■青島維特信息科技有限公司 / 張祥富 經理
前言
模具設計是模具整個製造過程的源頭,模具設計決定了模具製造的效率、品質、成本、加工工藝,同時也決定了射出生產的穩定性、效率和成本。所以模具設計非常關鍵,是模塑製造的核心技術,需要系統性規劃,為後續智能製造做好基礎。
為了提升模具設計的效率、準確性、降低設計失誤、降低模具設計對人員技術的要求,企業應當重點加強:
- 模具企業設計標準化和智能化設計理念,培訓、輔導落地、執行;
- 梳理標準化體系包括:標準化零件、設計規範標準化、作業模式標準化;
- 將企業標準化技術通過系統軟體的方式固化,人人按標準設計,保證標準化執行落地;
- 通過智能系統完成企業技術的積累和沉澱,避免人員流動造成對企業技術能力的影響;
- 通過建立大量的標準庫、標準模組並開發大量的快捷集成設計方式,大幅提升設計效率;
- 通過智能化設計系統完成大部分重複和繁瑣的工作,解放設計師將主要精力用在模具和核心技術上如:分型、結構合理性、工藝優化等與產品相關的技術。
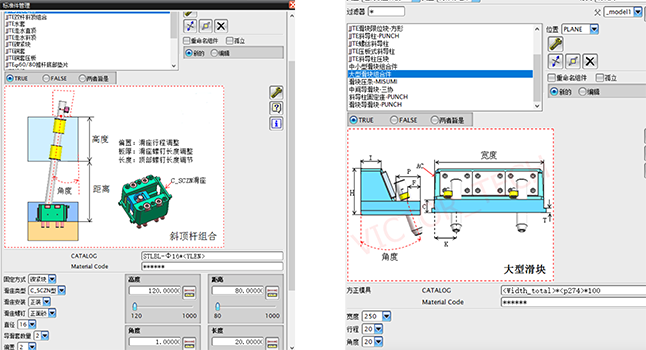
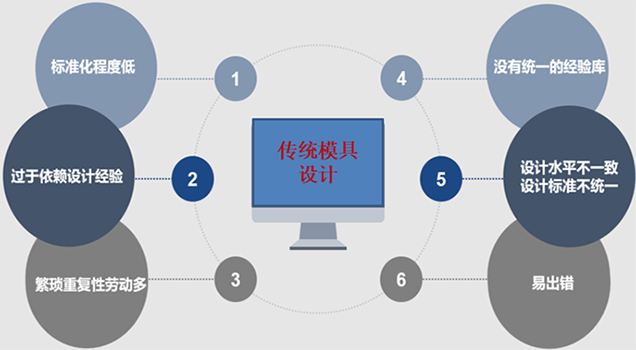
模具企業競爭激烈,交期、成本、品質壓力大,傳統模具設計已經不能滿足市場需要,需要全面系統性變革,利用先進軟體技術執行標準化並融入豐富的專家經驗變革模具設計模式:
- 平臺化智能設計,協同設計。
- 建立標準化專家技術庫、知識庫、標準化設計,降低設計人員技術要求。
- 系統規劃標準化零件庫、結構設計模組化,提升標準執行統一性和準確性。
- 通過標準快捷設計系統,大量減少工程師繁瑣、重複性的操作,釋放設計師時間和精力,專注於產品成型及核心技術工藝。
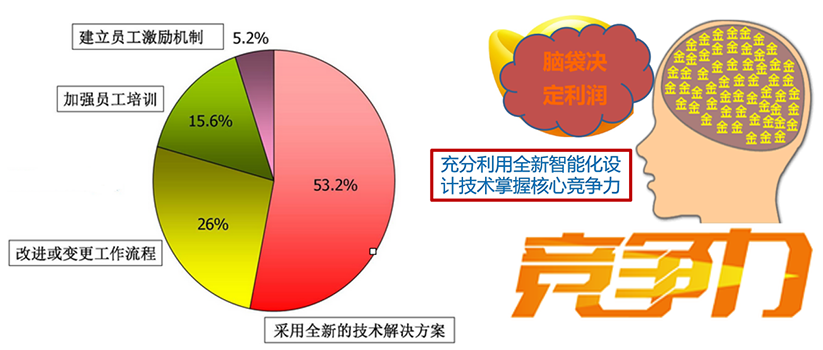
標準化整體優勢
設計前期零件標準化的完善,採購成本降低,設計效率提升,模具週期縮短,不斷增強企業整體競爭力。同時設計標準化後,編程和製造部門也可以進行相應的加工標準化,實現更加高效統一的生成節拍。
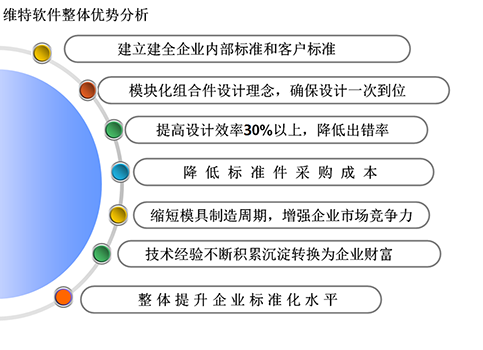
模具行業標準化發展趨勢
隨著模具行業信息化、數據化、自動化、智能化、工業互聯網的發展模具設計向智能化轉型升級是必然趨勢。模具設計是模具製造的源頭,標準化、數據化、協同化、智能化模具設計必須要系統性規劃。
標準化也是企業管理和技術沉澱的最好方式,模具行業的轉型升級設計是關鍵,是模具智能製造的源頭。標準化無疑是模具製造過程中推動信息化和自動化的源頭,一步跨不到信息化、自動化、智能化,很重要的基礎就是前端的標準化,決定了能否順利推動模具企業整體信息化、自動化、智能化成功的關鍵。
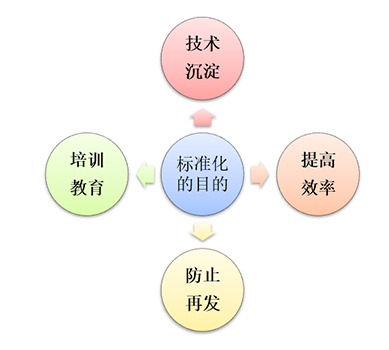
模具企業標準化搭建包括
管理流程、作業標準、工藝標準、技術標準、零件標準、公差標準、模組化、設計標準化等。
標準化的積累也是後續進行模具自動化技術和管理的基礎工作,積累到一定程度就很容易實現自動化和系統化升級。
一流企業永遠是在做標準,能成為行業標準的制定者,一定是行業的引領者。優秀的模具企業都非常重視內部標準化體系建設。
標準化、信息化、自動化、智能化是行業發展方向和趨勢,而標準化是關鍵基礎,作為所有數據輸出的源頭,設計標準化的程度提升會大大縮短設計週期、降低採購成本,同時也可以帶動後續加工部門的標準化程度。
模具行業競爭越來越激烈,如何確保短週期、低成本,通過搭建起企業標準化設計平臺,實現信息技術與生產管理高度融合,能夠顯著增強模具企業研發的設計能力進而縮短研發週期,降低研發成本,降低設計準入門檻;同時也是企業對外實力展示的一個窗口,可以站在更高的平臺與同行競爭,確保自身優勢。
模具企業標準化帶來的好處
- 智能模具設計的源頭標準化,是後續加工工藝、編程、加工等標準化的基礎;
- 讓模具開發和製造有序進行;
- 誰做都一樣,降低人為因素影響;
- 模具開發效率提升,模具品質穩定有保障;
- 模具成本降低。
模具企業標準化的未來
- 運用技術將標準固化;
- 利用大數據分析標準化,降低經驗的影響;
- 共享標準化,從而形成行業標準;
- 標準化會同精益製造相結合,大數據分析將充分發揮作用,讓標準更準。
應用案例
案例一:自動滑塊設計
設計人員把滑塊頭部設計完成後,後端自動匹配成組生成,組合標準件(耐磨板、壓條、斜導柱、導滑)全部匹配到公司標準,確保所有設計人員對於標準執行的統一,整個滑塊生成不到1分鐘,在標準化基礎上極大提升了設計自動化效率。
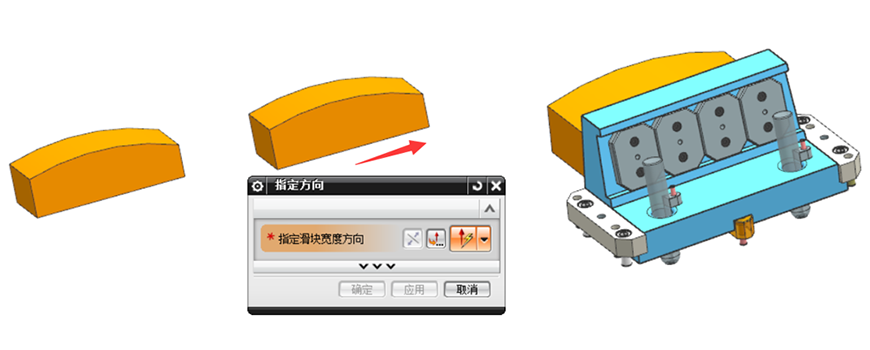
案例二:自動斜頂設計
設計人員把斜頂頭部設計完成後,後端自動匹配成組生成,自動定位匹配到模架對應位置上,組合標準件(滑座、導滑塊)全部匹配到公司標準,包括假體符合要求,確保所有設計人員對於標準執行的統一,實現批量操作,批量生成,在標準化基礎上極大提升了設計自動化效率。
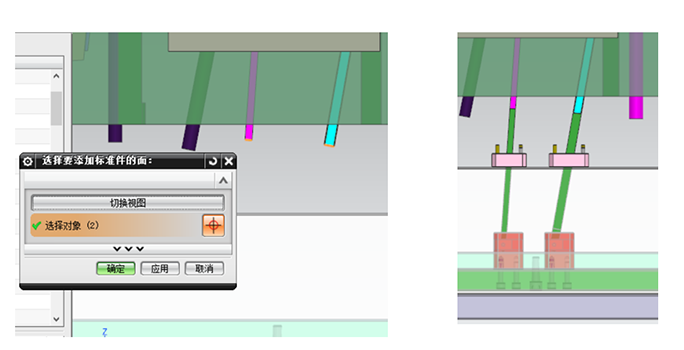