■型創科技 / 王海滔 應用工程師
前言
在射出成型過程中,噴射痕(Jetting)是一種常見的表面缺陷,也被稱為噴流痕、放射紋或蛇形紋。它的形成主要是因為熔融態的聚合物在高速通過噴嘴、流道或澆口等流量限制區域時,由於流速過快,造成噴射形態,先進入空腔導致聚合物急速冷卻,與後續填充的熔膠難以完全融合,從而在射出件表面形成類似蛇般蜿蜒的粗糙編織紋,這不僅影響產品的美觀,還可能導致光澤差異和色差問題。
噴射痕形成原因
當熔融塑料通過狹窄的噴嘴、流道和澆口等區域後,如果突然進入一個開放且較寬的區域,熔體前端的速度可能會急劇下降,而後續熔體仍以高速推進,這種速度差異可能導致蛇形紋的產生。
- 澆口位置選擇不當
如果澆口位置設置不合理,熔體從狹小的進膠點突然進入寬闊的模具型腔時(厚壁側),容易形成噴射,進而導致蛇形紋的出現。
- 不合理的澆口設計
過小的澆口尺寸會導致熔膠流動受阻,增加噴射的可能性。
- 射出工藝參數不適宜
注射速度過快、注射壓力過高、保壓切換不當等工藝參數設置不當,也可能導致熔體在模具內的流動不穩定,形成蛇形紋。
- 材料特性不匹配
使用的材料流動性不足或與模具設計不匹配,也可能導致熔體在流動過程中形成蛇形紋。
- 模具溫度控制不當
模具溫度過高或過低都會影響熔體的流動狀態,進而導致蛇形紋的產生。
- 射出機性能不佳
機器穩定性差、控制系統精度不高、設備存在磨損、清潔不澈底等狀况下,可能會影響熔膠的流動,無法準確捕捉對應澆口的螺杆位置進行降低射速,增加噴射痕的風險。 - 環境因素
如環境溫度低,熔膠冷卻速度加快,增加了噴射痕的形成機率。或是高濕度環境可能會影響熔膠的流動性和冷卻速率,間接導致噴射痕的產生。
解決措施
- 優化模具設計,重新設計澆口和流道系統,適當增加澆口的尺寸或改變澆口的位置,使熔體流動更加平穩,減少流速的劇烈變化,並改善排氣系統。
- 調整工藝參數,如適當降低注射速度和壓力,延長保壓時間,確保熔體在模具內流動穩定。
- 選擇更適合模具設計和工藝要求的材料,或調整材料的配方,以改善其流動性能,並控制合適的熔膠溫度。
- 合理控制模具溫度,確保熔體在模具內具有良好的流動性,避免因溫度問題導致的熔體流動不穩定。
- 改進產品設計,盡可能簡化產品幾何形狀,設計均勻的壁厚,以減少熔膠流動難度。
- 提升射出機性能,選擇穩定性好、控制精度高的射出機,並進行定期維護。
- 適應環境因素,控制生產車間的溫度和濕度,以減少環境對熔膠冷卻的影響。
- 定期維護保養,定期對射出機和模具進行保養,確保設備處於最佳工作狀態。
總結
解決射出成型中的蛇形紋問題需要綜合考慮材料特性、模具設計、工藝參數以及設備條件等多個因素。通過精確控制這些變量,可以有效避免蛇形紋的出現,從而提高射出產品的整體質量。在實際操作中,應根據具體情况靈活調整策略,以達到最佳的成型效果。
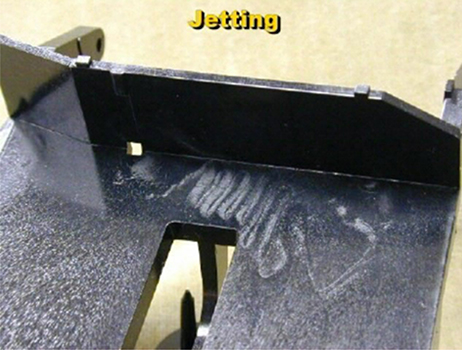
