■科盛科技研究發展部 / 周祐陞 工程師
前言
射出成型中的塑料溫度控制,通常是利用螺桿的旋轉與料管上的加熱片,將低溫的固態塑料顆粒加熱成高溫的液態熔膠。熔膠溫度會影響到產品的品質,過高會有材料裂解、黃化等問題;太低則會降低材料的流動性、增加流動阻力。熔膠的溫度並不能透過射出機直接控制,而是受到塑化過程間接地影響。塑化過程中有三個主要條件會影響熔膠溫度,包括加熱片溫度、螺桿轉速與背壓。以下將說明塑化過程如何影響料溫。
螺桿轉速與料溫關係
螺桿旋轉會帶動塑料流動,過程中產生的剪切熱會使熔膠溫度升高。螺桿轉速太快會造成料溫偏離加熱片溫度太多;轉速太慢會則會增加計量時間,降低生產效率。由圖1可看出,當螺桿轉速越快,中心處的溫度越高;而兩側則維持在加熱片的溫度,造成熔膠溫度不均勻的情形。在提升轉速以降低計量時間時,需要注意隨之而來的溫升對塑料的影響。
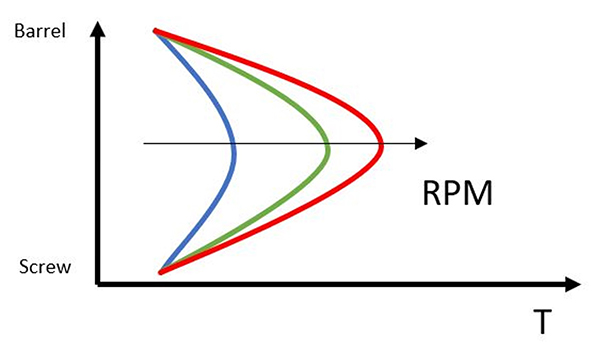
背壓料溫關係
計量時,螺桿會將熔膠輸送至料管前端,這些被貯存在前端的熔膠會產生壓力,當壓力大於背壓時,螺桿就會向後推動。若背壓太高,螺桿不易後退,塑料與螺桿接觸的時間變長,剪切生熱造成料溫上升;若背壓太低,螺桿後退速度太快,造成計量不準確,熔膠不夠緊密,可能含有空氣。背壓應與螺桿轉速相互配合,使塑料在螺桿內的時間適中,以得到好的料溫控制。
加熱片與熔膠溫度關係
加熱片一般有多個不同設定,可依照材料對溫度的敏感度進行設定。在塑料尚未融化前,加熱片提供主要的熱量。此時塑料的溫度會低於加熱片的溫度。隨著塑料融化並進入螺桿後段,剪切熱逐漸增加,此時熔膠的溫度有可能高於加熱片溫度。
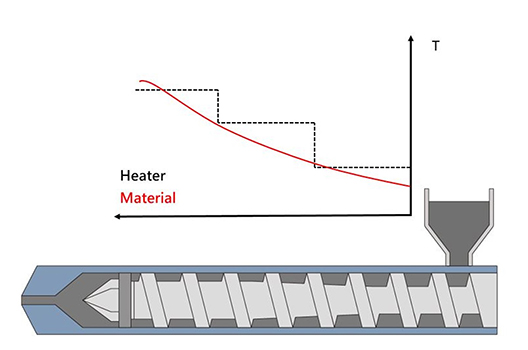
塑化模擬
塑化的過程中,物理上需要考慮塑料的相變化;幾何上則有螺桿旋轉的空間改變,這兩個因素造成模擬相當的複雜,一般需要將模型進行簡化。塑料從固態顆粒融化的過程可以被分成為三個部分[1]:固體床(Solid Bed)、熔化池(Melt Pool)、熔化模(Melt Film),相變化的模擬即以這三個區域為基礎進行延伸。螺桿的複雜幾何則可以使用去纏繞法,將螺桿與料管間的螺旋通道拉直成二維[2]或三維[3,4]的通道,再假設螺桿靜止,料管以反方向旋轉,即可將動態的計算域轉變為固定不變的空間,大大地減少計算的複雜度。以Moldex3D為例,只需要在視窗中填入螺桿的各項尺寸,軟體即可自動完成模擬所需的模型。簡化後的模型每次分析約在三分鐘以內,可以快速提供數據做為成型參考。
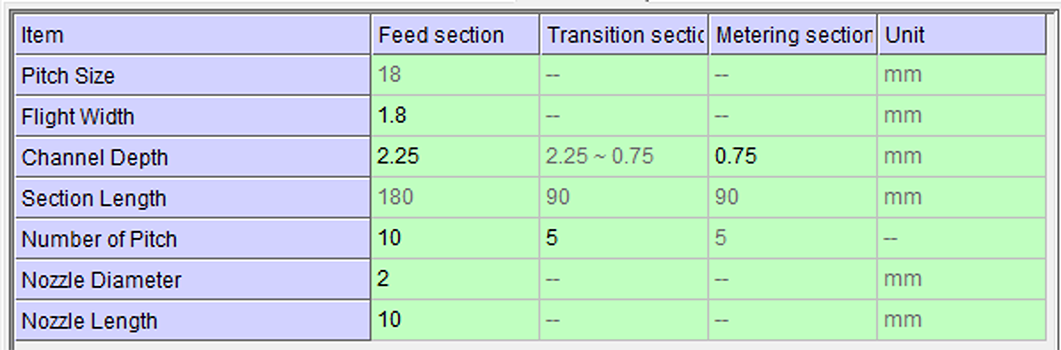
結果判讀
Moldex3D會呈現出螺桿各個位置的結果。以圖4為例,呈現的是各個不同截面下,從螺桿表面到料管表面的溫度分佈。我們最關心的通常是最後的料溫,從圖中可看到此處的最高溫度比加熱片約高出2℃。使用者可以藉此確認料溫是否控制在合適的範圍。
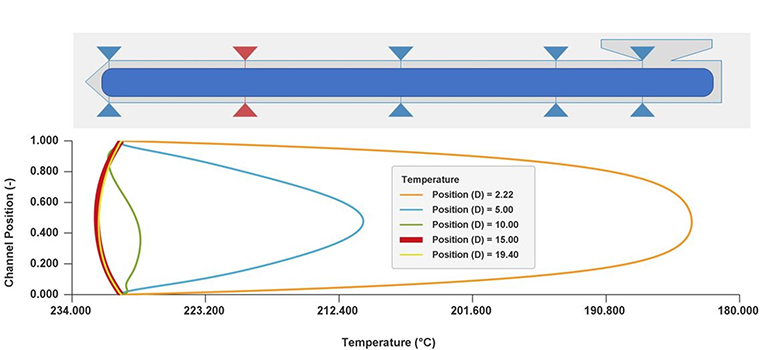
圖5與圖6分別為塑料在各個位置下的平均溫度與平均壓力。平均溫度可以作為調整各個加熱片溫度的依據;平均壓力則可以做為螺桿轉速與背壓設定的參考。
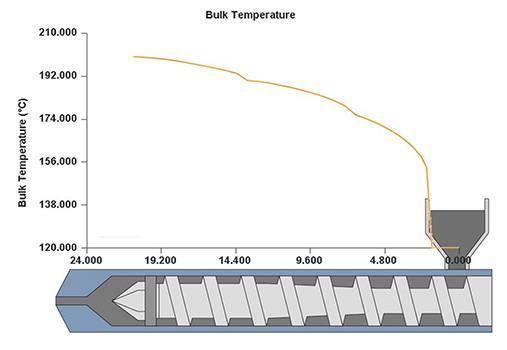
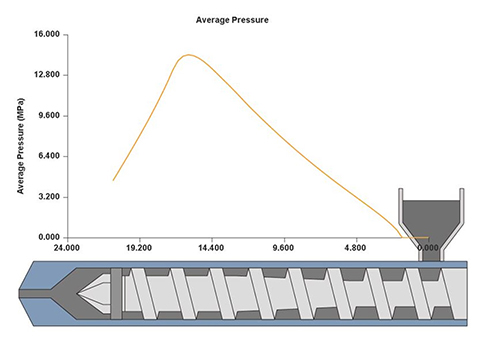
圖7顯示的是各個位置下,固態塑料所佔的比率。當數值降到零,代表塑料完全熔融;圖中可以檢視塑料在現行條件下能否完整地熔融。
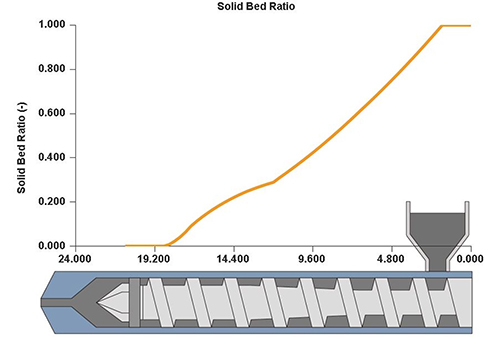
表1為模擬與實驗的比較,成型條件為螺桿轉速150RPM,背壓4.5MPa。最大溫升代表的是熔膠的最高溫與加熱片的差值,一般情況下,這個溫度的變化越小越好,代表塑料的溫度均勻,且幾乎等於加熱片的溫度。而塑化時間為螺桿到達指定計量位置所需的時間,此段時間最好接近且必須小於冷卻時間,原因是在塑化過程進行的同時,前一射也在模具中進行冷卻。若塑化時間小於冷卻時間太多,代表塑料在料管內停滯的時間很長,塑料有可能變質;若是塑化時間長於冷卻時間,則代表計量無法在開模前結束,影響到下一模次的生產。

結論
Moldex3D塑化分析功能可提供與評估螺桿作動行為,以及料管內部各個部位不同的壓力與溫度之變化。同時,我們可藉由參數設定與幾何結構的差異設定,觀察到這些設定在不同材料塑化時,所產生的溫升及壓降等行為變化,更快掌握塑膠射出的成型特性。
參考文獻
[1].F. Agassant, P. Avenas, J.Ph. Sergent, P.J. Carreau, “Polymer Processing Principles and Modeling “, Hanser, Munich (1991).
[2].Tadmor, Z. (1966). Fundamentals of plasticating extrusion. I. A theoretical model for melting. Polymer Engineering and Science, 6(3), 185–190.
[3].Chang, R.-Y. and Lin, K.-J. (1995) ‘The hybrid FEM/FDM computer model for analysis of the metering section of a single-screw extruder’, Polymer Engineering and Science, 35(22), 1748+.
[4].Altınkaynak, A., Gupta, M., Spalding, M. A., & Crabtree, S. L. (2011). Melting in a Single Screw Extruder: Experiments and 3D Finite Element Simulations. International Polymer Processing, 26(2), 182–196.