■恒申安科羅工程塑料
前言
從創新材料、成型技術、設計製造出發,安科羅在電動汽車輕量化發展之路上不斷探索。在上一期的雜誌中,我們討論了可持續性原材料和水輔成型技術在電動汽車的輕量化中發揮的作用,並與大家分享了安科羅在該領域內的應用案例。
本期將從設計製造角度出發,探討積層製造在電動汽車可持續性輕量化之路上的重要作用。
積層製造同樣可以實現輕量化和可持續性
積層製造又被稱為3D列印,通常被定義為基於3D體積模型分層構建部件的過程。
3大優勢:
- 更高效的產品設計
更少的材料創造出更大的強度,使多個部件可以合併為一個,與傳統工藝相比,這種方式可以完成不同的形狀設計。
- 更環保的製造工藝
大多數傳統製造技術都是做減法,這就意味著生產射出過程中必定會產生廢料,這些廢料無法完全回收利用,且回收的部分也需再加工;而積層製造工藝不涉及模具,也沒有雕刻廢料。
- 更短的創新及上市週期
積層製造使得快速迭代不受傳統製造工藝的原型設計限制,因此企業能以更快速度響應客戶需求,更高效利用材料、流程與人員,在更短時間內將產品推向市場。
而電動車的開發週期顯著要短與傳統燃油車,並且更新迭代速度也要快得多,這也是3D列印技術越來越受到電動車親昵的原因。
市場應用
案例1:寶馬量產車型的3D列印零部件
基於應用需求,安科羅為寶馬開發了用於3D列印的AKROMID® B3 ICF 40碳纖維增強尼龍。該材料以PA 6為基材進行碳纖維增強,拉伸模量可達30000 MPa,彎曲強度320 MPa,斷裂伸長率1.7%。
這款材料通過3D列印技術可以完成不同的形狀設計,目前已經用於寶馬量產車型的某些特定部件,可以減小零件體積、節省材料並減輕重量。
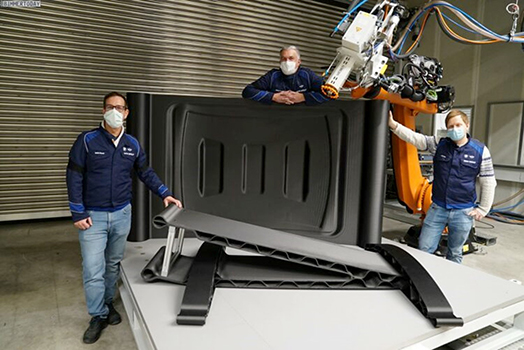
案例2:熔融沉積成型工藝(MDM工藝)
安科羅與伊之密、亞琛塑料加工研究所合作,開發的碳纖增強材料AKROMID® B3 ICF 30 9 AM,已被成功應用於一種新開發的熔融沉積成型工藝(MDM),為積層製造開創了全新可能。
這是一款30%回收碳纖維增強的PA6材料,碳足跡僅為4.9kgCO2eq/kg,為改善配料和喂料速度,該款材料提供直徑小於1mm的顆粒,以配合更精細的配料系統,大幅縮短停留時間。由於碳纖增強化合物的導熱性更好,會帶來更快的冷卻速度,加上高填充增強塑料不同批次之間的穩定性,實現了更出色的機械性能,及擁有更高速度的穩定製造工藝。
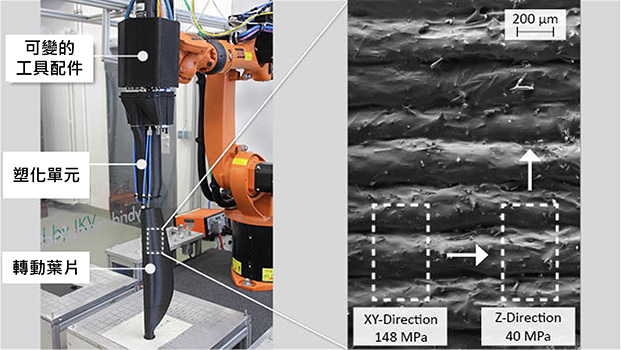