■科盛科技 研發二處 / 張權緯 經理 & 陳彥融 工程師
前言
在射出成型的產品開發與生產之過程中,設計工程師會使用CAE進行產品之可行性分析與優化分析,並透過模擬分析的方法預先排除在生產時可能發生的缺陷,優化產品設計,並採CAE虛擬試模之方式找到合適的生產用成型條件,預期可做為試模時之參考依據。
然而,當模具開發完成準備進入產品量產階段,製造端受限於CAE分析資料取得不易,常依據自身經驗來決定試模條件,若遇到新產品或新材料時,受限於個人經驗,有時會無法有效率的完成試模,致使試模時間增加。且若重要之試模經驗沒有被有效的保存與提供給後續成型與設計工程師進行參考時,也會導致試模經驗無法被保存且設計與製造端的生產條件差異也會越來越大。因此,當設計與製造之雙向資訊無法有效的傳遞與溝通時,設計與製造端的開發通常是各自作業,導致兩端的資訊斷層越來越大,嚴重時甚至會延滯產品的上市時間。
Moldex3D與FANUC透過整合之操作流程,讓模流分析結果可快速與便利的一鍵式傳送給製造端,讓成型工程師可參考此條件快速地展開試模流程,從而找出最合適的生產條件,減少試模時間,協助順利的完成在面對新材料或新產品時的挑戰。當雙向之資料可容易進行交換時,試模數據就可容易的保存,重要資料均會存放於系統中,可作為後續產品開發或產品製造時的重要參考資訊。因此,當完成設計與製造端的整合時,兩個階段的工作與資訊流程可完整被串起與交流,進而創造出智慧化的射出成型生產流程。
設計與製造之整合
Moldex3D與FANUC ROBOSHOT射出機的整合流程中,雙方為透過Moldex3D iSLM與FANUC ROBOSHOT LINKi2進行資料交換,其中iSLM與LINKi2均可運行於客戶端之私有雲中,確保重要資料的安全與機密性。設計工程師於地端完成Moldex3D分析,並可將分析結果上傳iSLM,而在試模現場之成型工程師可透過ROBOSHOT LINKi2,直接於機台控制器上開啟與iSLM整合功能,即可在不需增加任何設備的情況下,直接於機台上查看CAE分析結果與進行雙向資料交換,使得設計與製造端的資料可以無縫接軌,進而達到設計與製造之完美整合,相關流程如圖1所示。
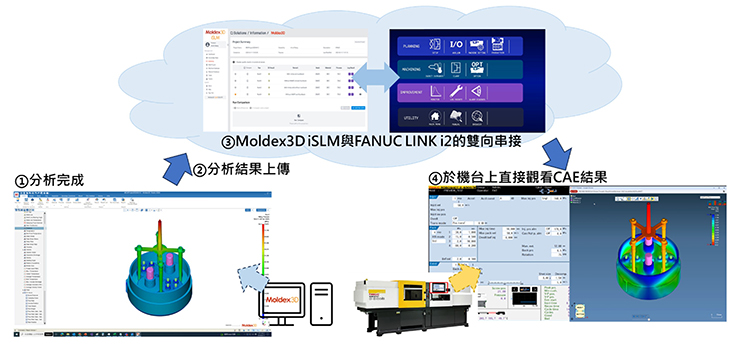
應用情境
使用者可於控制器上直接開啟iSLM,並開啟將要進行試模之分析結果,所有於iSLM內可以查看的分析結果,例如流動波前結果、分析射出壓力曲線等,均可於控制器上直接查看,以便於透過CAE分析結果了解可能之產品生產情況。
若要了解產品在不同螺桿位置所對應之流動充填結果,亦可直接在控制器介面進行設定預定要查看的短射位置,即可直接控制模擬顯示結果,在試模前即可了解產品可能之短射情況,如圖2所示。
當成型工程時了解CAE之分析後,要開始進行試模時,可一鍵式的快速將成型條件由CAE端傳送到設計端,作為第一次試模之參考條件,如圖3所示。由於CAE之分析結果是依據產品、材料與機台特性下所產生之分析結果,因此分析優化時所使用之成型條件已高度符合實際可能之生產情況,採用此成型條件可由接近實際情況之方式開始試模,而非傳統之試模方式,因此採用此條件可加快試模效率與降低試模成本。
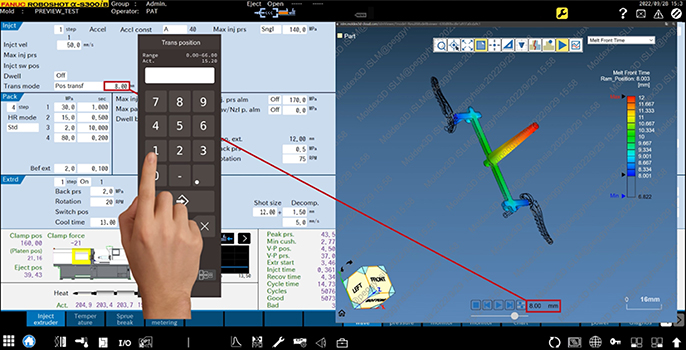
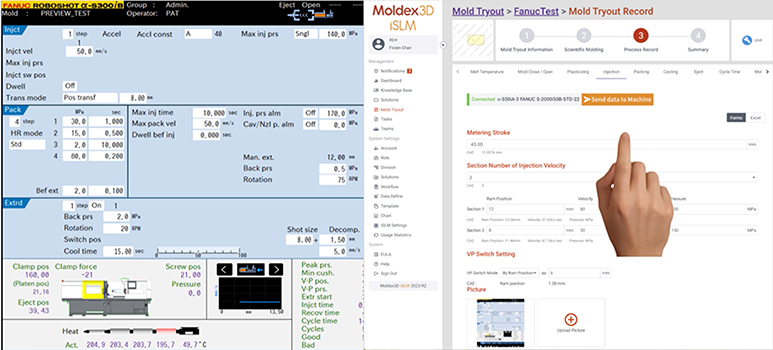
成型工程師依據最終產品品質進行成型條件微調後,亦可透過一鍵式的成型條件傳送方式,讓在製造端微調後之參數傳送至CAE端,除了將重要的試模結果與經驗保存於iSLM中,亦可讓後續之成型工程師或設計工程師當遇到類似之產品時有參考依據,加速研發與生產速度。
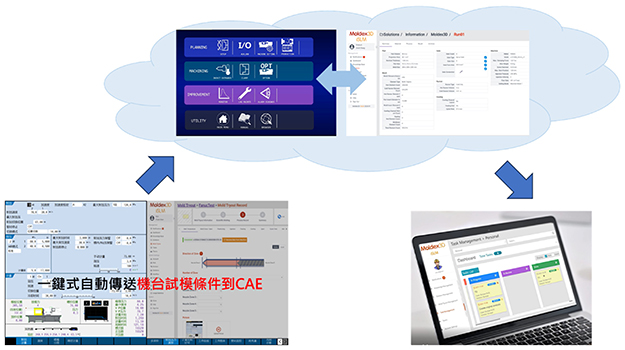
結論
當完成設計與製造端的整合,兩個階段的工作與資訊流程可完整串接,試模前透過模流分析結果成型工程師可快速與便利的察看分析結果,且第一次試模之成型條件亦可便利的傳送給製造端,射出成型工程師即參考此條件快速地展開試模流程。
透過此系統,試模之重要資料可容易的被保存於雙方系統中,可作為後續產品開發或產品製造時的重要參考資訊,進而協助使用者順利完成在面對新材料或新產品時的生產挑戰,創造出智慧化的射出成型生產流程。