知識與技術數位化,新進人員僅需1個月即可操作機台,並在3個月內便能獨立作業,顯著縮短了人才培訓週期。
另一家總部位於台灣、將模具廠設在大陸的業者,在導入上博模具智慧製造方案後,成功實現了台灣運營、異地製造的企業營運布局。透過全數位化管理與標準化設計,該業者將模具設計時間縮短了40%。此外,全面整合的MOM製造營運管理系統涵蓋CNC銑削、EDM放電及CMM檢測等環節,成功實現機台運行「0」撞機,並將加工失誤率降低90%。後續的第二階段方案更進一步將模具廠內多條自動化產線,以多部機器人協作、AMR換線等方案進行整合,該廠區目前全日三班作業,僅需3人即可維持運作,大大降低現場對於人力短缺的困擾,且生產效率穩步提升,產能利用率達到80%以上,為企業在競爭力奠定了堅實基礎。
知識積累與虛實整合的創新應用
智慧製造不僅是可視化與機聯網的應用,或機器人自動上下料的自動化作業,更重要的是實現製造相關的資訊流與現場實際加工任務的整合,透過建立完整的數據管理體系,企業可將寶貴的製造經驗轉化為可複製的標準流程,這不僅解決了技術傳承的問題,更為企業建立起持續優化的基礎。上博科技結合工業物聯網技術,實現了虛實整合的創新應用,透過3D模型的精準設計與智能化的量測規劃,企業能夠自動生成檢測報告,確保產品品質的一致性。同時,模擬技術的運用可提前識別加工過程中的潛在問題,減少生產過程中的不確定性,提升運作穩定性。透過數據的整合與設備的串聯,生產的彈性與效率得到顯著提高,為企業創造了更多可能性。
未來展望:打造智慧製造生態系統
上博科技將持續深化智慧製造的創新應用,推動數位化、自動化與虛實整合技術的進一步發展,致力於結合跨領域技術,打造一個完整的智慧製造生態系統,幫助更多企業從傳統模式向智慧化全面轉型。在全球製造業加速轉型的浪潮中,智慧製造已不再只是技術升級的選擇,而是提升產業競爭力的必經之路。上博科技憑藉其創新的解決方案,正引領台灣模具產業走向更具競爭力的未來藍圖,為產業的可持續發展注入全新的生命力。
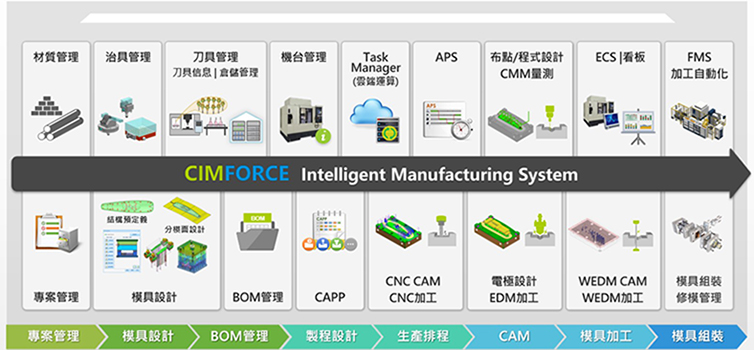
點擊下方連結,並訂閱上博科技Youtube頻道,獲取更多技術資訊!
https://youtube.com/@cimforce?si=NWRM0dY78ETNjbv5