■型創科技 / 王海滔 應用工程師
PIM簡介與優勢
粉末注射成型(PIM)是一種製造微型高精度金屬或陶瓷部件的技術。在PIM中,金屬或陶瓷粉末首先與黏合劑混合,然後注射成型、通過燒結緻密化得到產品。PIM技術與傳統工藝相比,它具有精度高、組織均勻、性能優異、生產成本低等特點,能以經濟、量產的方式製造形狀複雜、高精度及高性能材質的小型機械零件,如微型齒輪、微型扇葉、微型醫療器具、汽車微裝置零件等。
PIM工藝生產難點
- 欠注:材料流動性差、製品厚度過小、溫度太低、注射時間太短和注射壓力太小都會造成成品無法充滿。
- 熔接痕:熔膠在注射過程中會因結構被分成若干股料流,再次匯合處可能出現線狀的痕跡,會影響成品的外觀與強度性能。當排氣不良、澆口位置不當、速度過慢、溫度過低都會進一步降低熔接線的品質。
- 氣穴:在注射過程中型腔內空氣未及時排出,被熔膠包裹或壓縮至流動末端,將引起成品表面氣穴,影響外觀品質與強度性能。常發生在產品厚度較大、模具排氣不良、工藝中射出速度過快等情況下。
- 黑線:在注射過程中由於剪切率的變化,造成金屬粉末與黏結劑分離,形成光澤度不佳的線狀缺陷。
- 開裂:製品在脫脂燒結後出現開裂的現象,可能是由於成型過程中產生應力堆積或應力分佈不均,殘餘應力在後續工藝中釋放導致。還有可能是製品厚度差異較大,不均勻的收縮應力導致斷裂。
- 變形:指的是成型製品冷卻後出現彎曲或扭曲,直接影響製品的外觀尺寸精度,甚至引起製品報廢。變形的原因多樣,如製品冷卻不均勻、內部積熱和頂出過早、製品厚薄不均和結構設計不合理等。
PIM成型品質與效率提升方向
- 煉膠配方:在選配黏結劑時考量產品結構的成型難度,維持胚狀功能需求下,優先選擇流動性更佳的。
- 成型設備:選擇金屬粉末專用射出機,配備專用的耐磨螺杆和料筒、含加熱控制的加長噴嘴、精準的螺杆位置控制、高回應電機等,給予更寬廣的工藝視窗,滿足精度高、效率好、速度快的需求。另外搭配自動化取件設備,充分保護脆性產品,防止自由下落造成損傷。
- 脫脂設備:目前市面上有一種混合脫脂爐,可同時滿足多種脫脂要求,包括單一的溶劑脫脂、蒸汽脫脂、冷凝蒸汽脫脂、脆化脫脂、虹吸脫脂,還可以同時進行多種工藝脫脂,實現黏合劑的快速脫出。如廠內生產工藝多樣化,該混合脫脂設備可以大大提升效率。
- 燒結設備:一般分為真空爐和連續爐,真空脫脂燒結爐是一種利用真空技術對材料進行燒結的間斷式(批次式)生產設備,用於金屬粉末注射成型製品的二次脫脂(熱脫)和燒結工藝環節。連續脫脂燒結爐是一種連續式生產設備,可使用於PIM製品從毛坯件進入爐內到燒結件出爐的全過程,並且可以不間斷連續運轉,特別適合於大批量產品的生產,有利於提升企業的規模化效應,顯著降低大批量產品生產的單位成本。
- 熱流道選用:優勢在於節約昂貴的粉末材料成本、避免冷流道粗大所造成的冷卻時間延長、減少了粉末混合料對模具的磨損及降低射出壓力、提高了模具使用壽命等。
- 使用模流分析技術:預先分析產品設計與模具設計的潛在問題,預測外觀缺陷、應力分佈等。把源頭做好,節省時間與修模成本,提高生產效率。
總結
金屬粉末射出中每個製程環節都是極為重要的,要達成高密度、高精度、高強度、少後續加工的目的,每個環節都需非常仔細評估及研究,盡可能避免在脫脂、燒結後才發現缺陷,此時的金屬射料已經無法再回收利用。不能忽視在混煉、造粒、射出、脫脂、燒結熱處理,以及模具系統應力分佈這些重要環節的重要性,提早預防缺陷才是解決缺陷的最佳方法,以達高可靠度PIM產品高精度要求。
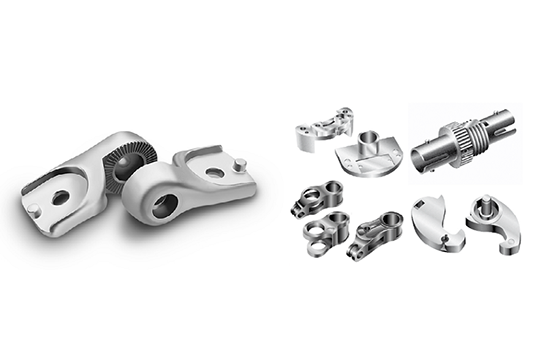