■達明機器人
前言
工業自動化的自動運輸需求不斷攀升,AGV (Automated Guided Vehicle) 自動導引車行之有年,廣泛運用在工廠和倉庫中,負責物料的裝載、卸載、移動、儲存和運送。隨著工業4.0時代來臨,智慧工廠需要更具彈性且快速導入的應用,於是出現以機械手臂結合自動導航搬運車的自主移動機器人(AMR-Autonomous Mobile Robot)。
整合手、眼、腦、腳的智慧設備──AMR
AMR是以機械手臂結合自動導引車,可使機械手臂具備自主移動能力,無限擴大工作範圍,加工或存取動作不再侷限於單一工作站。多部AMR在生產線來回穿梭進行多站工作,可大幅提升工作效率,適用於智慧製造少量多樣化的產線。AMR所搭載的機械手臂關乎使用彈性,如內建視覺的達明協作機器人的AMR,以機械手臂結合自動搬運車、機器視覺及電腦系統,等同於整合手、眼、腦、腳的智慧機械設備,為使用者帶來高彈性有效率的解決方案。
當AMR使用達明機器人導入製造業等應用時,內建智慧視覺的「眼睛」能彌補自動導引車的行走誤差,並精準定位進行快速的取放任務,提高生產稼動率,無須額外整合視覺,降低整合的時間與費用。視覺定位檢測可透過TM Landmark快速複製,以臺灣半導體產業某客戶為例,廠內單層有10臺AMR,需對應108個設備存取點(loadport/stocker/E-rack),手動教導點位需24個工作天,但是透過TM獨家專利TM Landmark──跨手臂點位共用套件,快速複製點位,只需要1個工作天即可快速完成108個loadport的設定,效率提升數十倍,後續的站點維護也可大幅縮短時間。除此之外,當產線面臨人為的碰撞,或是天災地震的侵襲,皆可透過視覺定位檢測,快速恢復原先設定,避免長時間停機停線。以及當產線有變動時(例如:擴線/移線,製程設備更動),可達成快速部署,大幅度增加導入彈性與設備可利用率。
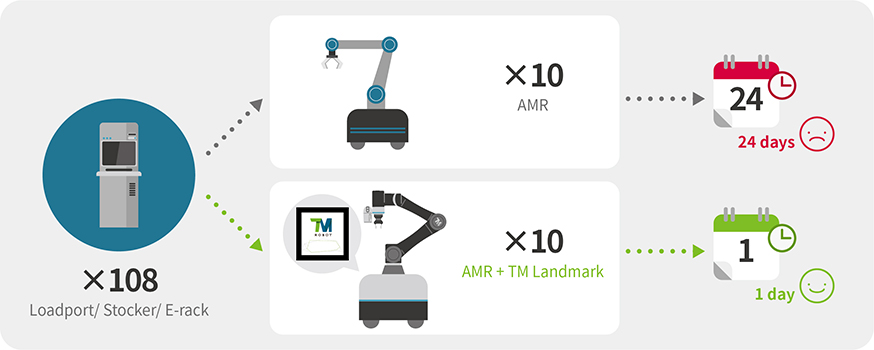
除了半導體大廠之外,臺灣知名航太產業龍頭的漢翔航空工業也積極導入AMR使用達明機器人的案例,除了複合材料零組件塗膠製程,及發動機零組件刻字檢測自動化之外,也使用多臺AMR進行大範圍廠區內材料的運送,以往人力從揀料到運送到工站,需耗費數十分鐘到一小時之久,透過AMR只需事先規劃送料排程產線上線前即可預先送達。除了「眼睛」之外,AMR結合「大腦」也就是連接公司生產管理控制系統,可結合工單生產管理,確保不會有缺料的情形,除了定時派車運送產線材料之外,若是個別工站緊急調料,亦可透過平板電腦臨時下單派車補料,充分達成生產線各種需求。
AMR在2018年的市場規模約為2.6億美元,而2025年將以15.85%的複合成長率成長至7.4億。倉儲與製造業生產線,是工業用AMR主要使用的區域。隨著物聯網、工業大數據分析應用等技術,正在翻轉供應鏈和物流之間的關係,在倉庫裡建立AMR為製造業之趨勢,透過AMR讓撿貨員能夠順利將物品運送到不同工站,取代以人力運送的方式,AMR也是工業4.0下彈性製造的最佳代表。
結語
近兩年COVID-19疫情衝擊全球經濟,間接催化機器人技術與市場的快速發展。蓬勃發展的AMR,是整合手、眼、腦、腳的智慧機械設備,與傳統的AGV相比,能做到精準定位上下貨、環境監測等工作,多元彈性的應用模式,大幅提升AMR的應用價值,除了製造業,未來不同產業也能看到AMR的身影,如醫院照護、環境清潔、餐飲業、倉儲物流業、零售通路業等。