■Sodick / 張翼 副部長
前言
近年,金屬3D列印工藝隨著工藝的日趨成熟,在模具中特別是塑料模具和射出模具上的應用已經越來越多。目前很多人已經認識到了通過金屬3D列印製作模具時能夠在模具的內部作出冷卻用的3D水路,從而能大幅度的提升塑料模具、壓鑄模具的冷卻效率,進而縮短冷卻時間和提升產品的品質。
金屬3D列印工藝雖然可以提升傳統模具的冷卻效率,但是由於受目前列印速度的制約,在模具製作時相較于傳統製作來說仍然有時會存在工時偏多的現象,這也往往成為人們對金屬3D列印應用產生猶豫的原因。
然而,金屬3D列印與傳統加工相比,工時增加還是減少這個其實要根據工件(模具模仁)的形狀特徵去綜合判斷的。有些模具形狀特徵比較簡單,傳統加工容易,這樣使用傳統加工時的工時就會比使用金屬3D列印時少;有些模具形狀特徵比較複雜,傳統加工工序多,這種情況使用金屬3D列印+部分傳統加工所使用的工時就很可能會比使用傳統加工少。
下面就給大家介紹一個我司近期金屬3D列印製作模具實現較傳統加工工時縮短的一個事例。
3D列印方法與傳統加工方法對比實例
本案例產品存在需要放電加工的細節特徵(圖1中紅色箭頭所指的鋸齒樣細節特徵),3D列印加工可以實現均勻的餘量,減少電極的數量和放電的工時。
- 零件:凹模型腔(射出成型);
- 尺寸:φ54 x L34mm;
- 水管:隨形水管;
- 材質:STAVAX (SUS420J2);
- 硬度:HRC52±2;
- 數量:16個。
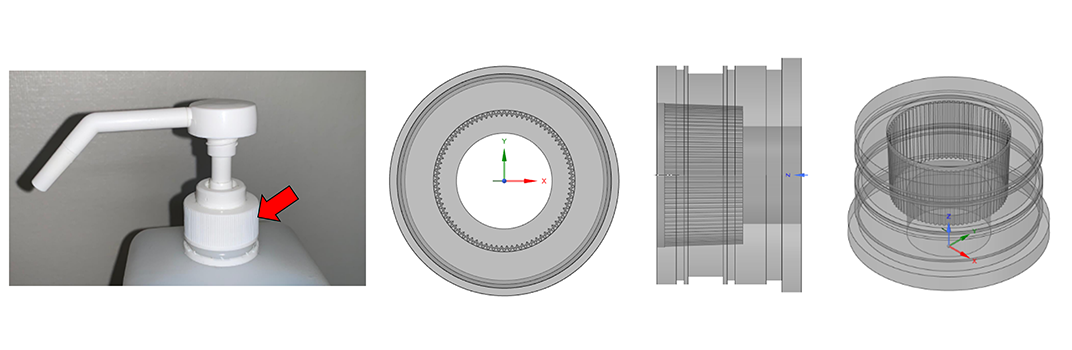
加工流程的比較
- 傳統方法
下單備料→材料到達→熱處理前粗加工(車床加工)→熱處理(淬火・回火)→車床精加工/電極加工→放電加工。
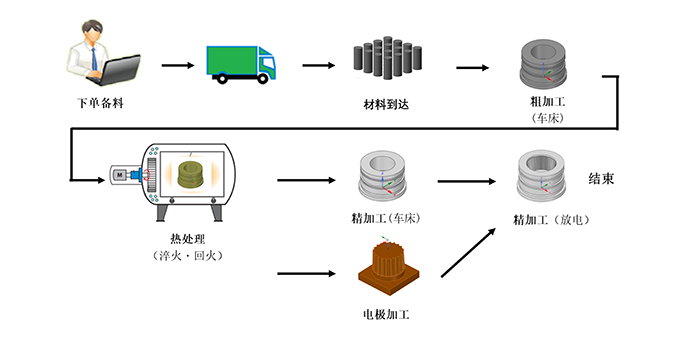
- 3D列印方法
3D列印→線割→熱處理(淬火・回火)→車床加工→放電加工。
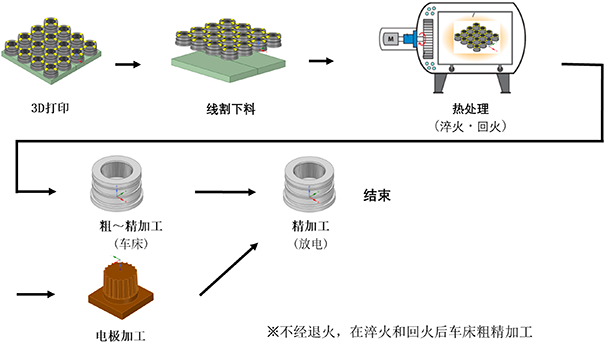
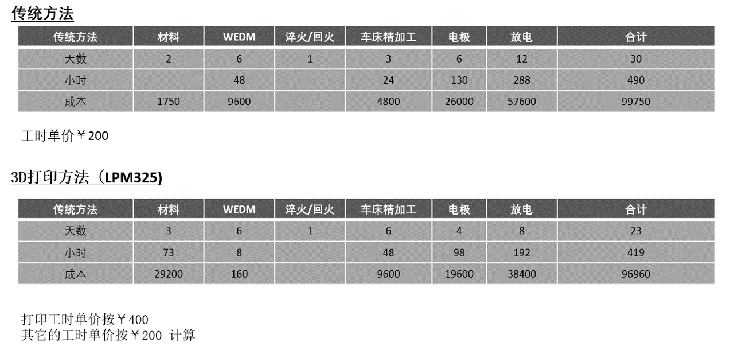
放電加工時間縮減的理由
- 傳統方法
-車床粗加工後,鋸齒部分還只是個圓形,鋸齒處餘量不均勻。
-放電加工是從鋸齒細節頂部開始,因此放電加工時間較慢。
- 3D列印方法
-加工完成的零件,鋸齒細節餘量均勻(單邊預留0.3~0.4mm的加工餘量)。
※注:消除了不必要的加工部位,減少了電極的使用數量。
-放電加工是從鋸齒細節中間部位開始。因此放電加工時間更快。
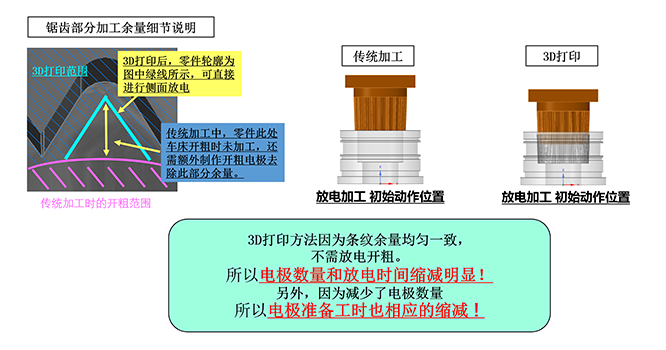
電極數量和放電加工時間比較
3D列印因為不需要放電開粗,電極數量削減32個!(如圖6)此外,3D列印可削減放電時間96小時!(如圖7)
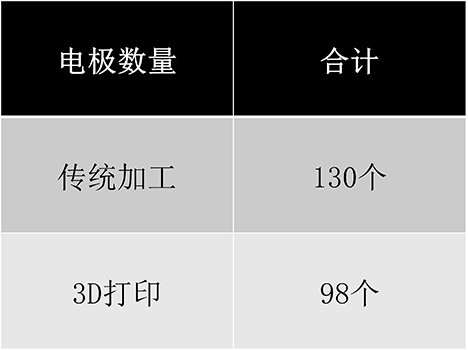
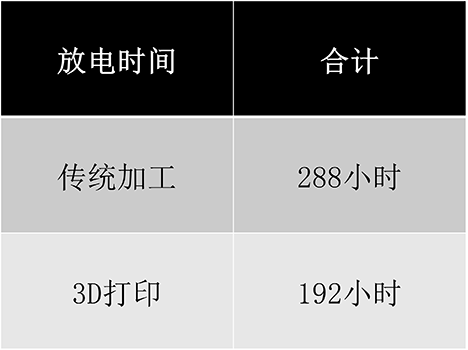
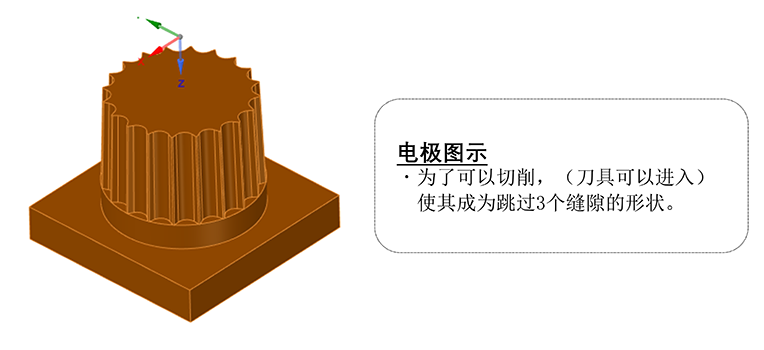
3D列印所具備的強力優勢:隨形水路
- 傳統水路樣式
-水路設計限制較多,要考慮傳統加工工藝的可行性(可加工性和可裝配性),水路很難達到充分均勻的佈局,模具溫差較大。
-零件側面需要進行水槽加工及密封槽加工。
-側面要套入O形圈,存在裝配風險(漏水、腐蝕等)。
-水路冷卻效率較弱。冷卻水從一個地方進入,在兩個方向分支,然後在一個地方匯合,一條水路要流經很多個零件,因此降低了冷卻效率(溫差大,流速低,換熱慢)。
- 隨形水路樣式
-水路設計不受傳統加工工藝的限制,水路加工簡單。
-可進行理想化設計,面面俱到,模溫控制能力很強,模溫溫差小。
-零件水路一次列印成型,加工簡單。
-零件水路無需組裝,沒有裝配風險。
-水路冷卻效率高,可每個零件配備一條單獨的冷卻水路,流程短、流速快、換熱快。
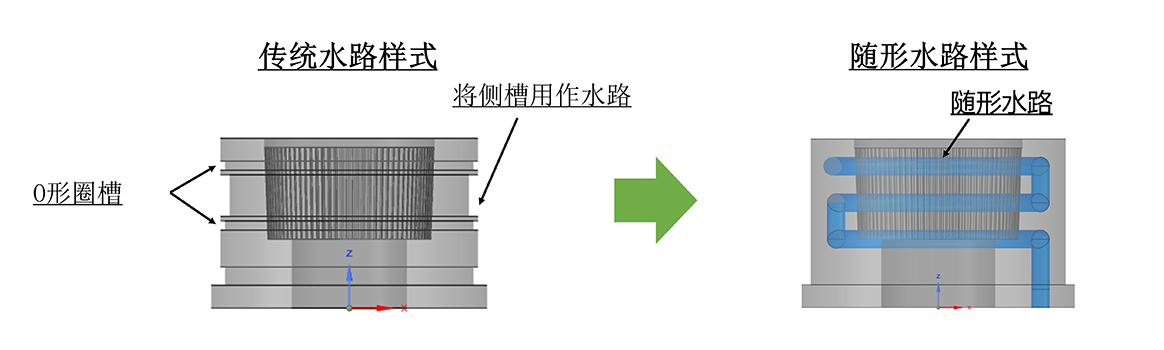
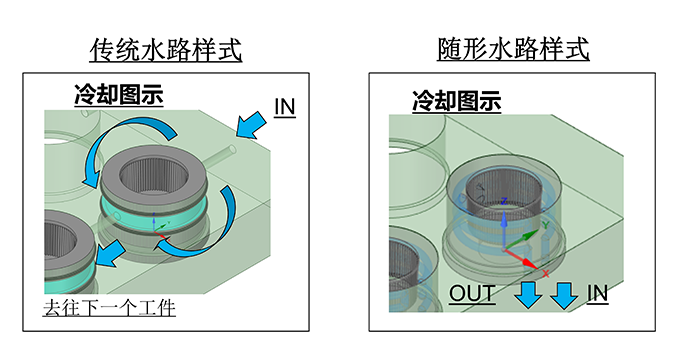
總結
總體看,3D列印加工方法相較傳統加工方法,工時減少了7天,費用減少了2790元。由此可見,3D列印方法可以實現削減成本和縮短工時的效果。
另外,3D列印的隨形水路優勢,可以幫客戶達到提高產品成型質量,提高產能,降本增效的目的。
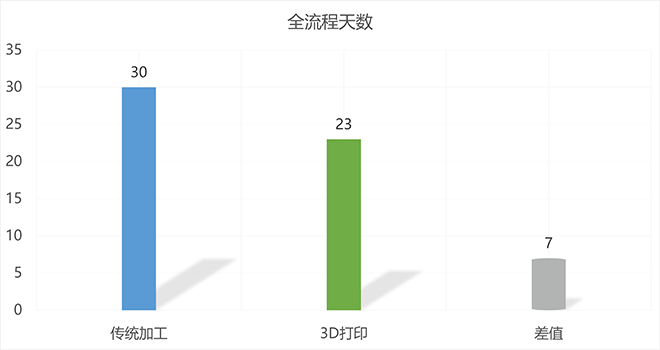
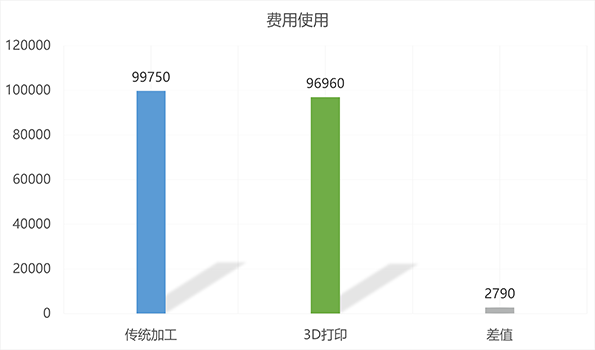