■型創科技 / 王海滔 應用工程師
前言
塑件的氣痕,通常稱為氣紋,是在塑料射出成型過程中常見的一種表面缺陷。氣痕在塑件表面通常呈現出不規則的、淺白色的線條或圖案,有時這些線條看起來像是輕微的凹陷,觸感上可能會感到輕微的凹凸不平。它們可能呈現為細小的分支狀、蛇形或隨機分布的圖案,往往與塑件的流動方向一致。
氣痕不僅影響塑件的外觀質量,降低了產品的整體美觀度,還可能影響塑件的結構完整性和力學性能。在某些應用中,氣痕可能會導致表面塗層附著不良或影響組件的裝配。
氣痕形成基理
氣痕的形成主要是由於塑料熔體在模具內流動時,氣體無法有效排出而被壓縮,或是熔體前沿合流處發生氣體夾帶而形成的。
塑件的幾何形狀、壁厚變化、澆口位置和數量、熔體溫度、模具溫度、射出速度、選用材料、模具排氣等都可能影響氣痕的產生。例如,壁厚變化較大的區域可能會因為熔體流速不一致而導致氣體難以排出,從而形成氣痕。
常見原因與解決措施
- 選用與製品匹配的設備:如果射出設備與所需生產的塑件不匹配,如最大注射量與塑件及澆口料重之和的比例不當,可能會導致熔料滯留熱分解產生氣體,或因熔料受熱不均而難以成型精密製品。
- 檢查設備運行狀况:如噴嘴孔太小、物料在噴嘴處流涎或拉絲,以及機筒或噴嘴有障礙物或毛刺,都可能導致物料分解,產生氣體並形成氣紋。或是背壓不足,塑煉的熔膠含氣體。
- 改善排氣不暢:模具排氣槽設計不足或位置不當,會導致模具中的氣體無法順利排出,從而在塑件表面形成氣紋。
- 優化澆口設計:澆口尺寸過小容易造成剪切熱,導致物料分解,產生氣體並形成氣痕。澆口長度過長也會增加氣痕產生的可能性。
- 控制模具溫度:熔膠溫度或模具溫度過低,會使得熔膠在填充過程中冷卻過快,形成冷料痕,並導致氣紋的產生。
- 調整注射壓力和速度:注射壓力過高或注射速度過快,會使模具中的氣體來不及排出,受到急劇壓縮,從而產生氣紋。採用高壓低速注射,因為用慢速進行射膠,型腔中的氣體壓縮得較慢,氣體有時間擴散到塑件和模腔間隙中的較大範圍,以至於氣痕較為不明顯。
- 保證原料乾燥充分:原料中含有水分或未充分乾燥,會在射膠過程中產生水蒸汽,形成氣紋。
- 選料考慮流動性:某些塑料熔體流動性差,容易在模具中產生氣體,且不易排出,導致氣紋的形成。
- 選料考慮耐熱性:耐熱性差的塑料在高溫或高剪切力下容易分解,產生分解氣體,這些氣體如果不能及時排出,也會形成氣紋。
- 控制環境濕度:射出設備所處的環境濕度大,會導致模具內壁凝結水珠,這些水珠在射出過程中汽化成水蒸氣,如果不能及時排出,也會產生氣紋。
- 優化壁厚設計:塑件設計時壁厚過渡不恰當,會導致熔膠在填充過程中冷卻不均,形成氣紋。
總結
總的來說,塑件氣紋的產生是個複雜的過程,涉及射出設備、模具設計、生產工藝、塑料熔體自身、環境因素、排氣系統設計、原料質量和產品設計等多個方面。通過綜合考慮這些因素,並採取相應的消除措施,可以有效解決氣紋問題,提高塑件的整體質量。
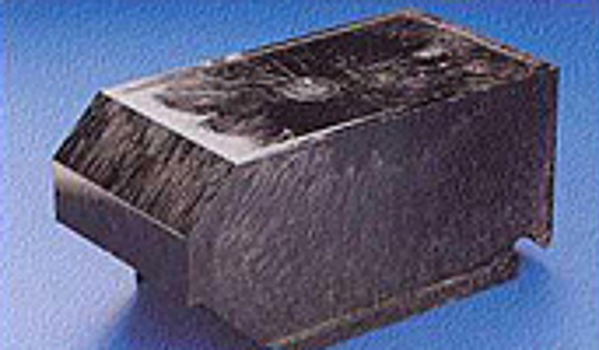
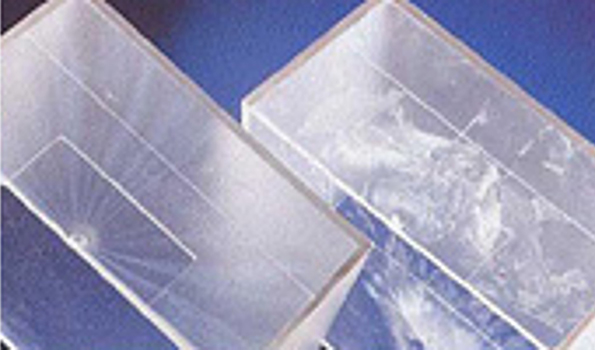
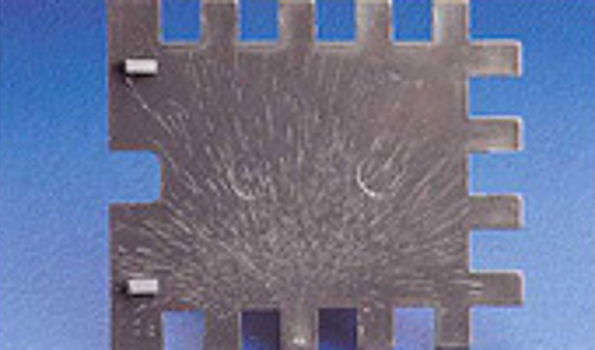